When delving into the realm of heat exchanger dimensions, it's crucial to understand the pivotal factors that influence their design and functionality. Heat exchangers play an integral role in numerous industries, ensuring efficient thermal energy transfer between fluids. The intricacies of choosing the right dimensions for a heat exchanger are not just about fitting into a design; they are about optimizing performance, cost-effectiveness, and longevity. In this detailed exploration, we will uncover the key considerations and expert recommendations on this essential topic.
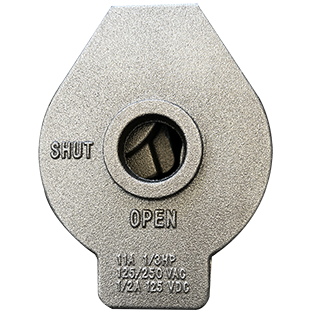
Firstly,
the application of the heat exchanger dictates the dimensions to a great extent. For example, industries such as oil and gas, HVAC, and chemical processing each have unique requirements based on the type of fluids, temperatures, and pressures involved. A small-scale HVAC system might benefit from compact, high-efficiency plate heat exchangers, with dimensions optimized for limited spaces, while a refinery would require large shell and tube configurations capable of handling enormous volumes and harsh conditions.
Moreover, the thermal load or the amount of heat that needs to be transferred plays an undeniable role in determining the dimensions. A higher thermal load requires a larger surface area for efficient heat exchange, directly impacting the size of the unit. An expert approach involves calculating the Log Mean Temperature Difference (LMTD) and the Overall Heat Transfer Coefficient, which together pinpoint the precise surface area needed for optimal exchange efficiency.
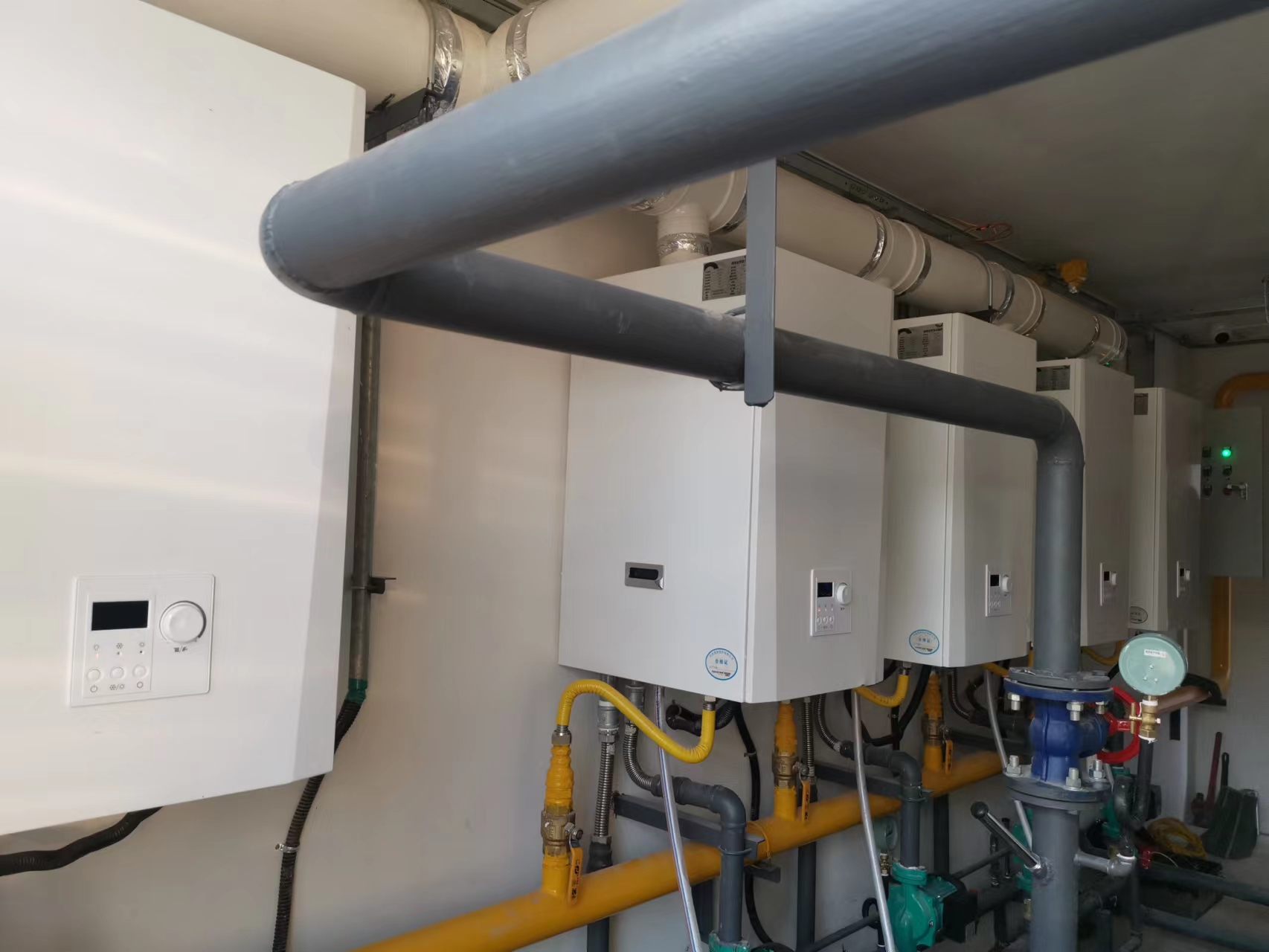
Another critical aspect is the type and properties of the fluids involved. The viscosity, corrosiveness, and fouling tendencies of fluids influence the selection of materials and the design intricacies of the heat exchanger. For instance, highly viscous fluids demand channels or tubes with larger diameters to ensure smooth flow and minimize pressure drops. Similarly, corrosive fluids might require specific materials like stainless steel or titanium, influencing not just durability but also cost.
Installation space constraints are practical considerations that often dictate dimensions. Industrial facilities might have limited space, necessitating a vertically stacked or a tightly-packed design without compromising efficiency. Computational Fluid Dynamics (CFD) has emerged as a powerful tool in customizing designs that perfectly fit the available space while maintaining excellent thermal performance.
