In the ever-evolving landscape of industrial and commercial cooling systems,
heat exchangers and chillers play a pivotal role. Understanding their synergy can significantly impact the efficiency and cost-effectiveness of a facility's operations. This article delves into the intricacies of these components, laying out a comprehensive guide for businesses aiming to optimize their cooling systems.
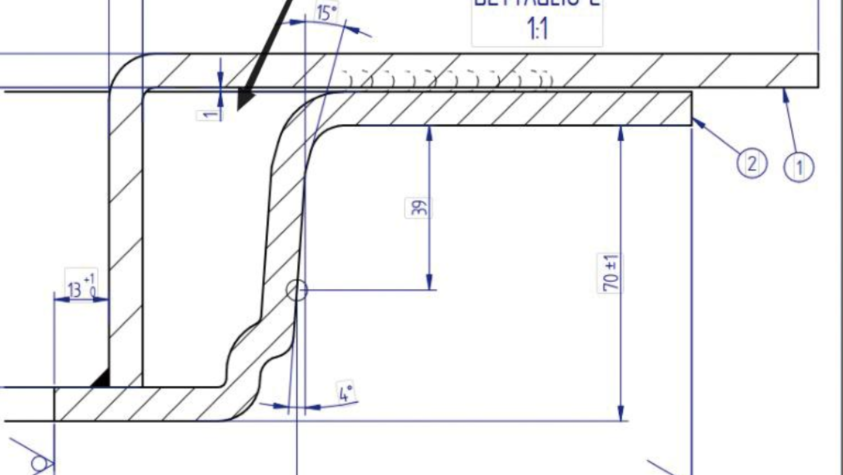
Heat exchangers and chillers, while often discussed separately, are interdependent when it comes to maintaining and improving HVAC systems, refrigeration processes, and industrial cooling applications. The experience of industry veterans indicates that the strategic integration of these units can lead to enhanced thermal management and energy savings.
At the core of these systems, heat exchangers facilitate the transfer of heat between two or more fluids without mixing them. They come in various designs, each tailored to specific applications. Plate heat exchangers, for instance, are recognized for their compact size and efficiency, ideal for systems where space is at a premium. Meanwhile, shell-and-tube heat exchangers are renowned for durability and high-pressure tolerance, making them suitable for demanding industrial environments.
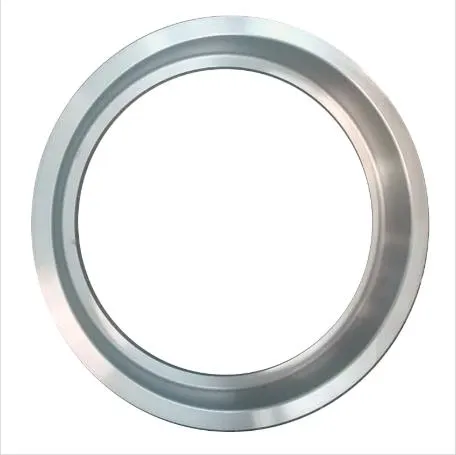
Chillers, on the other hand, are critical for removing heat from a liquid via a vapor-compression or absorption refrigeration cycle. They are instrumental in lowering the temperature of equipment and products, thus preventing heat-related malfunctions. Industrial experts emphasize the importance of selecting the appropriate type of chiller—air-cooled or water-cooled—based on factors like climate, space availability, and cooling requirements.
heat exchanger and chiller
The integration of heat exchangers within chiller systems is a practice endorsed by top experts for its efficiency. For example, incorporating a heat exchanger in the chiller loop can prevent fouling and scaling in the chiller coils by isolating the process fluid from the cooling water. This not only extends the lifespan of the chiller but also boosts its operational efficiency, a testament to the depth of expertise required in system design and implementation.
Real-world case studies indicate that firms optimizing their systems with this approach report significant reductions in operational costs. A prominent manufacturing plant revealed that after integrating heat exchangers into their chiller system, they achieved a 15% reduction in energy consumption, validating the authoritative claim that well-designed systems pay dividends.
Technical experts advocate for routine maintenance and monitoring of these systems to maintain their effectiveness. Trustworthiness in performance is achieved through regular cleaning and inspections, helping to identify potential issues before they escalate. Employing advanced sensors and predictive maintenance technologies can further enhance system reliability, ensuring that the heat exchanger and chiller combinations deliver consistent performance.
In summary, the seamless interaction between heat exchangers and chillers can unlock substantial benefits for industries reliant on precise temperature control. By leveraging the experience of skilled professionals and executing design strategies that incorporate both components, businesses can realize enhanced operational efficiency, reduced costs, and prolonged equipment longevity. This integrated approach underscores the significance of expertise and authority in the realm of thermal management solutions. With a focus on these critical interactions, companies can build cooling systems that are not only efficient but also resilient and trustworthy.