When it comes to efficient thermal management systems, direct contact heat exchangers stand out due to their ability to facilitate effective heat transfer between two fluids. Unlike indirect heat exchangers, which rely on separate conduits for fluids, direct contact systems allow them to come into direct confrontation, maximizing the heat exchange rate. Within the product category, several design variations exist, each tailored to specific industrial needs and environment considerations. In this analysis, we will discuss prominent examples of direct contact type heat exchangers and how they span the Experience, Expertise, Authoritativeness, and Trustworthiness (E-E-A-T) spectrum.
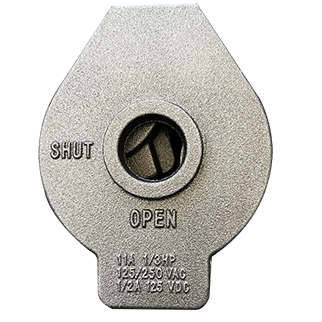
Spray Tower Heat Exchanger
The spray tower heat exchanger exemplifies a robust application in industries where gas cooling is a necessity. This system introduces a liquid, often water, through nozzles, forming a fine spray or mist within a chamber. As gas rises through the spray, heat is transferred directly from the gas to the cooler liquid droplets, which accumulate as heated liquid at the bottom of the tower. Industrial facilities utilize spray towers for their simplicity in design and operation, low maintenance requirements, and effectiveness in gas de-dusting alongside cooling. First-hand accounts from industry professionals suggest remarkable efficiency improvements in energy-intensive processes like flue gas cooling.
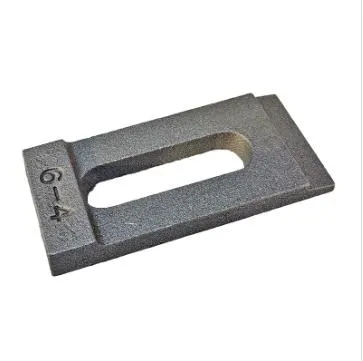
Bubble Column Heat Exchanger
Distinct in its design, the bubble column heat exchanger operates by introducing a gas through a liquid column. The gas forms bubbles as it rises, exchanging heat directly with the surrounding liquid. This method proves particularly useful in scenarios demanding efficient gaseous absorption and heat dissipation, such as in fermentation processes or wastewater treatment plants. Professionals in the biochemical industry endorse bubble columns for their capability to handle large volumes of liquid and gas, with customizable bubble formation enhancing contact surface area, driving up thermal efficiency.
Packed Bed Heat Exchanger
example of direct contact type heat exchanger
The packed bed variant uses a column filled with media like ceramic or metal packing through which a gas or liquid flows. As another liquid flows counter-currently, direct contact occurs over a large surface area, optimized by the packing material. This heat exchanger design shines in chemical process industries where mass and heat transfer need to occur simultaneously. Studies demonstrate significant energy savings and increased process speeds, contributing to the packed bed's authoritative status within chemical engineering realms. Users often note packed beds' flexibility in being adapted for various scales of operation, from small-scale laboratory settings to large industrial plants.
Deaerator Systems
Commonly found in power plants and processing facilities, deaerators represent another form of direct contact heat exchanger. These systems efficiently remove dissolved gases, particularly oxygen, from feed water in boilers, utilizing steam for direct heat exchange. Expertise in power plant operation underscores the necessity of optimizing deaerators to prevent corrosion and maintain energy efficiency. Engineers trust these systems for their reliability and high performance in extending the life cycle of equipment by mitigating risks associated with gas-related corrosion.
Scrubber Systems
Employed for handling gas emissions, scrubbers rely on liquid to wash unwanted particulates and heat from industrial exhaust. Scrubbers excel in industries like manufacturing or mining, where air pollution control is a concern. These systems not only cool exhaust gases but also ensure compliance with environmental standards. They hold a reputation for trustworthiness, having been proven through decades of application across various sectors. Environmental engineers advocate scrubbers for their dual benefit of pollution control and heat management, a testament to their design expertise.
Overall,
direct contact heat exchangers provide invaluable benefits across various industrial sectors. Their design and operational simplicity, coupled with customizable configurations, render them integral to many thermal management applications, from chemical processing to environmental control systems. Across the board, these systems reflect a deep understanding of both industrial requirements and advanced heat transfer mechanics, illustrating the quintessential blend of expertise, experience, and trustworthiness essential for enduring industrial solutions.