Die Casting Aluminum Parts A Comprehensive Guide
Die casting is a manufacturing process that involves pouring molten metal into a steel mold, where it solidifies under high pressure. This method is widely used to produce complex shapes and intricate designs in various industries. One of the most popular materials for die casting is aluminum due to its excellent properties such as low density, high strength-to-weight ratio, and good corrosion resistance. In this article, we will discuss the various aspects of die casting aluminum parts, including the process, materials, applications, and benefits.
The die casting process involves several steps, starting with the design of the mold. The mold is typically made of two halves, which are machined to precise tolerances to ensure a tight seal when closed. The mold is then assembled and preheated to the appropriate temperature, depending on the type of aluminum alloy being used.
Aluminum alloys suitable for die casting include those with low melting points, such as zinc, magnesium, and aluminum. These alloys are chosen based on their chemical composition, mechanical properties, and ability to flow into the mold cavities. Some common aluminum alloys used in die casting include A380, ADC12, and ZL101.
Die casting aluminum parts have a wide range of applications in various industries. They are commonly used in the automotive industry for producing engine blocks, transmission cases, and other components They are commonly used in the automotive industry for producing engine blocks, transmission cases, and other components
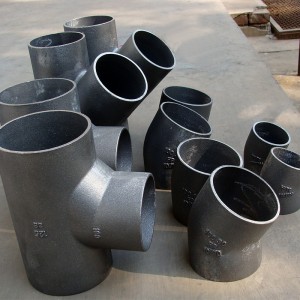
They are commonly used in the automotive industry for producing engine blocks, transmission cases, and other components They are commonly used in the automotive industry for producing engine blocks, transmission cases, and other components
die casting aluminum parts. Die cast aluminum is also used in the aerospace industry for manufacturing lightweight components such as fuel tanks and brackets. Other industries that benefit from die casting aluminum parts include electronics, construction, and consumer products.
One of the key advantages of die casting aluminum is its ability to produce parts with high dimensional accuracy and surface finish. The high pressure used during the casting process ensures that the metal fills the mold cavities uniformly, resulting in parts with minimal flash and porosity. This makes die cast aluminum parts well-suited for applications where precision and durability are critical.
Another advantage of die casting aluminum is its relatively low cost compared to other manufacturing processes such as forging or machining. This is because die casting requires fewer processing steps and can produce parts in large quantities with high productivity.
In conclusion, die casting aluminum parts offer numerous benefits, including high dimensional accuracy, excellent surface finish, and cost-effectiveness. With its versatility and broad range of applications, die casting aluminum continues to be a popular choice for manufacturers seeking to produce complex components with high quality and performance.