Designing and sizing a shell and tube heat exchanger is a meticulous process that requires a blend of engineering insight and practical experience. A pivotal component in industrial applications, these heat exchangers are integral in facilitating efficient thermal energy transfer. It's crucial to approach the design with a focus on achieving optimal performance while ensuring longevity and reliability.
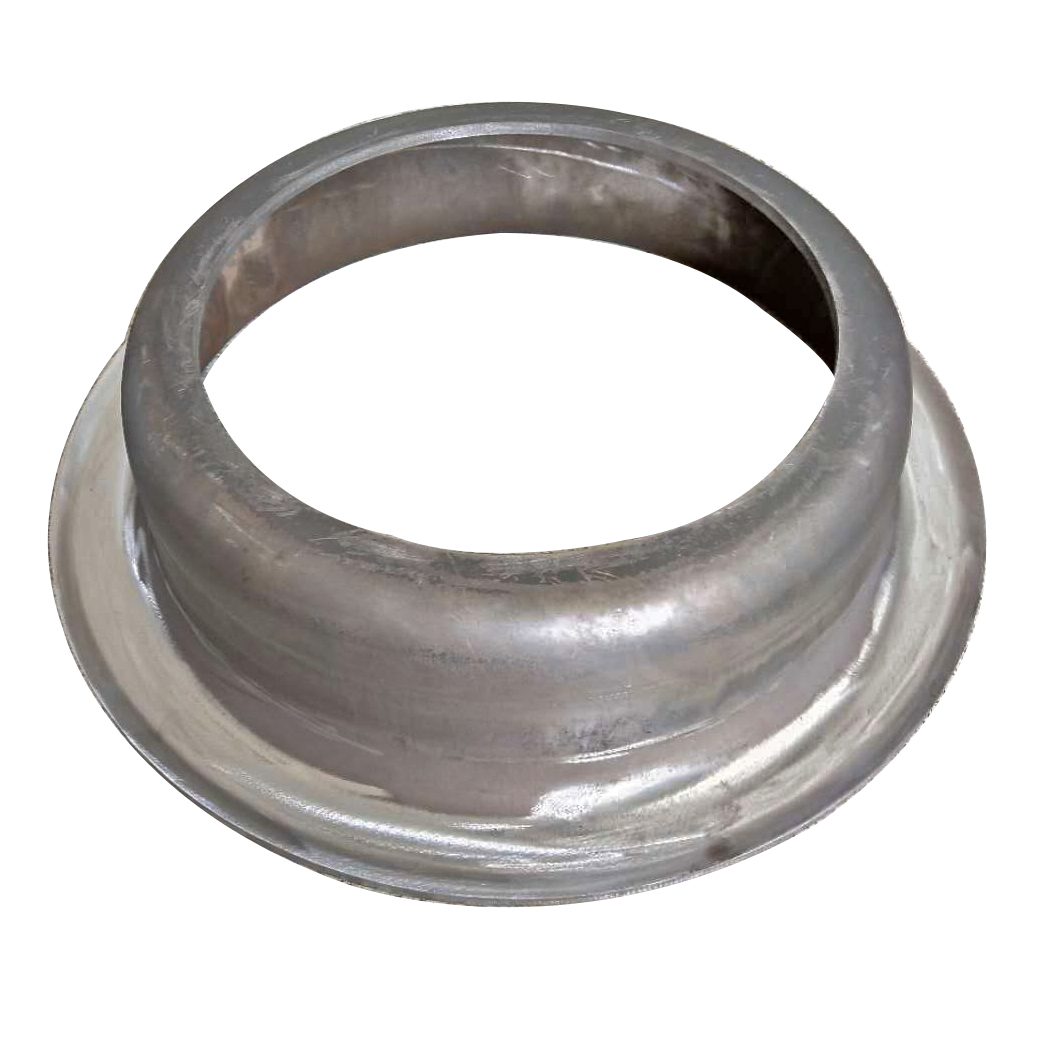
Understanding the fundamentals of shell and tube heat exchangers is key. These devices comprise a series of tubes, one set—usually referred to as the tube bundle—contained within a larger shell. The primary function is to allow heat transfer between two fluids one flowing through the tubes and the other around the tubes within the shell. This configuration not only maximizes surface area contact but also supports high pressure and temperature usage, making it versatile across various industries, from petrochemicals to HVAC systems.
The journey of sizing a shell and tube heat exchanger starts with detailed input from end-users about the fluid characteristics—temperature, pressure, flow rates, and thermal properties. Gathering accurate data here is paramount; subtle discrepancies can lead to design inefficiencies or operational failures. It's beneficial to involve a cross-disciplinary team including chemical engineers and mechanical experts to validate these parameters, fostering an environment of Expertise and collation of diverse knowledge pools.
