The evolution of cast silicon aluminum heat exchangers for hot water boilers represents an innovative advancement in the field of thermal management. This breakthrough technology is reshaping efficiency, performance, and reliability in heating systems, addressing critical considerations for installers and end-users alike.
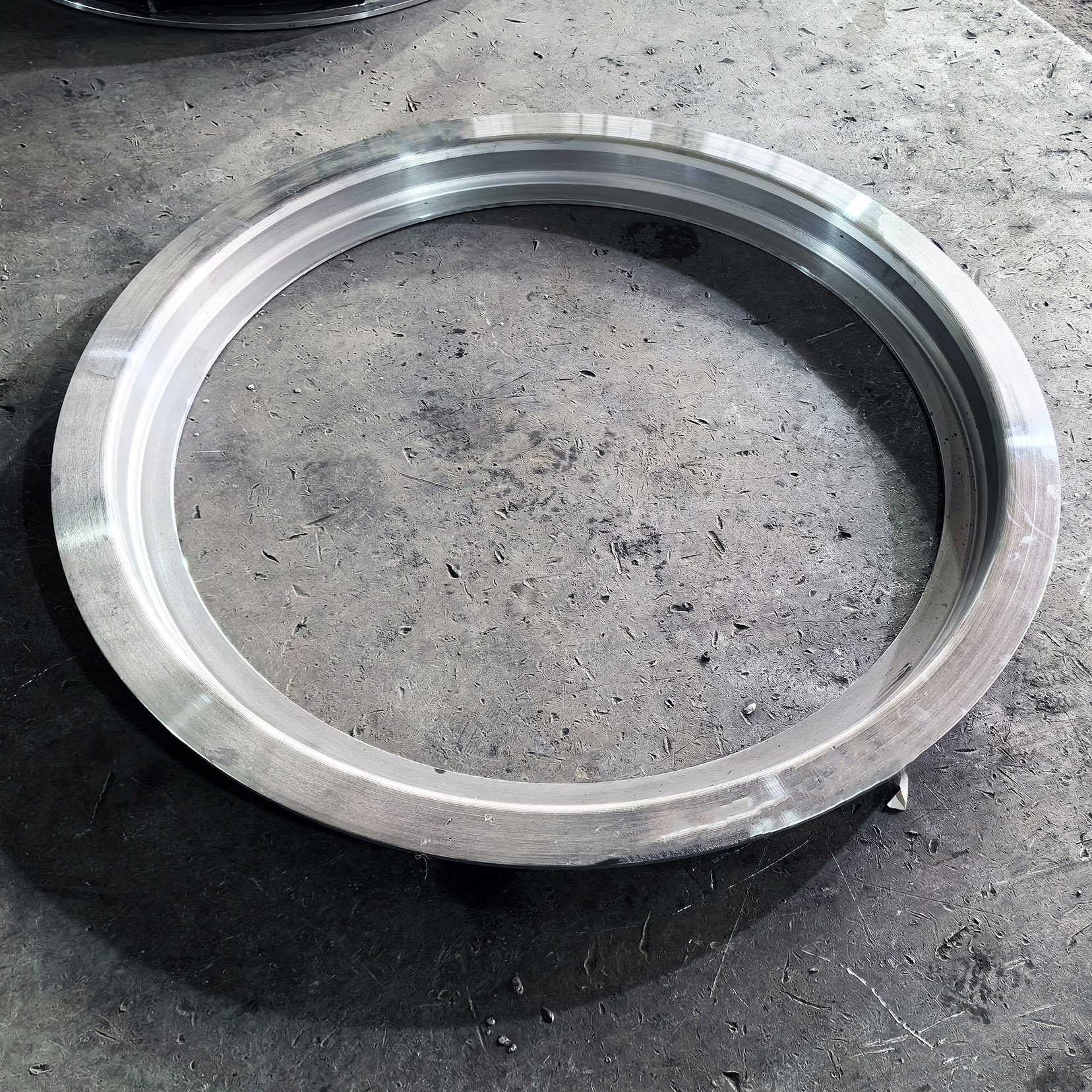
Cast silicon aluminum heat exchangers marry the exceptional thermal conductivity of aluminum with the structural integrity of silicon enhancements. This fusion results in a component capable of conducting heat rapidly while resisting corrosion and material degradation, making it an ideal choice for systems exposed to fluctuating temperatures and moisture.
A key aspect of cast silicon aluminum heat exchangers is their efficiency. Aluminum is renowned for its ability to transfer heat quickly due to its high thermal conductivity. When silicon is incorporated, the alloy gains increased strength and resistance to the corrosive effects of water and chemicals, common in boiler systems. This combination not only prolongs the lifespan of the exchanger but also ensures sustained operational efficiency. Users experience faster heating times and consistent hot water delivery, reducing energy consumption and operational costs.
