Double wall tube heat exchangers are revolutionizing heat transfer solutions across a diverse array of industries, offering unparalleled safety features and efficiency. These devices are engineered with dual-layered tubes that ensure optimal heat exchange while preventing any mixing of substances, thus safeguarding both operations and the environment.
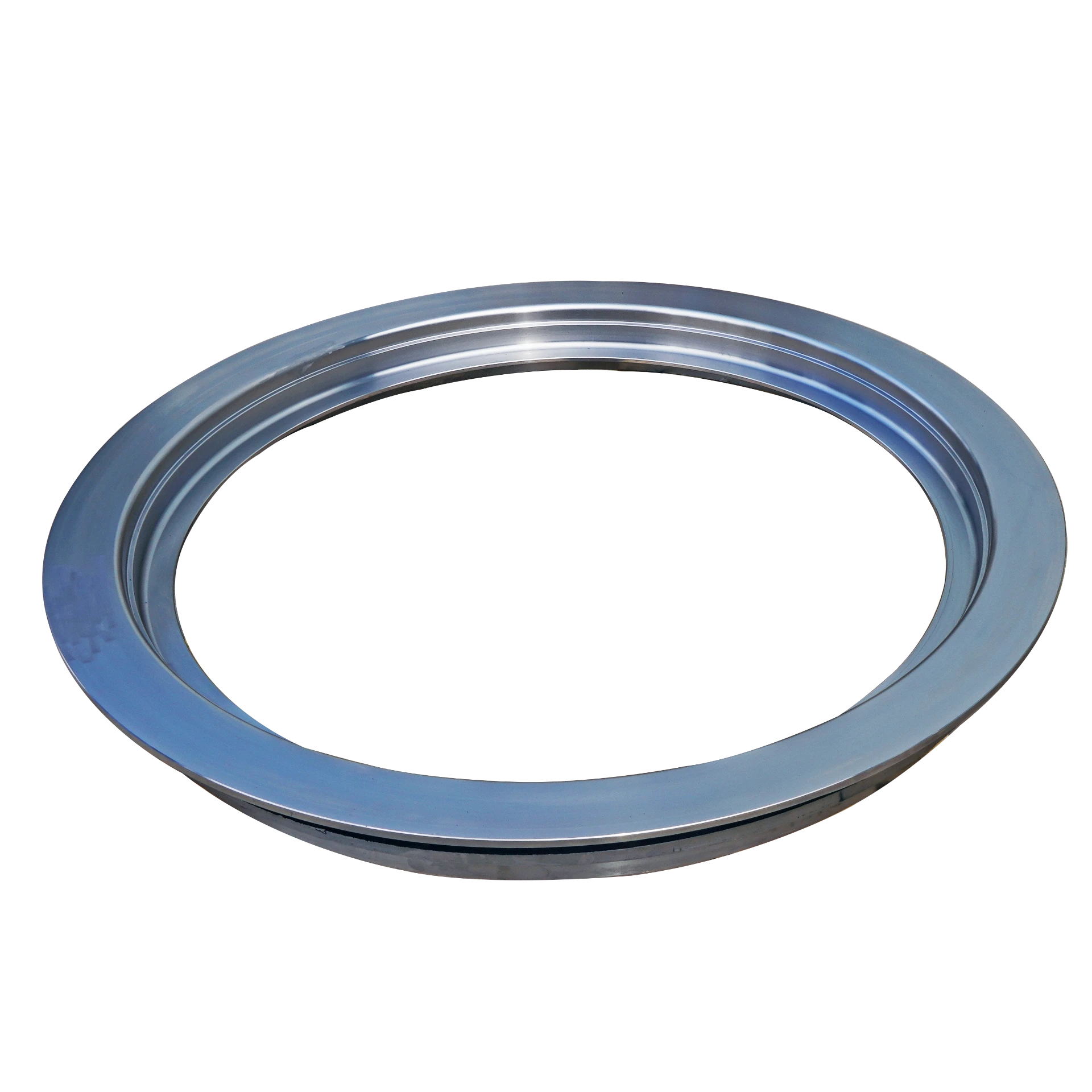
At the core of their design, double wall tube heat exchangers boast two concentric tubes. This ingeniously constructed double barrier prevents cross-contamination, a critical factor when dealing with hazardous or sensitive fluids. The space between the two walls can often be monitored for leaks, offering an immediate alert system that significantly enhances operational safety.
The precision and reliability of these heat exchangers make them ideal for the chemical and pharmaceutical industries. Here, the integrity of the fluid transfer mechanism is non-negotiable, as any compromise could lead to contamination or hazardous reactions. By eliminating the risk of fluid intermixing, double wall tube heat exchangers maintain the purity essential in these sectors, ensuring that each batch remains consistent with the highest quality standards.
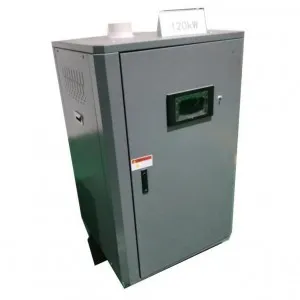
Beyond safety,
these heat exchangers are unparalleled in thermal efficiency. The inner tube facilitates the primary heat transfer, while the gap serves as an insulating buffer, minimizing heat loss and thus driving energy efficiency. Industries focusing on sustainability and cost reduction have found immense value in integrating double wall tube systems, as their ability to retain heat translates directly to energy savings and reduced operational costs.
In terms of craftsmanship and material selection, these exchangers are typically constructed from stainless steel or other durable alloys, which accommodate a wide temperature range and resist corrosion. This sustainability ensures longevity, reducing the frequency of replacements and maintenance, and thereby reducing overall lifecycle costs.
double wall tube heat exchanger
An emerging trend is the customization of double wall tube heat exchangers to meet specific industrial needs. Manufacturers now offer bespoke designs, with tube diameters, lengths, and materials tailored to optimize for specific thermal conduction requirements and installation parameters. This adaptability not only enhances performance but also broadens their applicability across non-standard operational environments.
Moreover, installation and maintenance have been simplified through advances in modular design. Companies can now invest in systems that are easily expandable or reconfigurable to match future growth or evolving process needs. The ability to service and upgrade components without extensive downtime or complete system overhaul provides companies with ongoing flexibility and reliability.
Thus, businesses looking to bolster their heat transfer solutions without compromising on safety or efficiency are increasingly turning to double wall tube heat exchangers. They offer a robust solution that aligns with high safety standards, energy efficiency goals, and environmental compliance.
With a strong reputation built on safety and efficiency, these heat exchangers are trusted by industries worldwide to support their most critical operations. Whether in pharmaceuticals, food and beverage, petrochemicals, or power generation, double wall tube heat exchangers represent a prudent investment in quality, reliability, and peace of mind, ensuring seamless operations while safeguarding critical resources.