A double shell and tube heat exchanger exemplifies a crucial innovation in thermal management systems, tailored for efficiency and versatility in transferring heat between fluids. In modern industrial applications, where maximizing energy efficiency and maintaining compact and reliable systems is paramount, the selection of an appropriate heat exchanger is critical. This article provides an in-depth exploration of double shell and tube heat exchangers, revealing their unique features, operational advantages, and the best practices for their application in various industries.
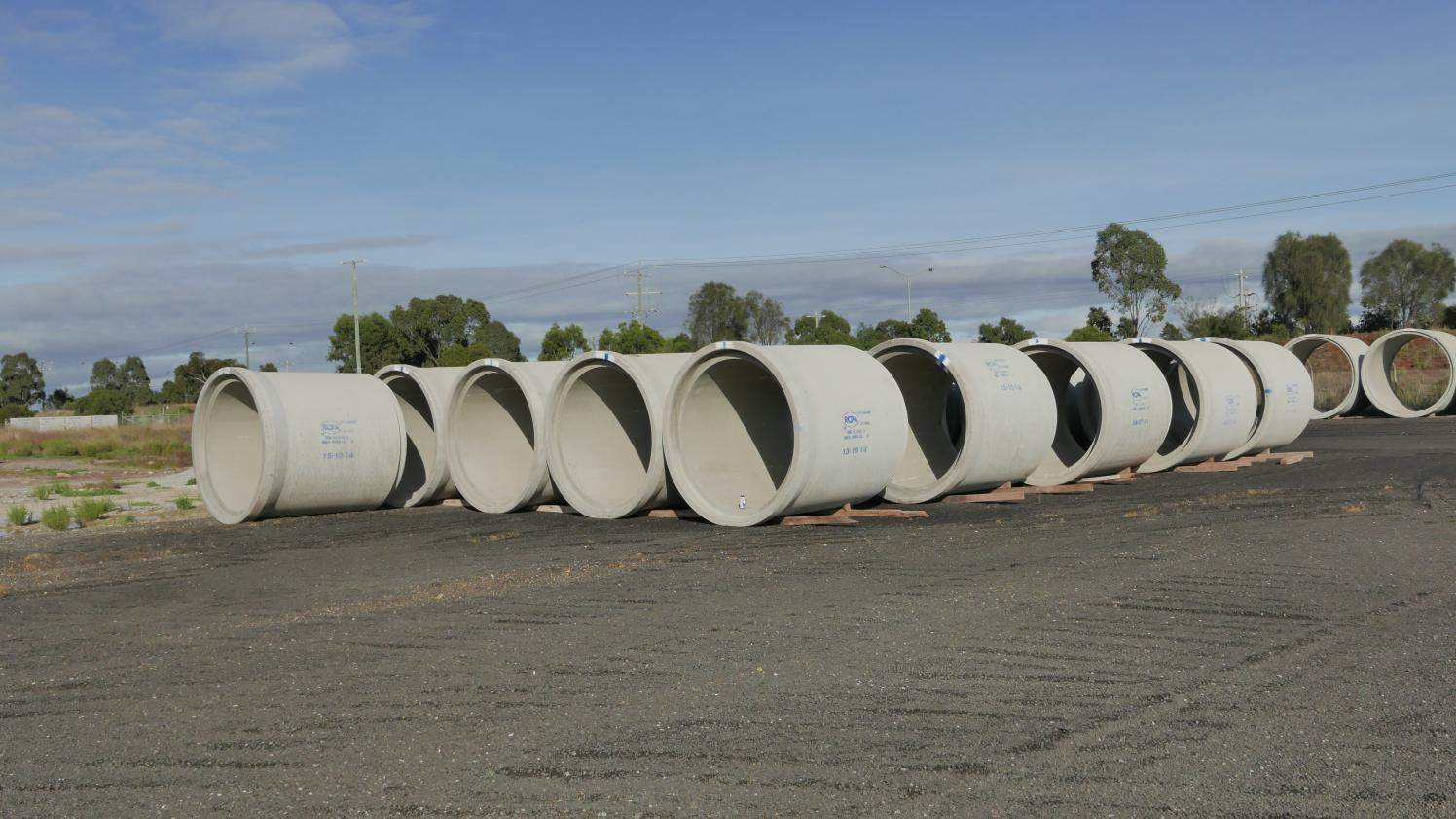
Double shell and tube heat exchangers integrate two distinct features a secondary shell layer and a conventional tube bundle. The secondary shell surrounds the primary shell with an additional layer, facilitating an enhanced level of heat transfer. As the hot fluid flows through the tubes, it exchanges heat with colder fluid in the shell space, making this system highly efficient. The design inherently supports a counter-current flow arrangement, enabling a greater difference in temperature between the fluids, thus optimizing the heat exchange process.
The primary advantage of a double shell and tube heat exchanger is its compactness compared to traditional single shell units, making it ideal for space-constrained environments. This feature is particularly beneficial in sectors like chemical processing, pharmaceuticals, and petrochemicals, where space efficiency does not compromise performance quality. The design's effectiveness in handling high temperature and pressure differentials also stands out as a significant benefit, reducing equipment wear and potentially lowering maintenance costs.
