In the intricate world of manufacturing, casting parts emerge as unsung heroes, silently powering industries from automotive to aerospace. Understanding the anatomy and intricacies of casting parts not only enhances operational efficiency but also ensures the delivery of high-quality products.
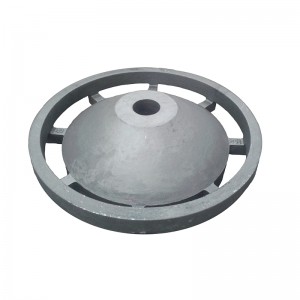
Casting, a venerable manufacturing process, involves pouring liquid material into a mold to form a desired shape once solidified. This technique, traced back thousands of years, has evolved to meet the exacting standards of modern-day production. The diversity in casting processes—ranging from sand casting and die casting to investment casting—caters to varied industrial needs, each offering unique benefits in terms of cost, precision, and material properties.
Focusing on experience is paramount. Successful casting is a result of cumulative insights gathered over decades. Experienced foundries leverage this knowledge to navigate complex projects, offering solutions that are not apparent to novices. One striking example of experience-driven casting innovation is in the automotive sector, where lightweight yet robust components are increasingly demanded. Through trial and meticulous refinement, seasoned experts have perfected methods to produce casting parts that significantly reduce vehicle weight without compromising strength or safety.
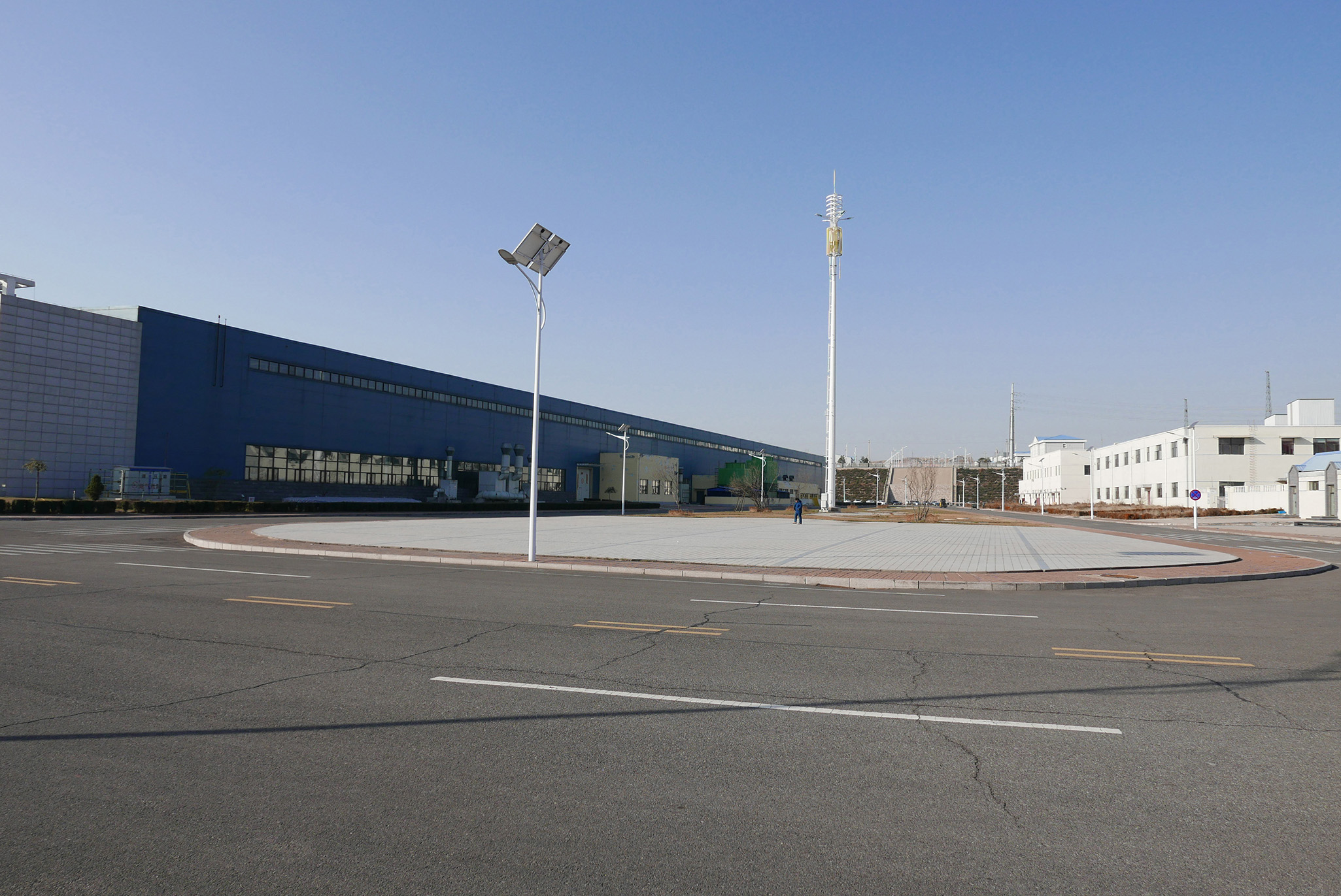
Expertise in materials and methods is essential. A nuanced understanding of metallurgy and material science guides experts in selecting the right alloy to match specific application requirements. For instance, when corrosion resistance and lightweight construction are critical, aluminum alloys might be favored, while cast iron remains a staple where high strength and wear resistance are paramount. Expertise also extends to mastering techniques like lost-wax casting, which allows for intricate designs with superior surface finishes.
Authoritativeness in casting is often established through continuous certification and adherence to industry standards. Leading manufacturers invest in cutting-edge technologies and rigorous quality control systems to maintain their authoritative status. Techniques such as X-ray inspection and 3D scanning ensure that casting parts meet stringent specifications and performance criteria. These firms also contribute to the field by spearheading innovations and best practices, serving as benchmarks for others in the industry.
casting part
Trustworthiness is the bedrock of successful supplier-client relationships in casting. Reliable manufacturers understand that delivering defect-free casting parts consistently is non-negotiable. Trust is built through transparent operations, where clients are kept informed throughout the manufacturing process. Moreover, environmentally-conscious manufacturers strive to reduce the carbon footprint of casting processes, enhancing their credibility in an era where sustainability is not just preferred but expected.
For businesses looking to source casting parts, choosing the right partner can spell the difference between project success and costly overruns. Critical considerations include evaluating the manufacturer's technical proficiency, track record, and the technological infrastructure they have in place. It's also prudent to consider the manufacturer's ability to scale operations to align with your growth trajectory.
Investing in the right collaboration opens doors to bespoke solutions tailored to meet specific industry challenges. Custom casting parts have become pivotal in industries such as wind energy, where precision-engineered components are crucial for efficient power generation. Such partnerships not only yield immediate product benefits but also contribute to longer-term technological advancements.
In sum, casting parts, though often overlooked, are fundamental to modern manufacturing. Their role is expanding beyond mere functional applications to becoming central components that support innovation and sustainability. Through expertise, experience, authoritativeness, and trustworthiness, the centrifugal force of the casting industry continues to push boundaries, ensuring that the products of tomorrow are not only feasible but flourish under new demands and paradigms. This is the inherent power of casting parts—shaping a future driven by precision and reliability.