Tubular condensers, an integral component in thermal systems, have significantly evolved over the years, embodying advancements in both design and efficiency. For industries reliant on heat exchange processes, selecting the right tubular condenser can enhance operational efficiency, reduce energy consumption, and ensure long-term system reliability. This article delves into the intricacies of tubular condensers, drawing from real-world experiences and expert insights to provide authoritative guidance for industry professionals.
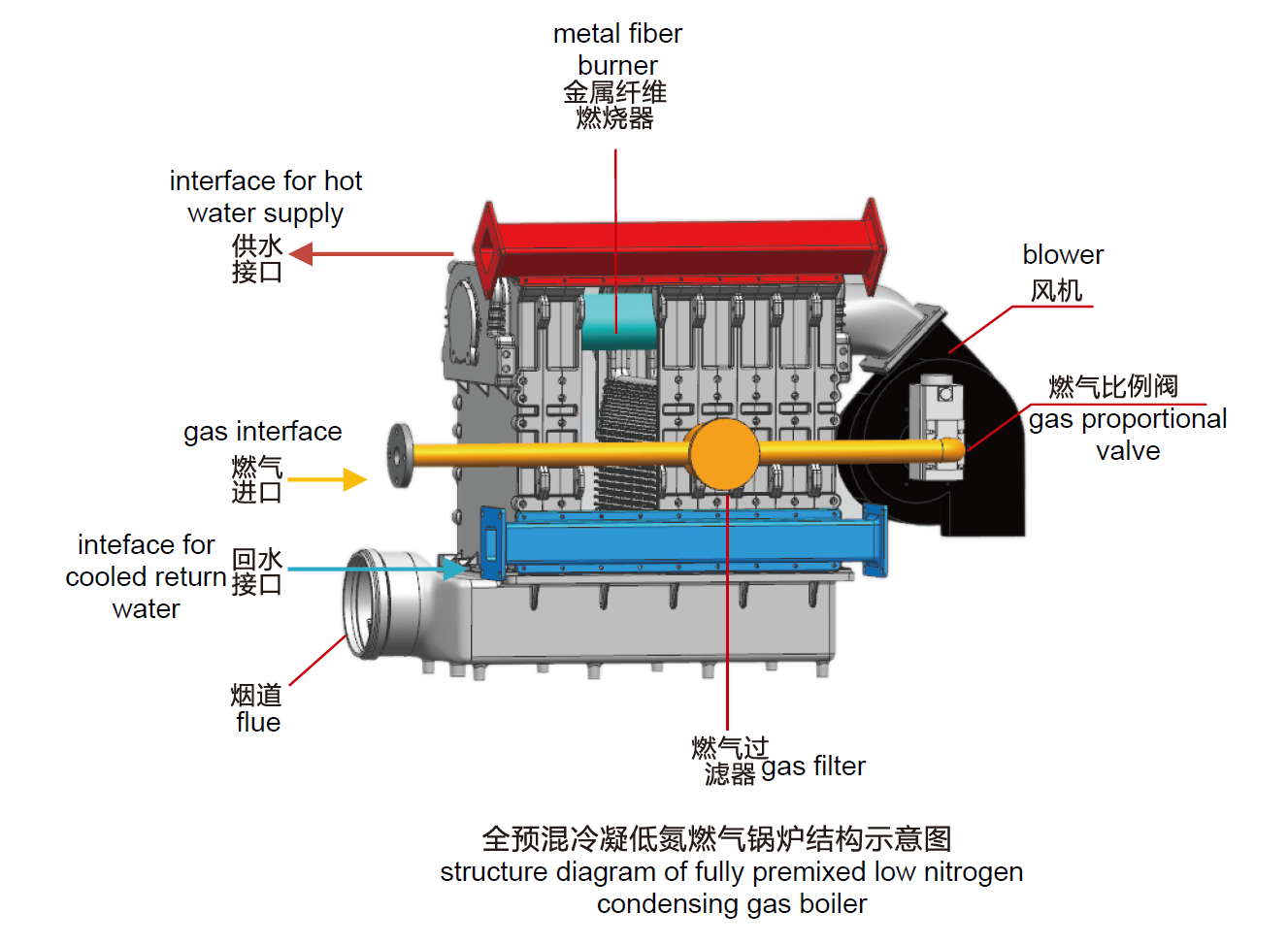
A tubular condenser operates on the principle of indirect heat exchange, where fluids or gases pass over a series of tubes through which coolant flows. This design is renowned for its versatility, accommodating a wide range of industrial applications, from power generation to chemical processing. The choice of materials for tubes—often copper, stainless steel, or titanium—depends not only on the specific thermal requirements but also on the nature of the fluids being processed.
Through years of hands-on experience, industry experts have consistently advocated for robust material selection.
The choice profoundly impacts the condenser's lifespan and efficiency. For instance, while copper offers excellent thermal conductivity, its susceptibility to corrosion in environments with sulfuric or acidic components necessitates careful consideration or an alternative material like titanium with superior resistance properties.
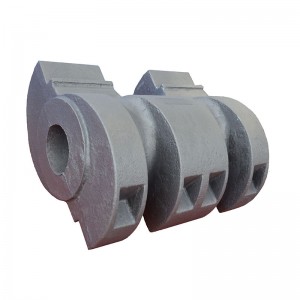
An essential aspect of tubular condenser systems is their adaptability. Experts emphasize that while standard models are available, custom configurations often yield the best outcomes. Tailoring the tube diameter, length, and arrangement to the specific needs of an operation can markedly improve performance. This customization reduces pressure drops and optimal heat transfer rates, ultimately contributing to energy conservation—a critical factor for reducing operating costs in energy-intensive processes.
tubular condenser
The reliability of tubular condensers also hinges on maintenance practices. Trustworthiness in performance often correlates with proactive upkeep. Routine inspections, facilitated by advancements in diagnostic tools, allow for early detection of potential issues such as tube fouling or leaks. The insights from seasoned engineers suggest implementing a regular cleaning schedule to mitigate these risks and extend the equipment's operational longevity.
Recent technological advancements have propelled tubular condenser designs into a new era of efficiency. The integration of smart monitoring systems enables real-time data collection on performance metrics, allowing operators to make informed decisions regarding system adjustments. This innovative approach not only optimizes energy usage but also reduces the environmental footprint of industrial processes.
In terms of energy efficiency, tubular condensers boast impressive capabilities. By maximizing the surface area contact between the cooling medium and the fluid, these systems achieve high rates of heat transfer with minimal energy input. Industry practices underline the importance of regular energy audits to assess performance and identify opportunities for further efficiency improvements.
In conclusion, the strategic implementation of tubular condensers requires a blend of expert knowledge, practical experience, and technological innovation. By selecting the appropriate materials, customizing designs, and adhering to stringent maintenance protocols, industries can significantly benefit from improved performance and cost savings. As advancements continue, the role of tubular condensers will undoubtedly expand, solidifying their status as a cornerstone of modern industrial heat exchange solutions.