Safety standards and regulations also govern the dimensions and design choices of heat exchangers. For instance, the American Society of Mechanical Engineers (ASME) codes outline stringent requirements for system integrity under various pressures and temperatures, directly impacting material thickness and component sizes to ensure safety and compliance.
heat exchanger dimensions
Furthermore, maintenance ease and accessibility are vital. A design that facilitates easy cleaning and maintenance can save significant operational costs. For example, design features such as removable tube bundles in shell and tube heat exchangers allow for straightforward inspection and cleaning, important in industries where fluid impurities can lead to fouling and reduce efficiency.
Incorporating energy-saving designs can help reduce the environmental impact and operational costs, a crucial consideration given today’s emphasis on sustainability. Optimal dimensioning that reduces unnecessary heat loss and energy consumption offers both economic and ecological benefits. The use of compact microchannel heat exchangers is one innovative solution, where enhanced heat transfer surfaces maximize efficiency despite their smaller physical footprint.
The choice between standard and custom dimensions is often a balance between cost and performance. Standard units, being mass-produced, offer cost benefits, whereas custom units, although potentially more expensive, can be tailored for specific needs, maximizing thermal efficiency and operational effectiveness.
Ultimately, achieving the perfect synergy between these diverse factors requires a nuanced approach blending experience, expertise, and advanced engineering tools. Trustworthy consulting from industry experts is indispensable, as they bring in-depth knowledge and experience to the table, ensuring that the chosen dimensions fulfill both current requirements and future scalability.
In conclusion, the dimensions of a heat exchanger are a delicate interplay of application requirements, thermal dynamics, fluid properties, space limitations, safety regulations, and maintenance considerations, all converging to achieve optimal performance. As technology advances, the realm of heat exchanger design continuously evolves, promising ever more efficient, durable, and cost-effective solutions, tailored to meet the specific needs of various industrial applications.