Behind the walls of every industrial facility, where machines tirelessly work day and night, lies an unsung hero - the high temperature heat exchanger. This critical component, often overshadowed by more visibly dynamic machines, holds a position of immense importance in thermal management and energy conservation. Through real-world applications, expert insights, and technical analysis, we explore how high temperature heat exchangers are revolutionizing industries across the globe.
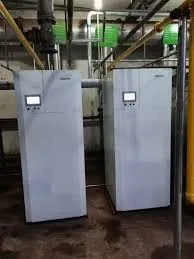
High temperature heat exchangers are crucial to industries ranging from petrochemicals to power generation, allowing for significant energy recovery and operational efficiency. At the core of their function, these devices transfer heat between two or more fluids without mixing them. In industries where the operating temperatures soar to extremes, these heat exchangers are indispensable for managing intense thermal loads.
Professionals like Dr. Lara Thompson, a seasoned mechanical engineer in the field of thermal dynamics, have seen firsthand the profound impact these devices can make. Dr. Thompson notes, In refineries and chemical plants, high temperature heat exchangers can recover up to 60% of waste heat, translating to millions in energy savings annually. Such energy recovery not only reduces operational costs but also contributes to sustainability by minimizing carbon footprints.
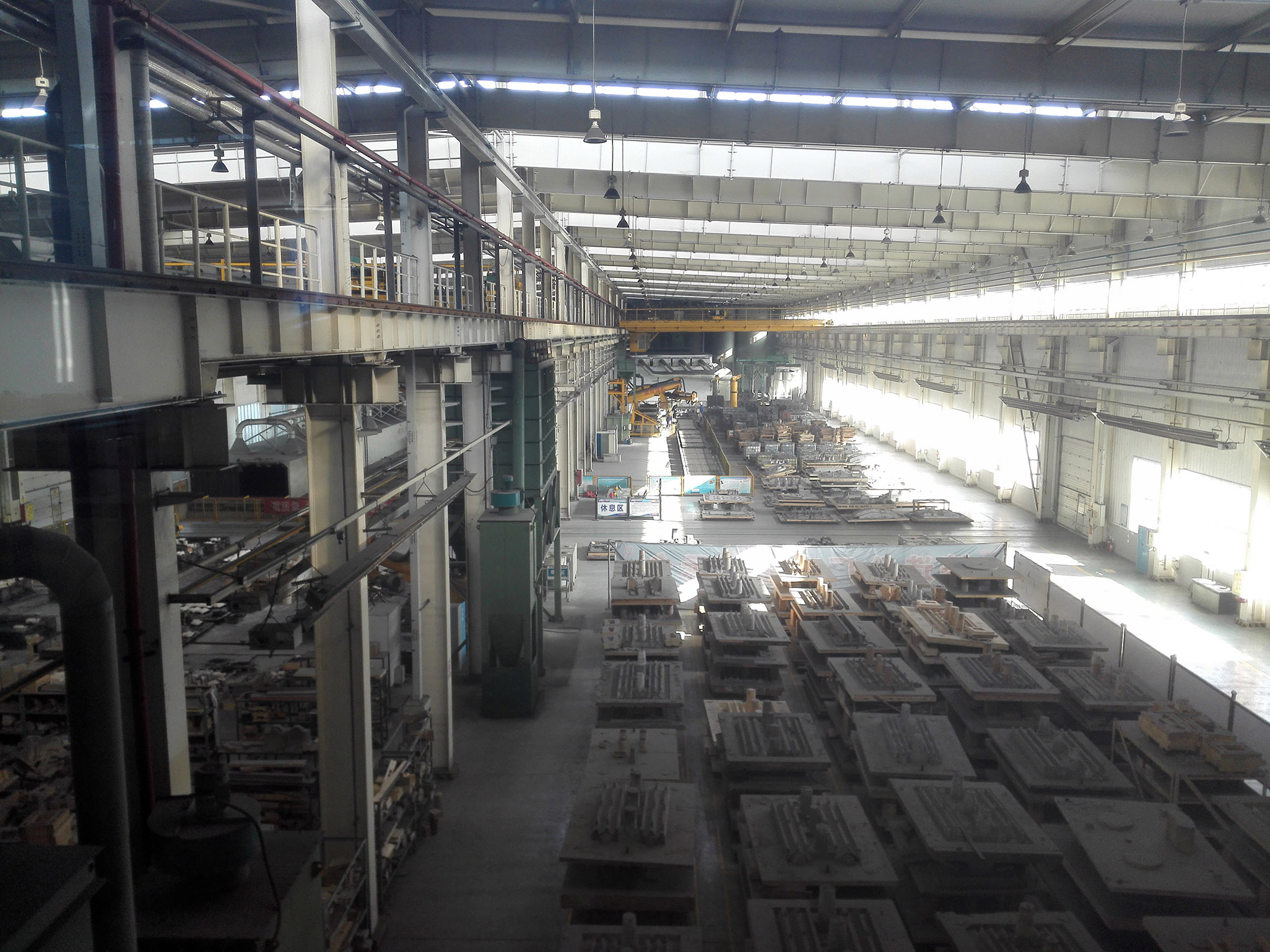
The expertise required in designing such heat exchangers is substantial. Material selection stands paramount, as the exchangers must withstand corrosive environments and extreme thermal stress without degrading. Engineers like Dr. Thompson often rely on materials such as Inconel and Hastelloy, known for their exceptional resistance to heat and corrosion. More recently, advancements in ceramic composites have offered promising alternatives that can operate at even higher temperatures with lower susceptibility to thermal fatigue.
Authoritative reviews from industrial reports affirm the necessity of these advanced materials. According to the Global Heat Exchanger Market Analysis 2023, the use of high-grade alloys and composites is anticipated to drive the market significantly, ensuring greater durability and efficiency. This resilience is particularly crucial in high-stakes environments where equipment failure could lead to catastrophic consequences.
high temp heat exchanger
