Selecting the right fluid for a heat exchanger is a critical decision that impacts the performance, efficiency, and longevity of the heat exchange system. The process involves considering various factors such as thermal conductivity, specific heat capacity, viscosity, and chemical compatibility. A well-informed choice ensures optimal operational conditions and maximizes system effectiveness.
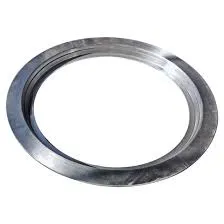
Understanding the specific requirements of your application is the first step in fluid selection. Each application comes with unique demands; whether it’s for HVAC systems, chemical processing, or power generation, the fluid must be tailored to suit these needs. Essential criteria include the operating temperature range, pressure levels, and the type of heat exchanger in use, whether it be shell-and-tube, plate, or air-cooled.
Thermal conductivity is paramount; selecting a fluid with high thermal conductivity facilitates efficient heat transfer, reducing energy consumption and enhancing performance. Water is a common choice due to its excellent thermal properties, but it’s important to note its limitations in terms of freezing and boiling points under extreme conditions. Alternative fluids, such as glycol-water mixtures, are often employed in scenarios where freezing is a concern.
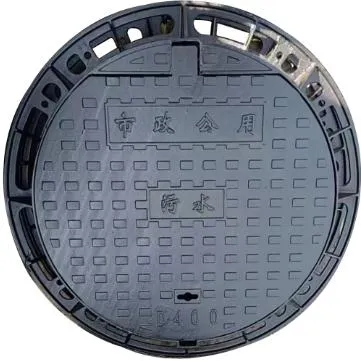
The viscosity of the fluid is another consideration, as it affects the pumping power required and the efficiency of the heat transfer. Fluids with low viscosity are typically preferred, as they flow more readily, reducing the frictional pressure drop across the system. However, a balance must be achieved as very low viscosity fluids may compromise the heat exchanger’s ability to transfer heat effectively.
Specific heat capacity should not be overlooked, as fluids with high specific heat can absorb more heat without a significant rise in temperature. This makes them particularly useful in systems where temperature control and stability are essential. Matching the fluid’s specific heat capacity to the system’s requirements ensures that the heat exchanger can meet the thermal demands without strain.
heat exchanger fluid selection
Chemical compatibility and material considerations are equally important. The selected fluid must be compatible with the materials used in the heat exchanger to avoid corrosion, scaling, or chemical degradation. For instance, if the system utilizes copper pipes, fluids containing ammonia must be avoided due to corrosion risk. Consulting material compatibility charts and corrosion data is a standard practice that guarantees long-term reliability and safety of the system.
Safety and environmental impact cannot be underestimated. Non-toxic, biodegradable fluids are increasingly preferred as industries commit to sustainable practices. Many heat exchangers now operate with natural refrigerants such as carbon dioxide (CO2) and hydrocarbons, which have a lower environmental impact compared to chlorofluorocarbons (CFCs) and hydrochlorofluorocarbons (HCFCs).
Finally,
economic considerations play a significant role in fluid selection. Initial costs, availability, maintenance requirements, and energy efficiency impacts must be weighed against the budget constraints of the project. While it might be tempting to choose a less expensive fluid solution, the long-term operational costs related to energy efficiency and maintenance should guide the decision-making process.
In conclusion, selecting the appropriate heat exchanger fluid requires a comprehensive evaluation of thermal performance, compatibility, safety, and economic factors. Engaging with manufacturers and industry experts to obtain data sheets and test results can offer valuable insights and support informed decision-making. This process not only enhances the system’s performance but also extends the operational life of the heat exchanger, providing a reliable and efficient solution to various industrial applications.