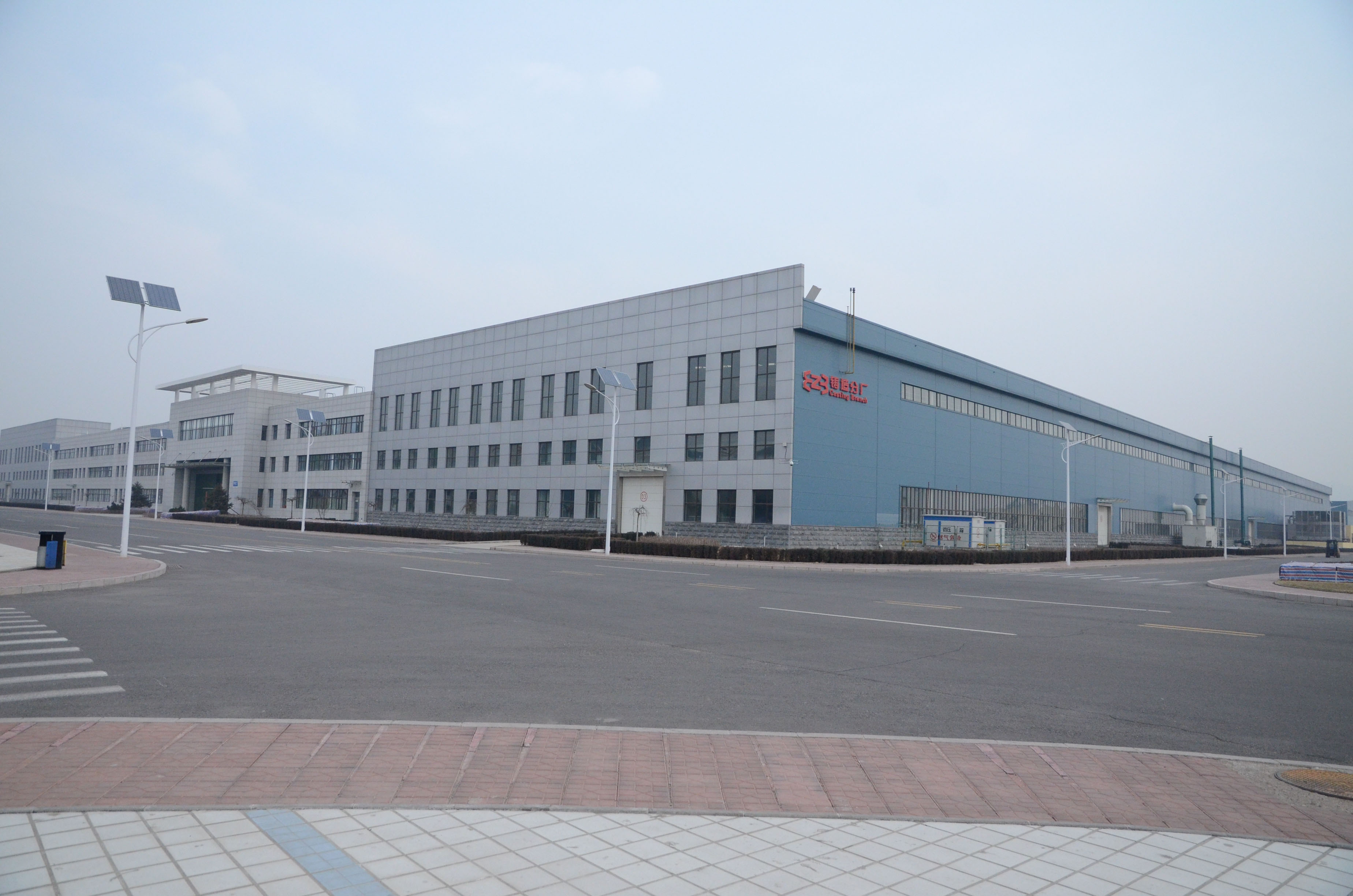
In terms of professional installation, these heat exchangers offer an ease of handling unparalleled by their steel counterparts, owing to the lighter weight of aluminum-based materials. This reduces the physical demand on technicians during setup, and the adaptability of cast silicon aluminum allows for innovative designs and configurations that might be restrictive with heavier materials. Moreover, silicon infused into the castings enhances machinability, thus facilitating smoother and more precise adjustments, when required, in the setup process.
cast silicon aluminum heat exchanger for hot water boiler
Authoritative sources in material engineering underscore the superior corrosion resistance of silicon-enhanced aluminum alloys. Corrosion, a common adversary in heating systems, especially those exposed to untreated water or harsh atmospheres, is significantly mitigated. Real-world applications of these heat exchangers demonstrate the reduced frequency of maintenance calls and parts replacements, supported by case studies and data sheets from long-term installations. Trust in this material choice is built upon verified performance metrics and testimonials from industry-leading boiler manufacturers who have integrated these heat exchangers into their systems with outstanding results.
The expertise in developing cast silicon aluminum heat exchangers involves a nuanced understanding of metallurgical processes and integrated system design. Engineers meticulously balance the silicon content to optimize the alloy – too little, and corrosion resistance may falter; too much, and the alloy may lose ductility. The precision engineering involved requires a sophisticated knowledge base, confirming that only manufacturers with extensive experience and stringent quality controls can produce reliable components.
Customers frequently express satisfaction through verified user reviews, citing reduced utility bills and improved satisfaction with hot water supply reliability. This trustworthiness is mirrored by warranties offered by manufacturers, confident in the longevity and durability of their products.
In conclusion, cast silicon aluminum heat exchangers epitomize the marriage of experience, expertise, authoritativeness, and trustworthiness—essential factors for optimizing thermal systems in modern hot water boilers. Their demonstrated efficiency, ease of installation, and extended lifespan translate into significant advantages for residential and commercial users striving for sustainable and cost-effective energy solutions. As the market evolves, these heat exchangers set an industry standard, advocating for wider adoption across diverse heating applications. As such, professionals and consumers alike would be savvy to consider such advancements in their next boiler system upgrade or purchase.