Choosing the best material for a heat exchanger requires careful consideration of various factors, which can significantly impact the performance and longevity of the equipment. Investing in the right material not only ensures high efficiency but also reduces operational costs in the long run.
Let’s delve into the best materials available and the criteria that drive their selection.
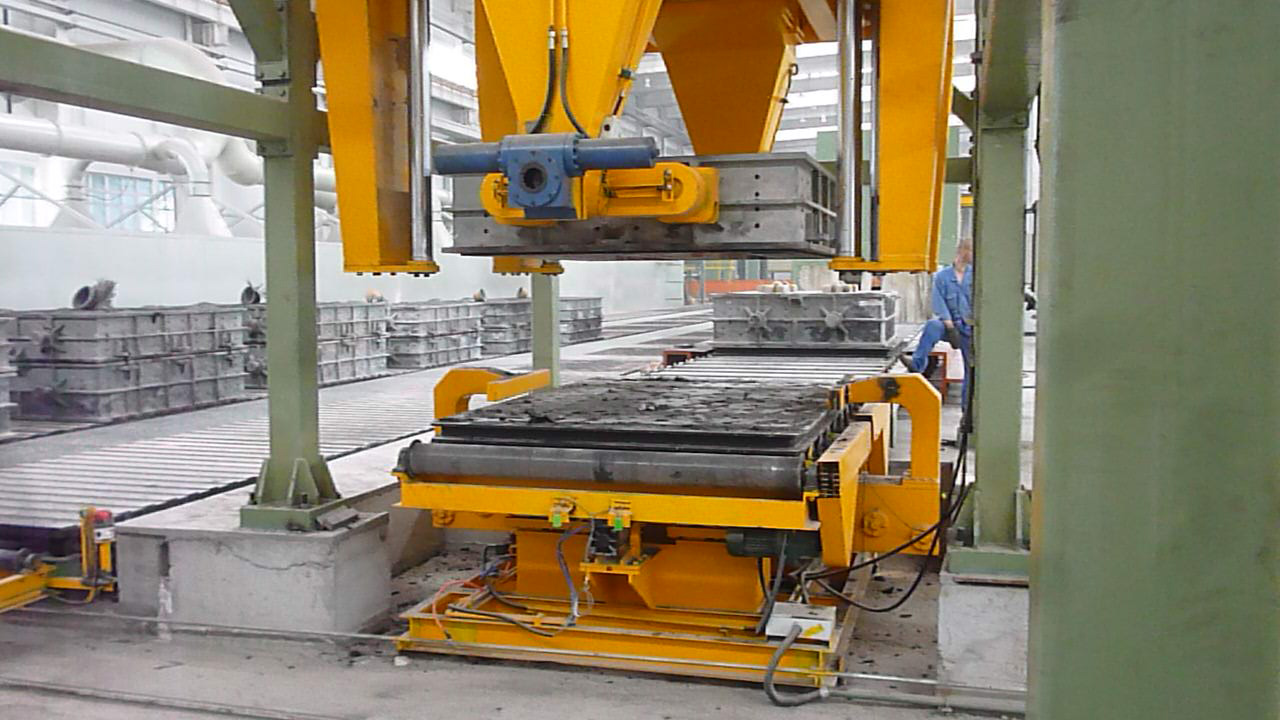
For industrial applications, stainless steel remains a popular choice for heat exchangers due to its exceptional corrosion resistance, thermal conductivity, and mechanical strength. Its ability to withstand high temperatures without losing its structural integrity makes it ideal for industries that require robust and durable solutions. Furthermore, stainless steel offers cost-effectiveness by minimizing maintenance needs and extending the lifespan of the exchanger.
However, copper is often considered a top contender for specific applications, given its superb thermal conductivity. This characteristic translates into faster and more efficient heat transfer, positioning copper as an excellent choice in HVAC systems or processes that demand rapid temperature adjustments. Yet, it’s essential to account for copper’s susceptibility to corrosion in certain environments, necessitating some protective measures or coatings.
