Water glass sand casting has emerged as a cornerstone in the realm of metal fabrication, revolutionizing how intricate metal components are created with precision and efficiency. Rooted in the ancient art of casting, this advanced technique offers a blend of tradition and modern innovation, making it a go-to method for industries ranging from automotive to aerospace. The process involves the use of a sodium silicate solution (commonly known as water glass) as a binder for the sand mold, providing enhanced mold strength and environmental benefits compared to traditional casting methods.
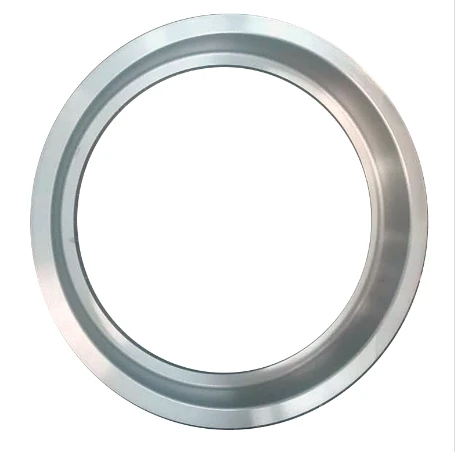
The primary advantage of water glass sand casting lies in its ability to produce complex geometries with exceptional surface finish. This feature is particularly beneficial for industries that demand high precision and dimensional accuracy. By utilizing fine sand particles bonded by water glass, manufacturers can achieve smoother surfaces and sharper details, reducing the need for post-casting machining and finishing. This not only minimizes production time but also lowers costs, making it an economically favorable option for large-scale production.
In practice, the water glass sand casting process begins with the preparation of the sand mixture. The sand, often silica-based, is combined with a liquid sodium silicate binder in precise proportions. Once thoroughly mixed, this blend is molded around a pattern, which reflects the shape of the desired final product. The mold is then exposed to carbon dioxide gas, which reacts with the sodium silicate to harden the sand, forming a rigid mold suitable for metal pouring.
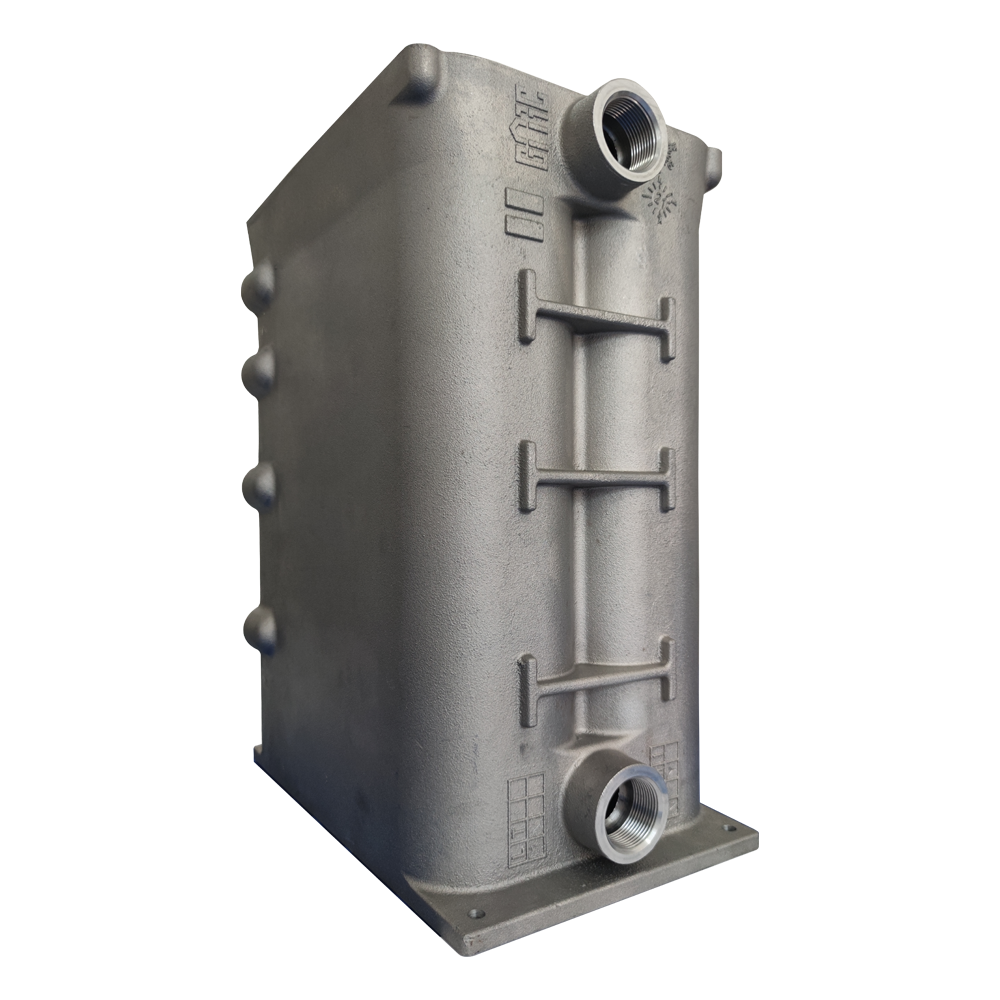
One of the key environmental benefits of this technique is its reduction in emissions compared to traditional sand casting methods that may rely on resins emitting volatile organic compounds (VOCs). Water glass sand casting results in lower emissions, making it a sustainable choice for companies committed to reducing their environmental footprint. Plus, the sand can often be reclaimed and reused after the casting process, enhancing the method’s eco-friendliness.
In terms of expertise, executing the water glass sand casting process requires comprehensive knowledge of both materials and techniques. An experienced foundry specialist understands the subtleties of controlling the mold permeability and strength, which are crucial to preventing defects such as blowholes or warping in the final product. Mastery over the regulation of CO2 flow during the curing stage is vital,
as it directly affects the mold’s solidity and the casting’s integrity.
water glass sand casting
Industries capitalizing on this technology often highlight its superiority in producing short-run, customized parts without compromising on quality. For example, the automotive industry often requires the rapid manufacturing of prototype parts before mass production. Water glass sand casting allows for quick iterations and modifications, offering flexibility while ensuring the prototypes mirror the performance and appearance of mass-produced components.
Experts argue that the reliability of water glass sand casting adds a layer of trust for manufacturers, minimizing the risks associated with high-volume errors and providing a level of consistency that is hard to achieve with other casting methods. This trusted reliability ensures that deadlines are met without sacrificing quality, making it popular in industries where timeliness and precision are critical.
While the method offers numerous benefits, it should be noted that it does come with challenges, such as the need for specialized equipment to handle and dispose of sodium silicate safely. Companies considering this casting method must invest in appropriate training for their workforce to optimize process efficiency and maintain safety standards.
Overall, water glass sand casting stands as an authoritative process in the metal casting domain, offering precision, sustainability, and cost-effectiveness. As industries continue to seek efficient methods to produce high-quality components with intricate designs, the relevance and demand for expertise in water glass sand casting are expected to grow exponentially, solidifying its role as a pivotal technique in the modern manufacturing landscape.