Heat exchangers are crucial components across various industries, serving as the backbone for thermal systems by transferring heat between fluids without mixing them. For those delving into the intricate world of engineering, the design and drawing of a heat exchanger is not just a task but an essential skill that calls for significant expertise. This article unravels the subtleties of drawing heat exchangers, offering insights grounded in real-world experiences, enhanced by professional expertise, and underscored by authoritative and trustworthy information.
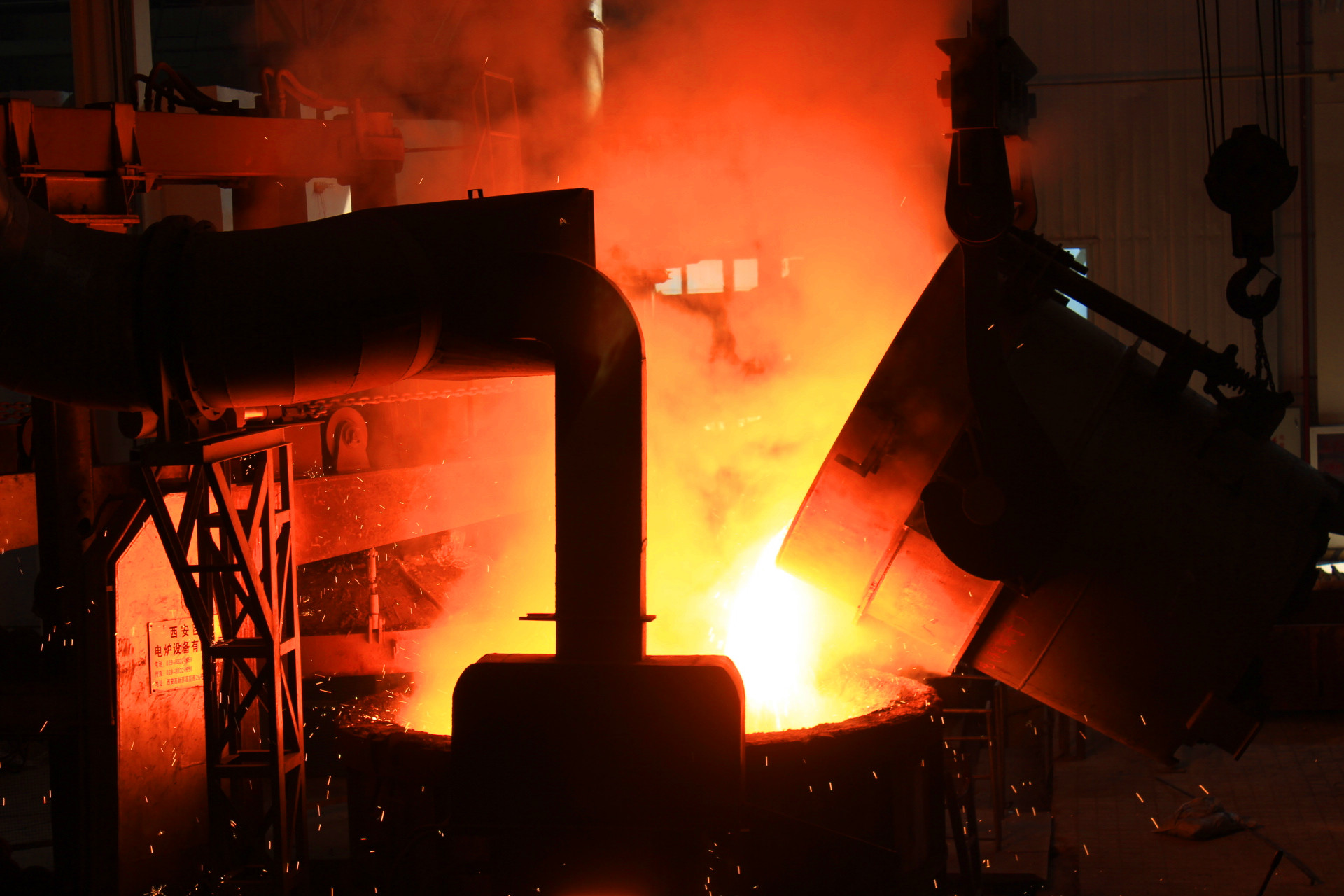
Understanding the blueprint of a heat exchanger begins with recognizing its purpose and the conditions it will function under. From HVAC systems to chemical processing plants, the applications dictate the type of heat exchanger—be it shell-and-tube, plate, or air-cooled designs. Each type offers distinct advantages; for example, shell-and-tube heat exchangers are often preferred in industries where high-pressure and temperature conditions are prevalent, due to their robust design and ease of maintenance.
To draw a heat exchanger effectively, one must first gather detailed parameters. These include information on the fluid types, flow rates, temperatures, and allowable pressure drops. Once these parameters are established, the next step is to select suitable materials. This step is pivotal as the material must withstand the operational temperatures and pressures while resisting corrosion. Stainless steel, copper alloys, and titanium are commonly employed due to their beneficial thermal properties and durability.
