Exploring the Artisanal Process of Custom Cast Iron Pipe Casting
In the realm of infrastructure and design, custom cast iron pipe casting stands as a testament to the fusion of traditional craftsmanship with modern engineering needs. This intricate process, steeped in history, offers unparalleled durability, aesthetic appeal, and versatility, making it a preferred choice for applications ranging from water supply systems to ornamental architectural features.
The Essence of Custom Cast Iron
Custom cast iron pipe casting begins with a vision – a specific requirement or design that deviates from standard, off-the-shelf solutions. Unlike mass-produced pipes, each custom piece is meticulously crafted to meet exact specifications, whether it's a unique diameter, an uncommon length, or even intricate decorative patterns.
The Casting Process Unveiled
The journey from raw material to a finished custom cast iron pipe unfolds through several stages
1. **Design and Pattern Making**
It all starts with a detailed design, which is then translated into a physical pattern. This pattern, typically made from wood or metal, mirrors the internal and external shape of the desired pipe. Precision at this stage is paramount, as the pattern directly influences the final product's accuracy.
2. **Molding**
Using the pattern, a mold is created, usually composed of sand mixed with a bonding agent. The sand mold is split into two halves to facilitate the removal of the cast piece later. For complex designs, multiple-piece molds are employed, ensuring every detail is captured.
3. **Casting**
The next step involves pouring molten iron, heated to around 1450°C, into the prepared mold. The high temperature ensures the metal flows smoothly, filling every crevice before gradually cooling and solidifying. This phase requires careful temperature control and precise timing to avoid defects such as porosity or shrinkage.
4
4
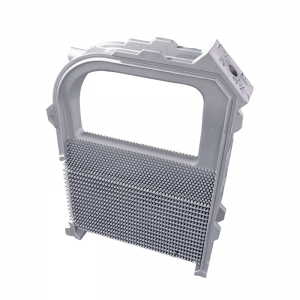
4
4
custom cast iron pipe casting. **Finishing and Inspection**
Once cooled, the cast pipe is extracted from the mold, revealing a rough version of the final product. It then undergoes a series of finishing processes, including grinding, machining, and sometimes coating, to achieve the desired surface finish and dimensional tolerances. Each piece is rigorously inspected to guarantee conformity to the client's specifications and industry standards.
The Charm of Customization
Custom cast iron pipes offer several advantages over standardized alternatives. Firstly, they provide tailor-made solutions for challenging installations, navigating through odd angles or limited spaces effortlessly. Secondly, their inherent strength and longevity make them ideal for projects demanding resilience against corrosion and high-pressure conditions. Moreover, custom casting opens doors for artistic expression; architects and designers can incorporate intricate motifs or historical replicas, enhancing the aesthetic appeal of structures.
Sustainability and Heritage
In an era where sustainability is paramount, custom cast iron pipe casting also presents an environmentally conscious option. Iron is infinitely recyclable, and using custom casting techniques minimizes waste by producing only what is needed, reducing excess material. Furthermore, it sustains traditional skills, preserving a heritage craft that has evolved over centuries.
Conclusion
Custom cast iron pipe casting represents more than just a manufacturing process; it embodies a commitment to precision, creativity, and longevity. As cities expand and infrastructure evolves, the demand for bespoke solutions continues to grow. By combining age-old techniques with contemporary design requirements, custom cast iron pipes serve as a bridge between past and future, offering a unique blend of functionality and aesthetics that stand the test of time. In every custom-crafted pipe, there lies a story of skilled craftsmanship, technological prowess, and a vision that transcends the ordinary.