Aluminum die casting stands at the forefront of modern manufacturing, offering unrivaled precision and strength in the production of complex components. This process, using molds made from high-grade steel, allows for the production of durable and intricately detailed products that serve a myriad of industries from automotive to electronics. With decades of experience, experts can attest to its numerous advantages over alternative methods such as plastic molding or simple forging.
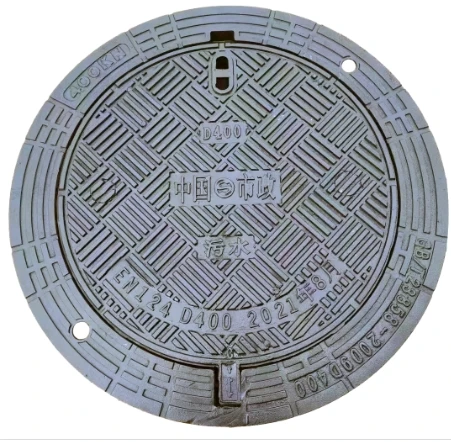
The hallmark of aluminum die casting is its ability to create detailed parts that require minimal machining. In a recent case study at a leading automotive component manufacturing facility, the switch from heavier steel parts to aluminum die-cast components resulted in a 20% reduction in overall vehicle weight, thereby increasing fuel efficiency without compromising on strength or durability. Such real-world applications highlight the transformative impact of die casting in contributing to more sustainable automotive manufacturing.
Expertise in die casting doesn't just reside in understanding the basic mechanics, but in mastering the nuances of temperature control, mold design, and alloy selection. These elements are crucial for preventing common defects like porosity and ensuring that the final product meets stringent industry standards. Industry-leading manufacturers invest heavily in training their technicians and engineers, ensuring that expertise translates into tangible benefits for the end-user, such as increased part longevity and reduced failure rates.
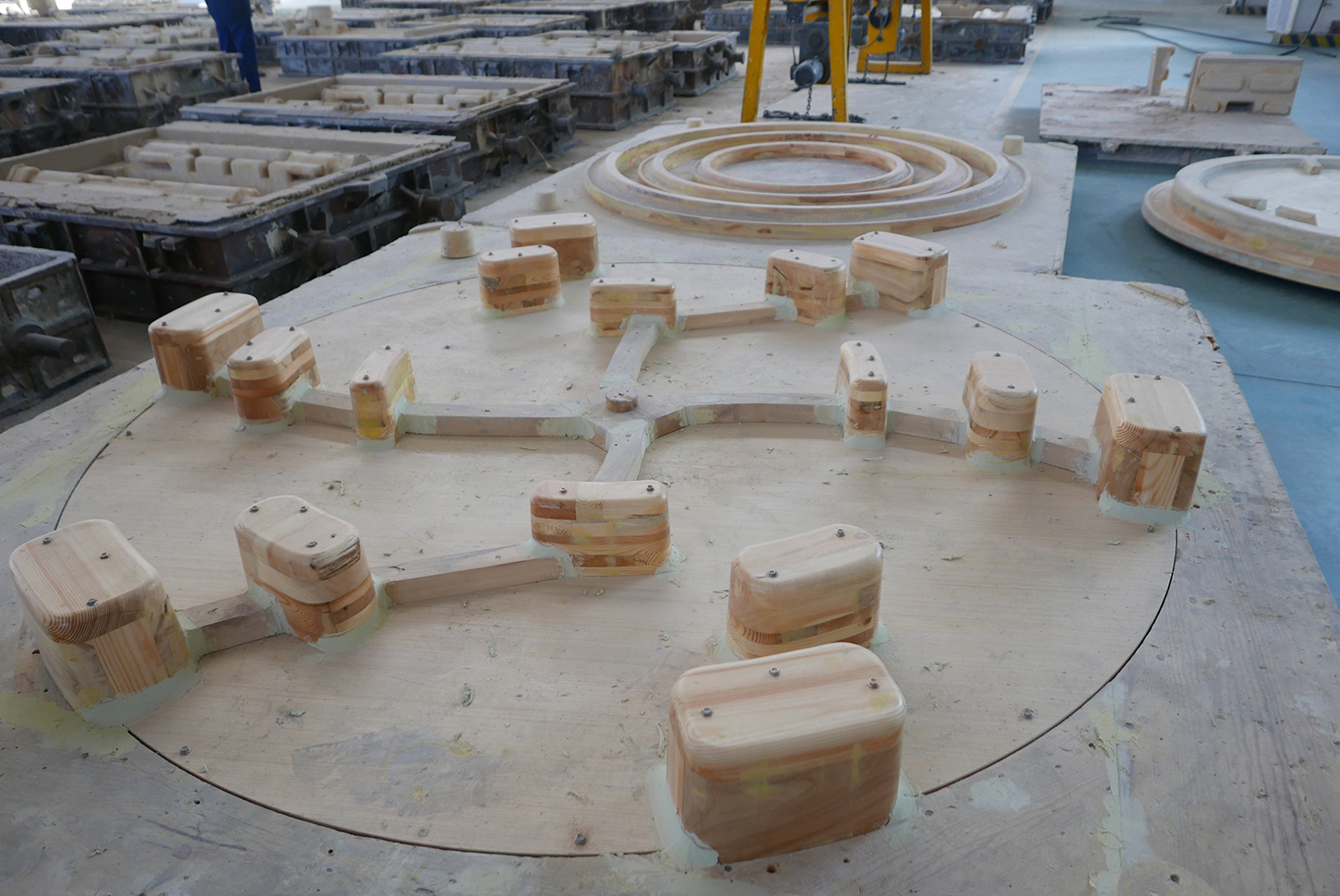
aluminum die casting
When it comes to authoritativeness, few manufacturing processes have been studied and optimized as thoroughly as aluminum die casting. Industry giants such as Tesla and General Motors have standardized the use of die-cast aluminum components due to the method's proven reliability. Scholarly articles published in journals of manufacturing science cite robust data, illustrating die casting's superior tensile strength and corrosion resistance when compared to traditionally manufactured parts. Such scholarly references cement the process's standing as a cornerstone of quality manufacturing in sectors demanding the highest standards.
Trustworthiness, a critical aspect of any manufacturing process, is inherent in aluminum die casting's value proposition. The process is governed by stringent international standards, which provide a framework ensuring continuous improvement and quality assurance. Quality control measures, such as x-ray inspection and automated dimensional verification, verify that each product meets exact specifications before it leaves the factory floor. Leading firms in the industry frequently perform audits to certify that their processes comply with ISO and other relevant certifications, providing added assurance for clients.
Aluminum die casting has undoubtedly revolutionized the creation of robust, lightweight components, making it indispensable across industries aiming for efficiency and excellence. The process not only exemplifies advanced engineering and scientific principles but also underscores the commitment to quality and innovation, providing a reliable solution to meet the most demanding industrial needs. For companies seeking to optimize production both in cost and quality, embracing die casting technology offers a forward-thinking path into the future of manufacturing innovation. This trusted method continues to evolve, integrating cutting-edge research and development to meet the challenges of tomorrow's increasingly demanding market.