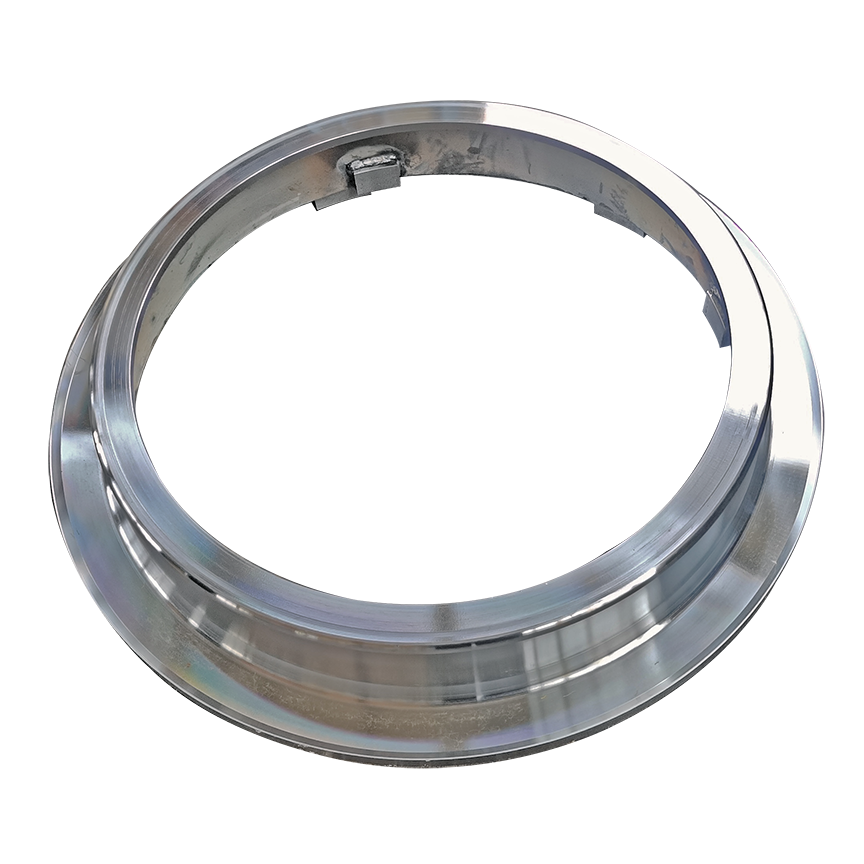
In scenarios where weight and space efficiency play crucial roles, aluminum emerges as an optimal material. Its lightweight nature without compromising thermal conductivity makes it an attractive option for space-constrained environments or mobile solutions like automotive and aerospace applications. Additionally, aluminum’s resistance to oxidation ensures longevity, although it may not be as robust as other materials in highly corrosive surroundings.
Titanium stands out in environments where aggressive corrosives are present, such as saltwater or chemical processing industries. Its unparalleled corrosion resistance and strength-to-weight ratio justify its premium cost. Despite its higher initial expense, titanium can offer significant savings over its life cycle by averting frequent replacements and maintenance operations, especially in extreme conditions.
best material for heat exchanger
For applications involving food and pharmaceutical processing, the choice often leans towards materials that maintain absolute hygiene and prevent contamination. Hence, nickel alloys, known for their resistance to bio-fouling and chemical reactivity, ensure compliance with stringent hygiene standards while maintaining performance efficiency.
Advancements in material science have also introduced advanced composites and ceramics in specific niche applications. These materials provide unique solutions where traditional metals may fall short, especially in high-temperature and high-pressure environments that demand exceptional material properties.
Selecting the best material involves an intricate balance between initial costs, operating environment, efficiency requirements, and end-use application. Engineers and designers must weigh these aspects to decide the most suitable option, ensuring that their choice not only meets immediate operational needs but also anticipates future requirements.
In conclusion, understanding the nuanced performance aspects of each material and their behavior in various applications is crucial. Consulting with material scientists, industry experts, and suppliers is recommended to tailor a solution that aligns with both performance expectations and budget constraints. As technologies and materials continue to evolve, staying informed about the latest advancements and market offerings is vital for making an informed decision that enhances the efficacy and lifespan of heat exchangers.