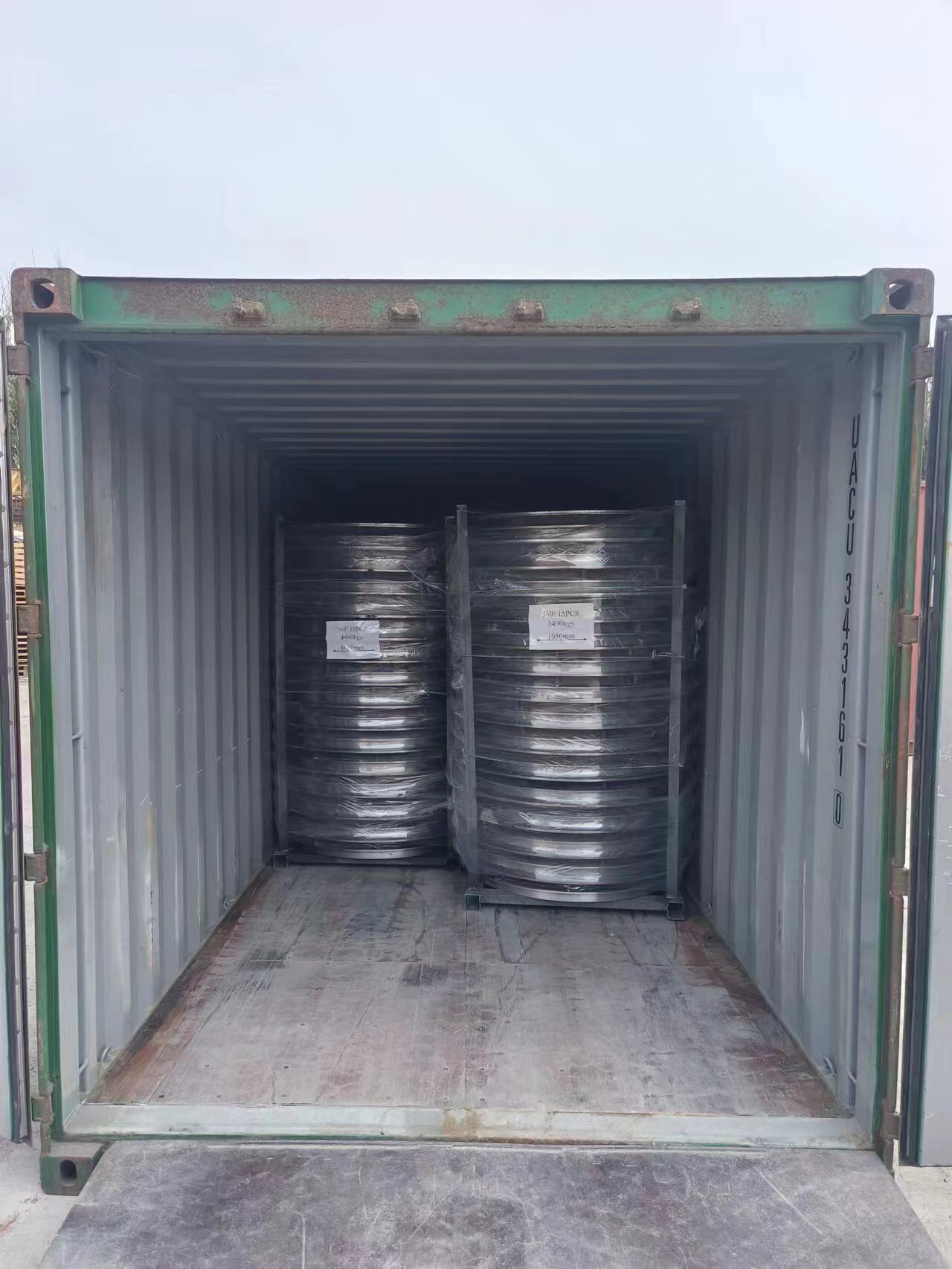
The drawing process itself commences with a comprehensive schematic that delineates the spatial arrangement of components. Expertise in computer-aided design (CAD) software can significantly enhance precision and efficiency at this stage. The schematic must articulate the relationship between the inlet and outlet headers, the arrangement of tubes or plates, and the positioning of baffles if applicable. This stage is not merely about dimensional accuracy but also ensuring that the design adheres to the industry standards like ASME, TEMA, or API.
Emphasis must be placed on the thermodynamic calculations that underpin the design. This involves determining the heat transfer coefficient, thermal load, and sizing of the exchanger’s surface area to ensure optimal performance. Professional evaluative techniques include the Log Mean Temperature Difference (LMTD) method and the Effectiveness-NTU, both requiring a deep understanding of thermodynamics and fluid dynamics.
drawing heat exchanger
In executing these tasks, collaboration with interdisciplinary teams often enriches the design process. Insights from mechanical engineers, materials scientists, and process engineers can refine aspects like material selection and layout, while technicians and draftsmen contribute by ensuring the schematics are not only functional but practical to manufacture and maintain.
Real-world expertise also emphasizes the importance of simulation and validation. Computational Fluid Dynamics (CFD) simulations are invaluable for testing how the heat exchanger will perform under expected conditions, allowing for adjustments before the manufacturing stage. Furthermore, peer reviews and verification by third-party professionals bolster the design’s trustworthiness, validating calculations and ensuring compliance with safety standards.
As fabrication begins, the drawing transforms from paper to tangible engineering marvels. Manufacturing must be meticulously monitored to adhere to the precise specifications laid out in the designs. Rigorous testing, including pressure tests and thermal performance evaluations, must be conducted to ensure reliability and efficiency.
The final element of the drawing process includes thorough documentation of the entire design and build procedure. This not only serves as a guide for operation and maintenance but also as a critical resource for future improvements and troubleshooting. Maintaining detailed records reflects the professionalism and accountability that underscores a successful engineering project.
In summary, drawing a heat exchanger is a process that demands a calculated blend of technical knowledge, practical skills, and strategic collaboration. It is an embodiment of engineering expertise and authority, harmonizing theoretical principles with practical applications. From gathering initial parameters to post-fabrication testing, each step is crucial to creating a device that stands the test of time and the rigor of industrial demands. Such thoroughness guarantees not only the creation of a robust and efficient heat exchanger but also strengthens trust and authority in the realms of engineering excellence.