Trust in high temperature heat exchangers is not just built on materials and design but also on rigorous testing and compliance with strict industry standards. International standards, like those from the American Society of Mechanical Engineers (ASME), provide comprehensive guidelines ensuring safety and performance. Companies engaging in compliance with these standards, such as Investing in testing protocols that simulate extreme operational conditions, demonstrate a commitment to reliability and quality.
In practice, for a facility manager like Robert Eason at a major petrochemical company, these standards mean peace of mind. When we install ASME-certified heat exchangers, we're not just buying equipment. We're investing in operational stability and safety. Eason’s experience reflects the broader industry confidence in compliant products, underscoring the critical nature of standardized manufacturing and testing processes.
Moreover, the integration of cutting-edge technology has streamlined heat exchanger operations. Modern systems now incorporate advanced monitoring sensors that provide real-time data analytics on temperature differentials and flow rates. Such innovations allow for predictive maintenance, where potential faults are identified and rectified before they escalate into significant malfunctions, thereby enhancing the longevity and reliability of the exchangers.
Looking forward,
experts predict an exciting horizon for high temperature heat exchangers. The transition to sustainable sources of energy, such as Concentrated Solar Power (CSP) and geothermal systems, will rely heavily on the efficiency of heat exchangers to convert high thermal inputs into usable power. In these systems, heat exchangers are pivotal in harnessing natural heat sources, converting them into electricity with unparalleled efficiency.
In conclusion, high temperature heat exchangers are vital components underpinning the functionality and efficiency of modern industrial systems. The convergence of expert engineering, authoritative material choices, steadfast adherence to standards, and innovative technology contributes to their growing prominence in energy-intensive environments. As industries evolve towards greater sustainability and operational prowess, the investments in advanced heat exchanger technology not only signify financial prudence but also a commitment to a more energy-efficient world. As we continue to push the boundaries of temperature and pressure, these devices will remain at the forefront, delivering performance that is not just efficient but transformative.