Industrial heat exchangers are critical components in various industries, including chemical processing, power generation, and refrigeration. Their primary function is to efficiently transfer heat between two or more fluids, ensuring optimized thermal management in complex industrial processes. When it comes to purchasing industrial heat exchangers, understanding the factors influencing their price is crucial for making informed investment decisions.
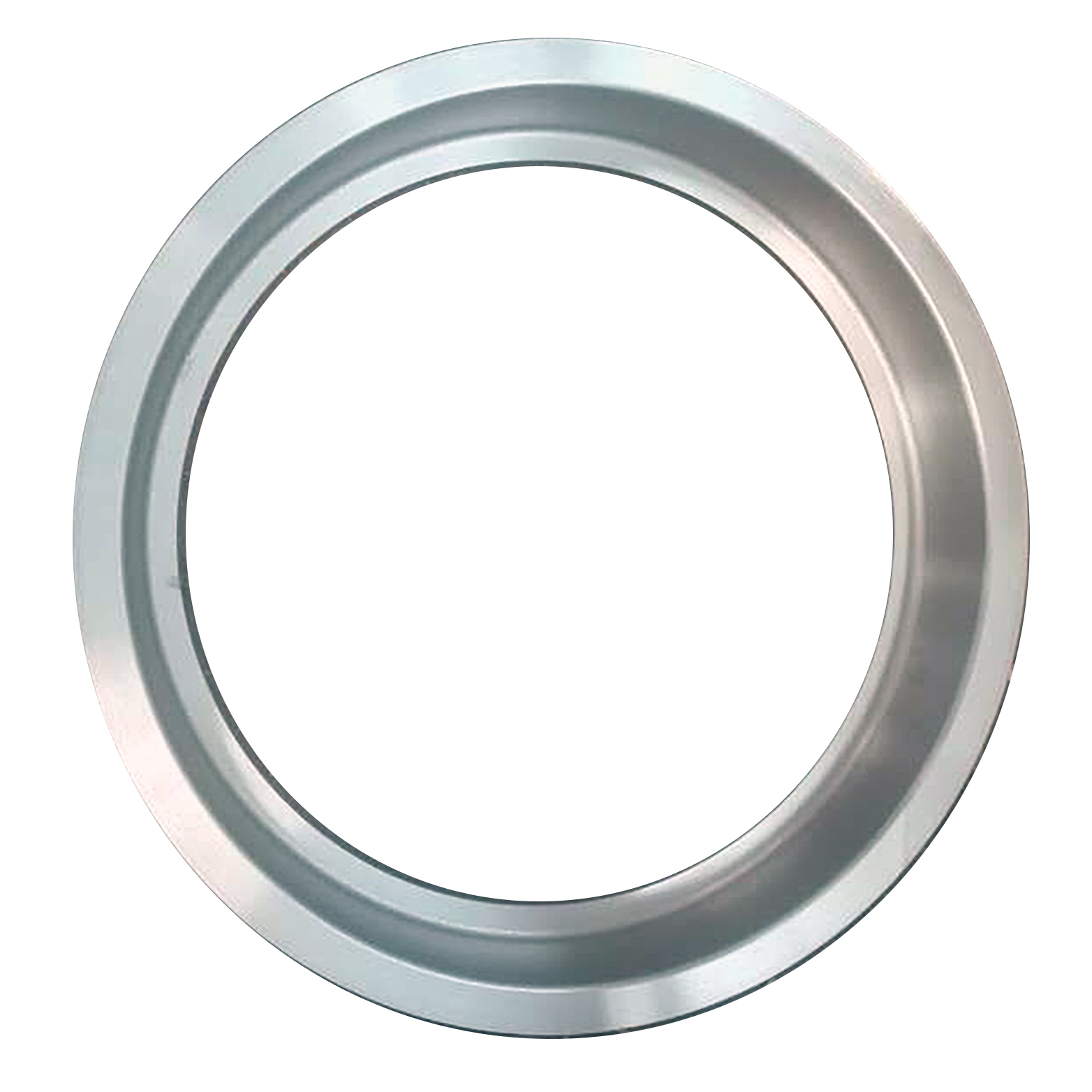
Several key factors determine the price of an industrial heat exchanger, and gaining insight into these variables can provide businesses with a competitive edge.
First and foremost, the type of heat exchanger plays a significant role in its pricing. The market offers a variety of designs, such as shell and tube, plate and frame, air-cooled, and double pipe heat exchangers, each catering to specific applications. Shell and tube heat exchangers are among the most common, valued for their durability and versatility. However, their complex construction can lead to a higher price point. On the other hand, plate and frame heat exchangers, known for their compact design and high efficiency, may offer a cost-effective solution for certain applications but might not be suitable for high-pressure scenarios.
