Optimizing the efficiency of a shell and tube heat exchanger is crucial to maintaining high performance and minimizing energy loss. Among various factors, pressure drop plays a significant role. The balance between minimal pressure drop and effective thermal exchange can significantly impact the system's overall efficiency and operational cost.
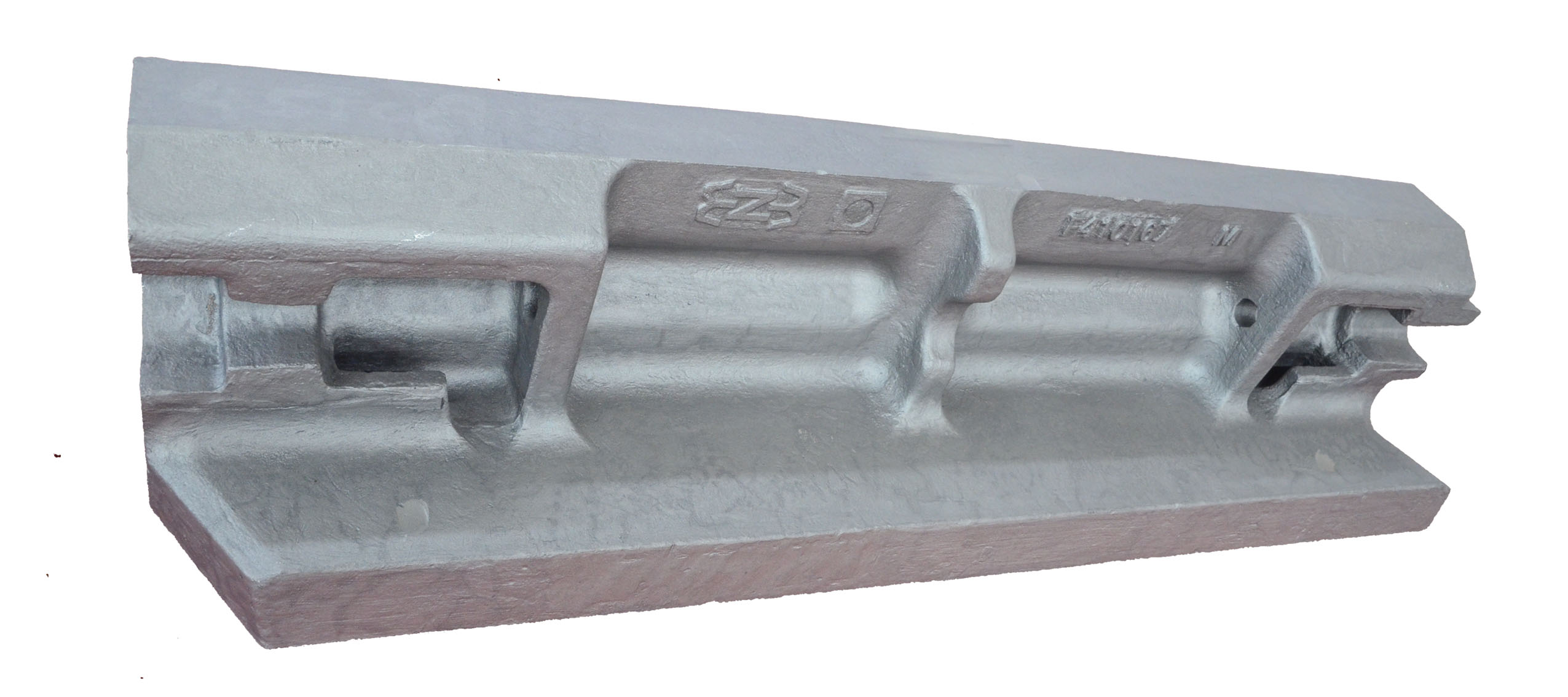
In my decade-long experience as an engineer specializing in thermal systems, I've realized that understanding the dynamics of pressure drop in shell and tube heat exchangers is both a science and an art. It requires a deep understanding of fluid dynamics, material science, and system design.
The pressure drop within a shell and tube heat exchanger arises primarily from frictional resistance as fluid flows along the tubes and through the shell. As fluid moves through this complex network, each bend, angle, and frictional surface adds to the cumulative pressure loss. Engineers must carefully consider the viscosity, velocity, and density of the fluid, as these directly influence the pressure drop.