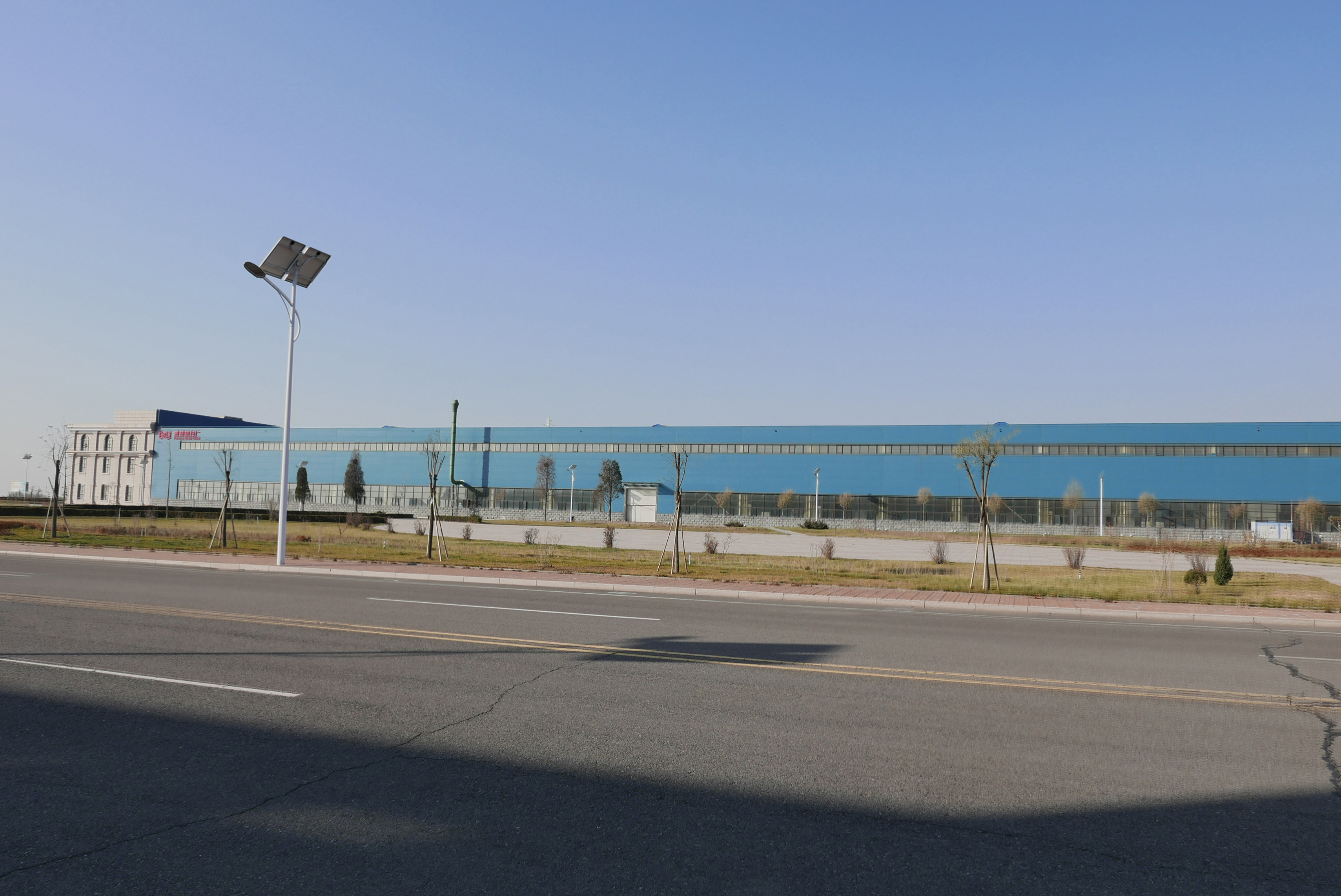
Expertise in designing and implementing double shell and tube heat exchangers is vital. Their deployment requires a deep understanding of fluid dynamics and thermal transfer principles to optimize their size and materials for specific applications. For industries that handle aggressive chemicals or high-pressure environments, material selection is critical to ensure the integrity and longevity of the heat exchanger. Commonly used materials include stainless steel, titanium, and nickel alloys, each selected based on the specific requirements of resisting corrosion and maintaining structural integrity at extreme temperatures.
Trustworthiness in the application and operation of these exchangers stems from meticulous engineering and manufacturing processes. Global standards, such as the ASME (American Society of Mechanical Engineers) codes, guide the production of these sophisticated devices, ensuring they meet stringent quality and safety guidelines. Factoring in these standards during the selection process guarantees that the equipment will perform reliably under stated conditions and offers peace of mind to operators and investors alike.
double shell and tube heat exchanger
In terms of energy efficiency, double shell and tube heat exchangers are designed to offer minimal pressure drop while maximizing heat transfer efficiency. This attribute can significantly cut energy costs, especially in large-scale operations. Leveraging computational fluid dynamics (CFD) during the design phase allows for precise modeling of fluid and heat flow, optimizing the exchanger's configuration before it is even constructed. This virtual testing phase ensures the finished product will deliver on the anticipated performance metrics.
Applying this technology in a reliability-centered maintenance framework allows businesses to predict potential failures before they occur. Regular monitoring through advanced sensor technology and using performance data analytics, operators can extend the life of their heat exchangers and maintain efficiency. Furthermore, these systems can be integrated into overall industrial Internet of Things (IIoT) architectures, enabling real-time data collection and analysis to drive smart decision-making and predictive maintenance strategies.
Successfully implementing a double shell and tube heat exchanger involves more than just selecting an appropriate model. Professionals must consider the exchanger's integration into the larger system, assessing compatibility with other components and the intended fluid dynamics. Expert consultation is often required to tailor the system to specific industrial needs, ensuring optimal return on investment.
On a conclusive note, double shell and tube heat exchangers embody a sophisticated balance of design, material excellence, and precision engineering. Acknowledging their diverse applications and reinforced by a track record of reliability, they are increasingly pivotal in industries aiming to enhance operational efficiency and sustainability. This focus on innovation and excellence not only amplifies energy savings but also firmly positions double shell and tube heat exchangers as invaluable assets in the contemporary industrial landscape.