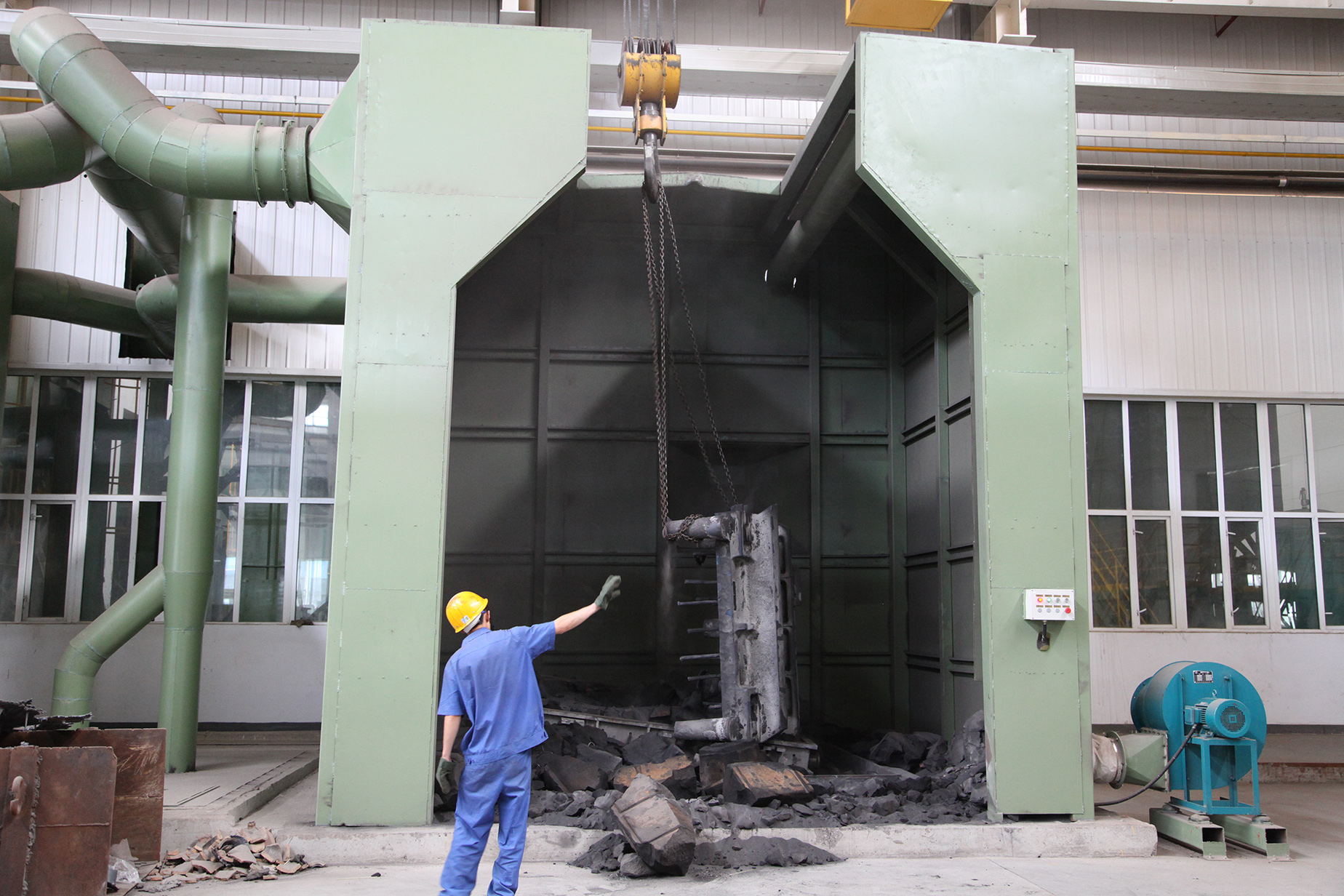
Next, leverage software tools grounded in heat transfer principles. These advanced programs simulate heat exchanger performance, offering real-time insights and precise data analysis. It's essential, however, to supplement software outputs with empirical correlations derived from hands-on industry Experience. This dual approach fortifies the design process against unforeseen practical challenges and enhances the system’s robustness.
sizing shell and tube heat exchanger
Material selection is another critical stage. The choice of materials impacts both the heat exchanger’s lifespan and its efficiency. Corrosion resistance, thermal conductivity, and mechanical strength should guide the selection process. For example, stainless steel, with its excellent anti-corrosive properties and thermal resilience, is often preferred in industries dealing with aggressive fluids or high temperatures. Consulting material sciences experts can provide the Authoritativeness needed to make informed decisions.
Pressure drop calculations ensure that the fluid flow through the exchanger is within acceptable limits, preventing excessive energy consumption. It's advantageous to conduct these calculations with precision and regard for any potential losses in system pressure. Trustworthy design anticipates and mitigates risks of pressure drop without compromising heat transfer efficacy.
Finally, consider maintenance and operational efficiency. A well-sized shell and tube heat exchanger should facilitate easy cleaning and maintenance access, reducing downtime. Regular inspections and upkeep align with Trustworthiness, ensuring that these heat exchangers operate optimally throughout their intended lifespan. Documenting each design decision and maintaining transparent records enhances trust and provides valuable insights for future projects.
In summary, sizing a shell and tube heat exchanger is a complex, multidisciplinary task that demands a balance between theoretical knowledge and practical application. It’s a process informed by expertise and guided by principles of engineering reliability. Adhering to these processes not only enhances the performance and efficiency of the devices but also reinforces the integrity and trustworthiness of the end product in real-world applications.