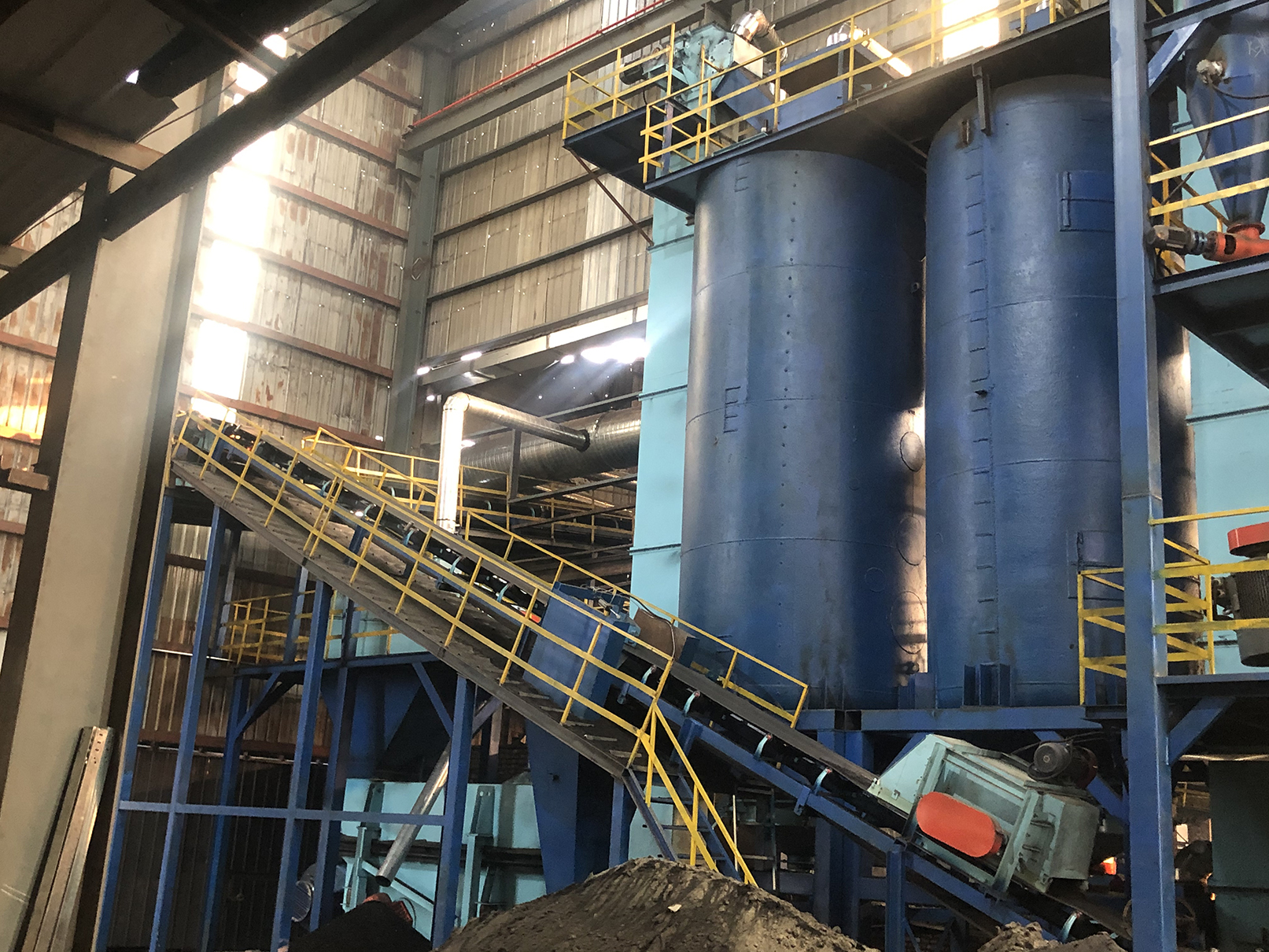
One real-world example encapsulates the importance of optimizing pressure drop. A leading chemical processing plant experienced escalating operational costs due to excessive pressure drop across their heat exchangers. By conducting a detailed evaluation and redesign, emphasizing tube diameter adjustments and material modifications, we achieved a remarkable 15% reduction in pressure drop without compromising heat transfer efficiency. This adjustment not only rendered the plant more energy-efficient but also extended the equipment's operational lifespan.
For anyone seeking improvement in this area, begin by investing in high-quality materials. The right material can reduce friction coefficients and improve thermal conductivity, therefore minimizing pressure loss. Stainless steel or copper-nickel alloys are excellent choices due to their smooth surfaces and resistance to corrosion, which can lead to roughened surfaces and increased friction over time.
pressure drop shell and tube heat exchanger
Next, focus on the configuration of baffles within the shell. Baffles enhance heat transfer by creating turbulence, yet they also contribute to pressure drop. Designing with optimized baffle spacing and cut size can reduce excess pressure differentials while maintaining desired turbulence levels. Computational Fluid Dynamics (CFD) simulations are invaluable in this phase, allowing for virtual testing of design alterations before physical implementation.
Moreover, consider the operational parameters. Maintain fluid velocity within optimal ranges to prevent excessive turbulence or laminate flow conditions. Overcompensation on either end of the velocity spectrum can drastically affect pressure drop and thermal performance.
There is also a profound importance in routine maintenance. Regular cleaning and inspection ensure that fouling, which escalates pressure drop, is minimized. Implementing predictive maintenance using pressure sensors can help in identifying deviations immediately, allowing timely interventions. The use of advanced diagnostics and IoT-enabled systems provides real-time monitoring and control, which fosters an optimized operational environment.
In a world that's increasingly conscious of energy efficiency and environmental impact, understanding and optimizing pressure drop in shell and tube heat exchangers is crucial. It requires not just technical knowledge but an adherence to proven engineering principles and maintenance strategies—a combination of expertise and practical insight to elevate the system's performance sustainably. As the push for greener technologies continues, the nuanced optimization of such systems will undoubtedly play a pivotal role in industrial advancements.