The Art of Cast Silicon Aluminum Alloy Heat Exchanger Manufacturing
In the world of industrial manufacturing, the quest for materials that can withstand the rigors of high-temperature environments while maintaining efficiency is never-ending. One such material that has made significant strides in this pursuit is the cast silicon aluminum alloy. This innovative compound offers a unique blend of properties, making it an ideal choice for heat exchanger applications. In this article, we will delve into the intricate process involved in manufacturing cast silicon aluminum alloy heat exchangers and highlight the benefits they offer to various industries.
Manufacturing cast silicon aluminum alloy heat exchangers is a meticulous process that begins with selecting the right quality of raw materials. The alloy composition must be carefully controlled to ensure optimal thermal conductivity and mechanical strength. Once the alloy is prepared, it enters the casting stage, where advanced techniques such as die-casting or sand casting are employed to shape the alloy into precise heat exchanger components. These methods allow for intricate designs and tight tolerances, which are crucial for maximizing heat transfer efficiency.
Following the casting process, the components undergo a series of finishing steps, including machining, cleaning, and surface treatment. Machining ensures that each part fits seamlessly within the heat exchanger system, while cleaning removes any residual casting materials that could impede performance. Surface treatments, like anodizing or coating, may also be applied to enhance corrosion resistance and improve durability further Surface treatments, like anodizing or coating, may also be applied to enhance corrosion resistance and improve durability further
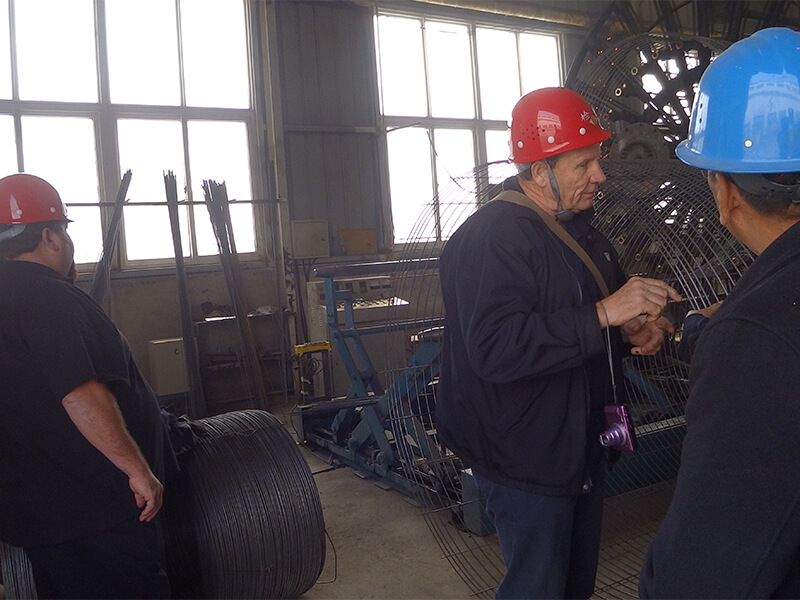
Surface treatments, like anodizing or coating, may also be applied to enhance corrosion resistance and improve durability further Surface treatments, like anodizing or coating, may also be applied to enhance corrosion resistance and improve durability further
cast silicon aluminum alloy heat exchanger manufacturer.
The advantages of using cast silicon aluminum alloy for heat exchangers are numerous. Its excellent thermal conductivity means that these devices can effectively manage large temperature differentials, making them suitable for harsh industrial settings. The alloy's natural resistance to corrosion and scaling allows heat exchangers to operate more efficiently over extended periods without maintenance. Additionally, the lightweight nature of silicon aluminum alloys results in easier handling during installation and potentially lower transportation costs.
Manufacturers specializing in cast silicon aluminum alloy heat exchangers stand at the forefront of innovation, continuously refining their processes to push the boundaries of what is possible. Their commitment to excellence ensures that these essential components meet the highest standards of performance and reliability across diverse sectors such as automotive, aerospace, and industrial cooling systems.
In conclusion, the manufacture of cast silicon aluminum alloy heat exchangers represents a pinnacle of engineering and material science. By leveraging the exceptional properties of this composite material, manufacturers provide solutions that not only endure under extreme conditions but also contribute to increased energy efficiency and reduced operational costs. As technology continues to evolve, so too will the processes and materials used in heat exchanger manufacturing, promising even greater advancements in industrial heating and cooling applications.