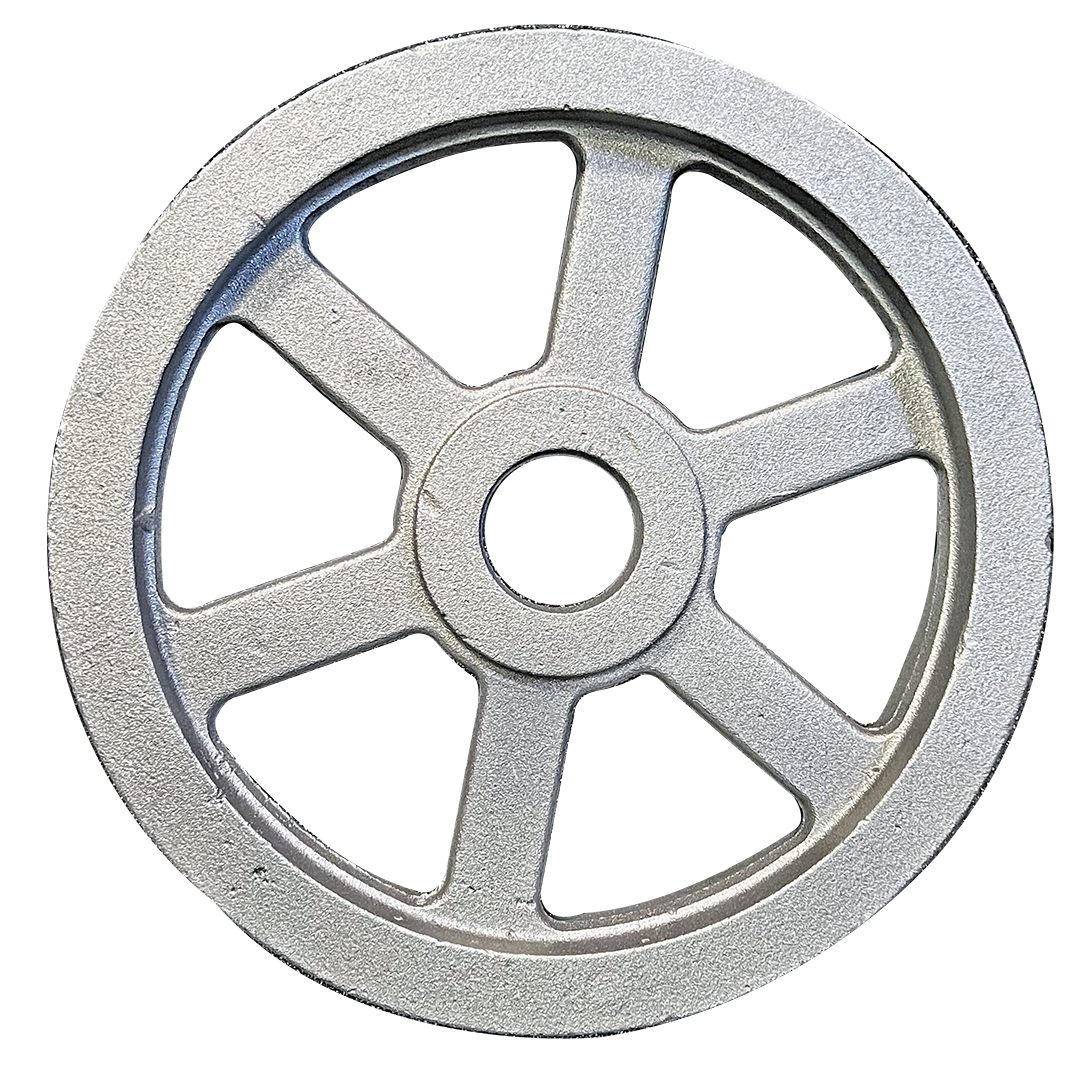
Material selection is another critical determinant of price. Depending on the operating environment and the nature of the fluids involved, materials such as stainless steel, titanium, or even exotic alloys may be required to prevent corrosion and ensure long-term functionality. Stainless steel is often preferred due to its balance of cost and corrosion resistance, but in industries dealing with corrosive substances, the use of more expensive materials like titanium may be justified, reflecting in a higher initial investment.
The size and capacity of the heat exchanger further influence the pricing structure. Larger heat exchangers with higher capacity demand more material and labor for manufacturing, naturally increasing costs. Furthermore, customizations to meet specific operational demands or space constraints can add to the expense. Businesses should carefully evaluate their process requirements and consult with experts to avoid over-specification, which can needlessly inflate costs.
industrial heat exchanger price
Professional installation services also contribute to the overall expenditure on industrial heat exchangers. Proper installation is crucial for optimal performance and longevity. Inadequate installation not only reduces efficiency but also raises operational and maintenance costs down the line. Partnering with experienced engineers ensures that the heat exchanger integrates seamlessly into existing systems, delivering anticipated performance and reliability.
Maintenance and operational efficiency should not be overlooked when assessing heat exchanger prices. Although the initial cost is an important consideration, the lifetime operational cost is a more telling metric of an exchanger’s true value. Investing in a high-quality, efficient heat exchanger can lead to substantial energy savings, reducing the total cost of ownership over time. Technologies like enhanced surface treatments can improve heat transfer coefficients, contributing to lower operational costs despite a higher initial purchase price.
Additionally,
industry standards and certifications can impact heat exchanger prices. Compliance with standards such as ASME, ISO, or API confirms reliability and safety, often justifying a higher price due to the increased assurance of quality and performance. Businesses should verify that the equipment meets all applicable regulations to ensure safety and avoid potential legal liabilities.
To navigate the complexities of purchasing an industrial heat exchanger, leveraging expertise from industry professionals is recommended. Consulting with engineers who specialize in thermal management can provide valuable insights into the appropriate type, material, and capacity needed for specific applications, aligning with both budgetary constraints and operational goals.
By considering these aspects, companies can make informed decisions, balancing upfront costs with long-term savings and performance, ultimately optimizing their industrial processes while maintaining financial prudence. Understanding these dynamics not only aids in selecting the most suitable heat exchanger but also strengthens negotiating positions, potentially leading to more favorable procurement terms.