In the intricate operations of oil refineries, heat exchangers play a pivotal role by optimizing energy efficiency and ensuring seamless functioning of processes. They are integral to keeping operations green and cost-effective, and leveraging their full potential requires a blend of experience, expertise, authoritativeness, and trustworthiness.
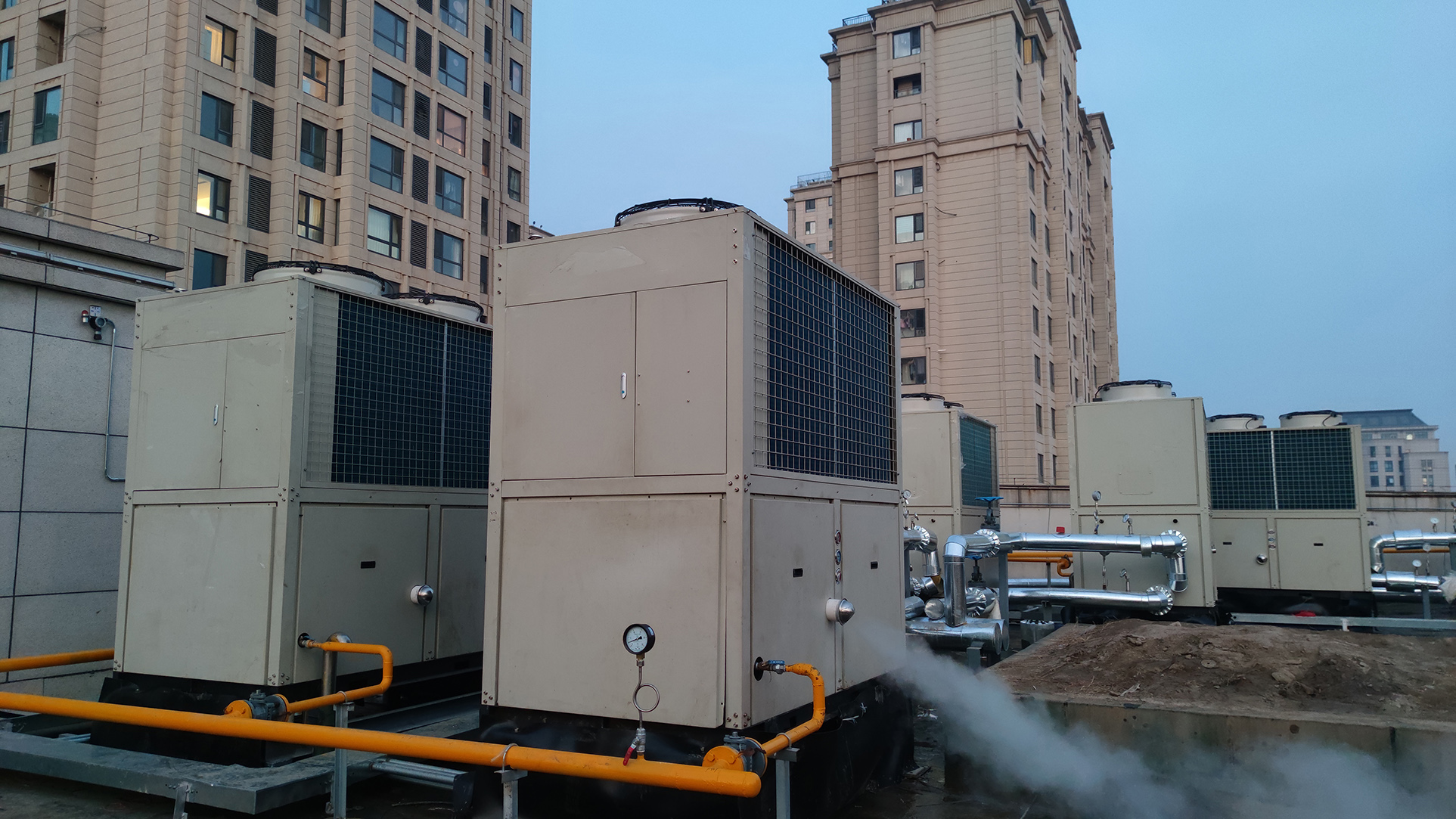
The efficacy of a heat exchanger is directly proportional to the operational success of a refinery. Heat exchangers are deployed to conserve energy by recovering heat from waste streams and converting it to useful energy, thereby reducing the overall energy demand. Their application is vital in the context of pre-heating crude oil, achieving efficient temperature control in distillation columns, and managing product cooling, among other processes.
Advanced heat exchanger technology offers an edge by minimizing energy consumption and maximizing thermal performance. Shell-and-tube, plate, and air-cooled heat exchangers are common types, each offering distinct advantages. Shell-and-tube exchangers, for instance, are acclaimed for their durability and ability to withstand high pressures. Plate heat exchangers, on the other hand, provide a compact solution with high heat transfer efficiency, making them an ideal choice for space-constrained environments. Air-cooled exchangers are predominantly used when water cooling isn’t feasible, offering a sustainable alternative with reduced impact on water resources.
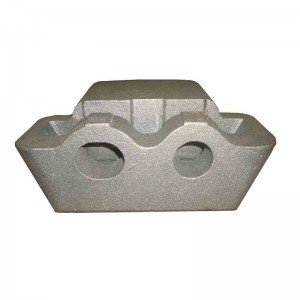
Real-world success in employing these technologies underscores the importance of understanding specific process needs. Expert insights garnered from on-the-ground experience reveal that selecting the correct type and material of heat exchanger is critical. Materials should be chosen based on resistance to corrosion and other operational stresses, as exemplified by the use of stainless steel in high-corrosion settings.
refinery heat exchangers
An authoritative understanding of thermal dynamics can significantly enhance the functional lifespan of heat exchangers, thereby ensuring reliability and efficiency. Subject matter experts recommend regular maintenance and inspections to preclude fouling—a common problem where deposits reduce heat transfer efficiency. Implementing cleaning schedules and real-time monitoring systems augments operational reliability and prolongs equipment life.
Trust is fostered through adherence to stringent industry standards and certifications, reflecting the commitment to safety and performance. Refineries pursuing high standards of operation must align with ASME codes and API standards to ensure their exchangers meet rigorous quality requirements, thus fostering an environment where safety and efficiency coalesce.
Emerging innovations in heat exchanger designs are worth noting. The integration of nanotechnology promises enhancements in heat transfer fluids, potentially revolutionizing heat exchangers by significantly boosting efficiency. Meanwhile, the introduction of modular heat exchangers facilitates quick replacements, minimizing downtime and enhancing productivity.
In conclusion, the strategic application of heat exchangers in refineries isn't merely an operational necessity but a pivotal strategy for energy conservation and efficiency. By leveraging experience, expertise, authoritativeness, and trustworthiness, refineries can optimize these systems for improved performance and sustainability. The path forward involves not only embracing current technologies but also remaining at the forefront of innovations that complement and enhance traditional systems, ensuring that refineries not only meet but exceed industry benchmarks for performance and environmental stewardship.