The Manufacturing Process of Cast Iron A Journey into Metallurgical Artistry
Cast iron, a versatile and durable material, has been a cornerstone in manufacturing for centuries due to its unique properties and wide range of applications. Its manufacturing process is a complex blend of science and art, requiring precision and expertise. This article delves into the intricate details of how cast iron is produced.
The journey of cast iron begins with raw materials. Mainly composed of iron, carbon, and silicon, cast iron also contains smaller amounts of manganese, sulfur, and phosphorus. These elements are sourced from iron ore, coke, and limestone. Coke, derived from coal, acts as a fuel and reduces iron oxide to iron during the production process. Limestone, on the other hand, serves as a flux, removing impurities like silica.
The first step in manufacturing cast iron is smelting. In a blast furnace, these raw materials are layered together with the coke at the bottom, followed by the iron ore and limestone. The furnace is then heated to extremely high temperatures, around 2,000°C, causing a chemical reaction known as reduction. Coke burns to produce carbon monoxide, which reacts with iron oxide, converting it into liquid iron.
During this process, impurities such as sulfur and phosphorus are removed by the limestone. The molten iron, now free of significant impurities, is tapped from the bottom of the furnace The molten iron, now free of significant impurities, is tapped from the bottom of the furnace
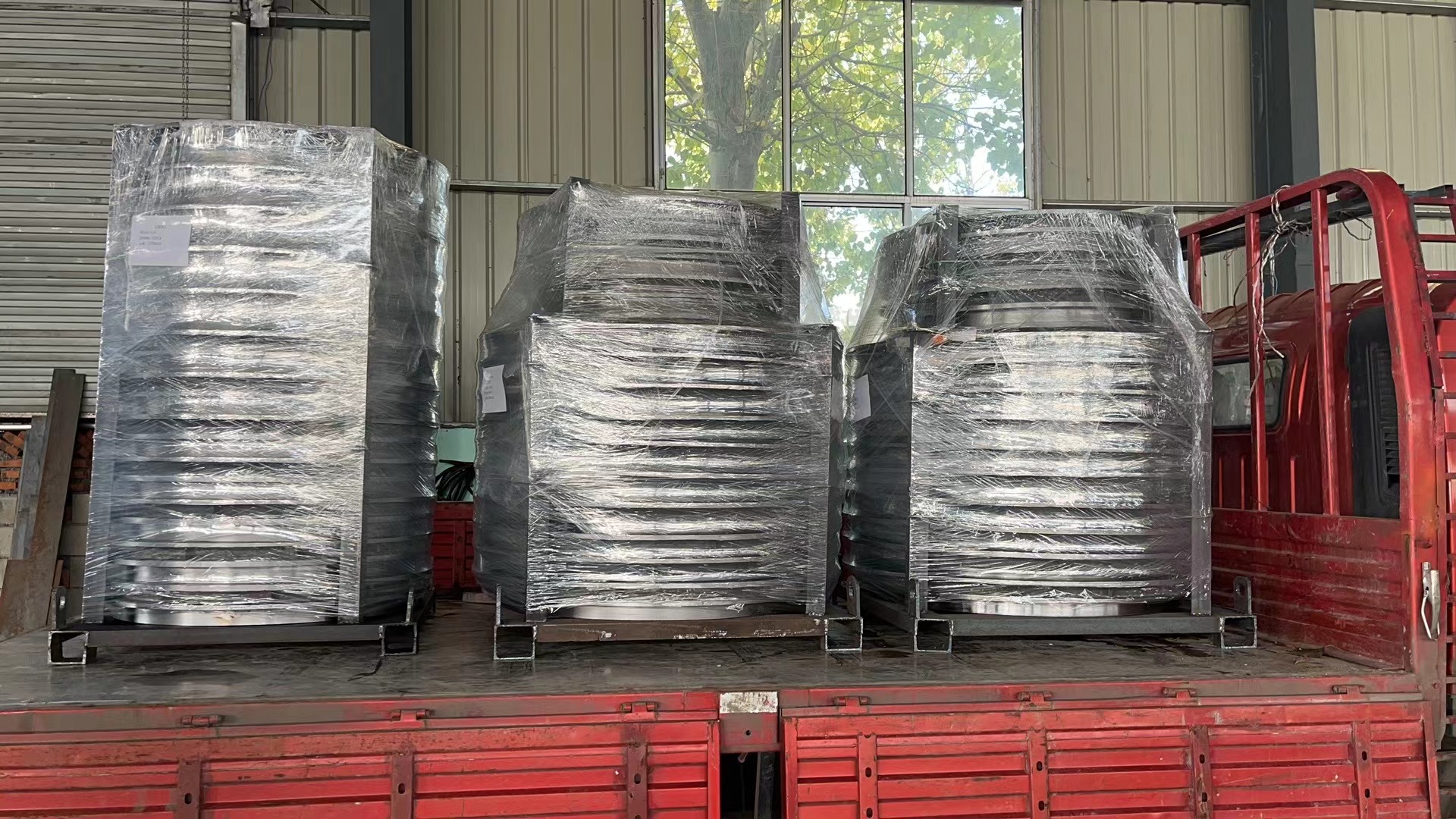
The molten iron, now free of significant impurities, is tapped from the bottom of the furnace The molten iron, now free of significant impurities, is tapped from the bottom of the furnace
manufacturing of cast iron. It is then transferred to a ladle, ready for casting.
The next phase is the casting process, where the liquid iron is poured into molds to form the desired shape. Molds can be made from sand or metal, with the former being more common due to its low cost and ease of use. Sand molds are typically made by compacting sand around a pattern that replicates the final product. Once the mold is filled with molten iron, it cools and solidifies, taking the shape of the mold.
After cooling, the cast iron is removed from the mold and undergoes various finishing processes. These may include machining, grinding, and heat treatment to refine the surface finish, improve mechanical properties, and relieve internal stresses. The final product can be a simple component or a complex, intricate part, depending on the application.
In conclusion, the manufacturing of cast iron is a meticulous and transformative process, from the extraction of raw materials to the final casting. Its unique properties, such as high strength, wear resistance, and good casting ability, make it a vital material in various industries, including automotive, construction, and machinery. Despite the advancements in technology, the fundamental principles of cast iron manufacturing remain rooted in the ancient art of metallurgy, a testament to human ingenuity and the enduring nature of this remarkable material.