A shell and tube heat exchanger stands as a quintessential tool in thermal management systems, particularly when discussing cooling water applications. This piece of equipment, cherished for its reliability and efficiency, plays a pivotal role in various industrial processes by facilitating heat exchange between two fluids—typically one flowing through the tubes and the other around the shell. Herein lies an exploration of the intricacies of shell and tube heat exchangers, their operational excellence, and real-world application insights.
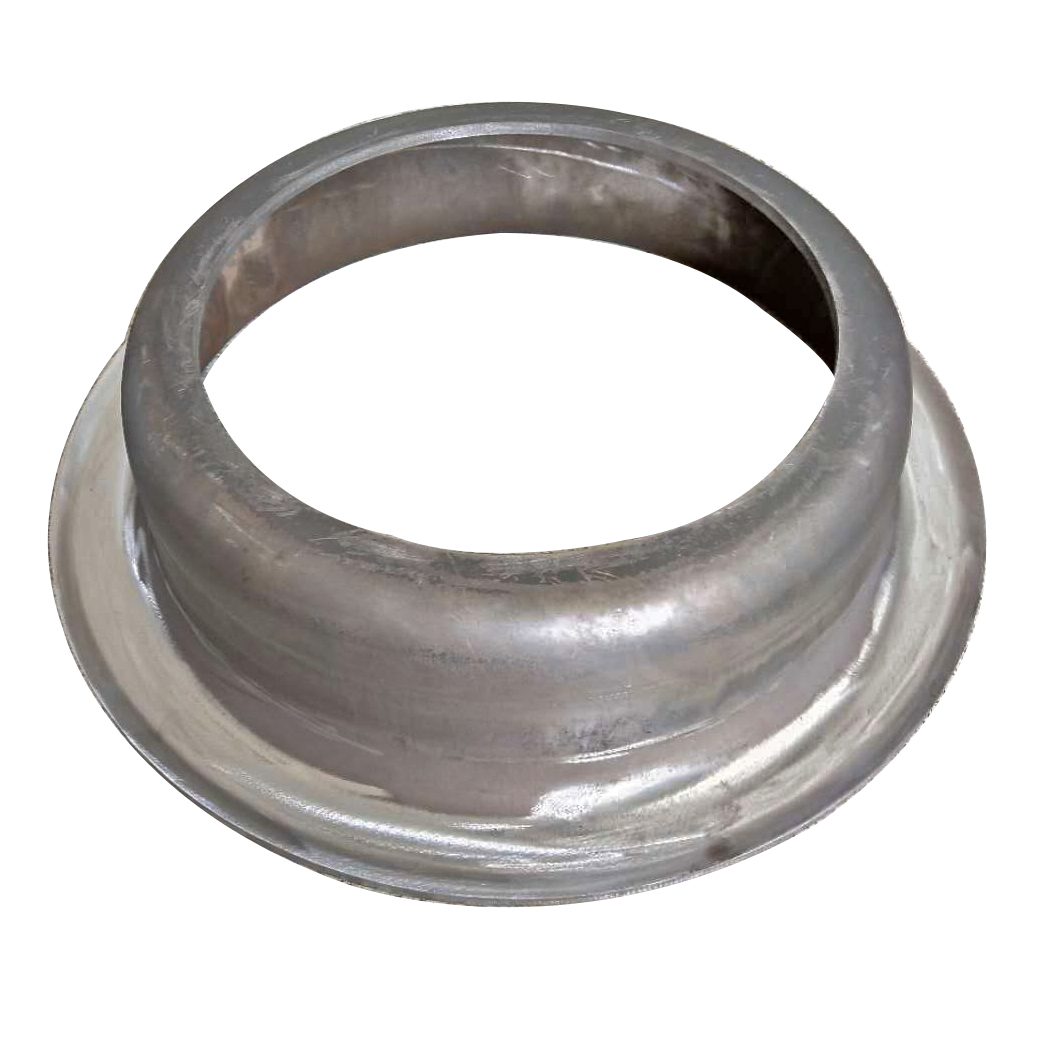
The fundamental design of a shell and tube heat exchanger comprises a series of tubes, packed within a cylindrical shell. One set of fluids is directed through the tubes, while the second fluid passes over them within the shell, enabling the heat transfer process. The elegance of this design is in its ability to handle high pressures and temperatures, making it ideal for industries like power generation, petrochemical, food processing, and HVAC.
An exemplary case in thermal performance is observed in facilities utilizing cooling water systems. Take, for instance, a petrochemical plant aiming to cool down processed hydrocarbons. Here, the cooling water circulates through the shell, absorbing heat from the hydrocarbon fluids circulating in the tube side. The large surface area of the tubes augments heat transfer rates, thereby optimally reducing the temperature of outgoing substances and ensuring operational stability and safety.
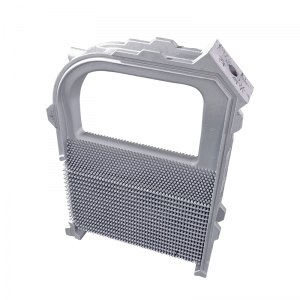
A major perk of shell and tube exchangers is their versatility. They can be customized in several ways—from the number of passes on the tube and shell sides to the choice of materials. Stainless steel is commonly preferred, providing corrosion resistance, essential for longevity and functional integrity especially when dealing with seawater cooling. This adaptability extends to maintenance as well; the modular design allows for the replacement of individual tubes or bundles without overhauling the entire unit.
From an engineering perspective, its prominence in the cooling sector is underscored by its efficiency in handling large volumes and flows. Engineers often emphasize the critical nature of selecting the right configuration based on specific process conditions and fluid properties. An underappreciated aspect of maximizing efficiency is through proper maintenance regimes, which include routine inspections and cleaning to prevent fouling and scaling—common adversaries in cooling water systems.
shell and tube heat exchanger cooling water
The necessity of heat exchangers finds verification from real-world examples. In a food processing facility, the shell and tube heat exchanger is employed to cool pasteurized milk quickly, maintaining not only product quality but also achieving regulatory compliance for storage temperatures. The authority of these devices in such sensitive applications speaks volumes about their dependable operation and compliance with stringent hygiene standards.
In terms of advancements, modern iterations of shell and tube heat exchangers incorporate enhanced fin designs and noise reduction technologies, aimed at meeting the demands of quieter, more energy-efficient operations. These innovations underscore the continued relevance and adaptability of traditional systems amidst advancing technology landscapes.
Trust in the effectiveness of this equipment largely stems from empirical evidence. Data suggest shell and tube heat exchangers offer superior return on investment due to their durability and decreased operational costs over time, compared to other types. Such insights are often shared among industry experts, fortifying their authoritative stance in enterprises seeking reliable thermal management solutions.
As operations around the world scale up, the significance of heat exchangers, particularly in cooling applications, becomes increasingly critical. Trusted for delivering consistent performance, these devices are crucial in processes where precision temperature control is paramount. The synthesis of expert opinions, complemented by user experiences, consistently enforces a narrative that shell and tube heat exchangers remain unrivaled in their class—a testimony to their engineered precision and real-world reliability.
In condensing this discourse on shell and tube heat exchangers, it is evident that their role in energy systems, cooling applications, and industrial heating processes is indispensable. Trust is built upon an uninterrupted history of reliability and efficiency, reinforcing the authority these systems command in global industrial applications.