When it comes to the manufacturing of precise and complex components, investment casting stands out as a superior choice, merging centuries-old craftsmanship with modern technological advancements. This process, also known as lost-wax casting, is a time-honored method that has evolved to meet the needs of industries seeking high-quality parts with exacting standards.
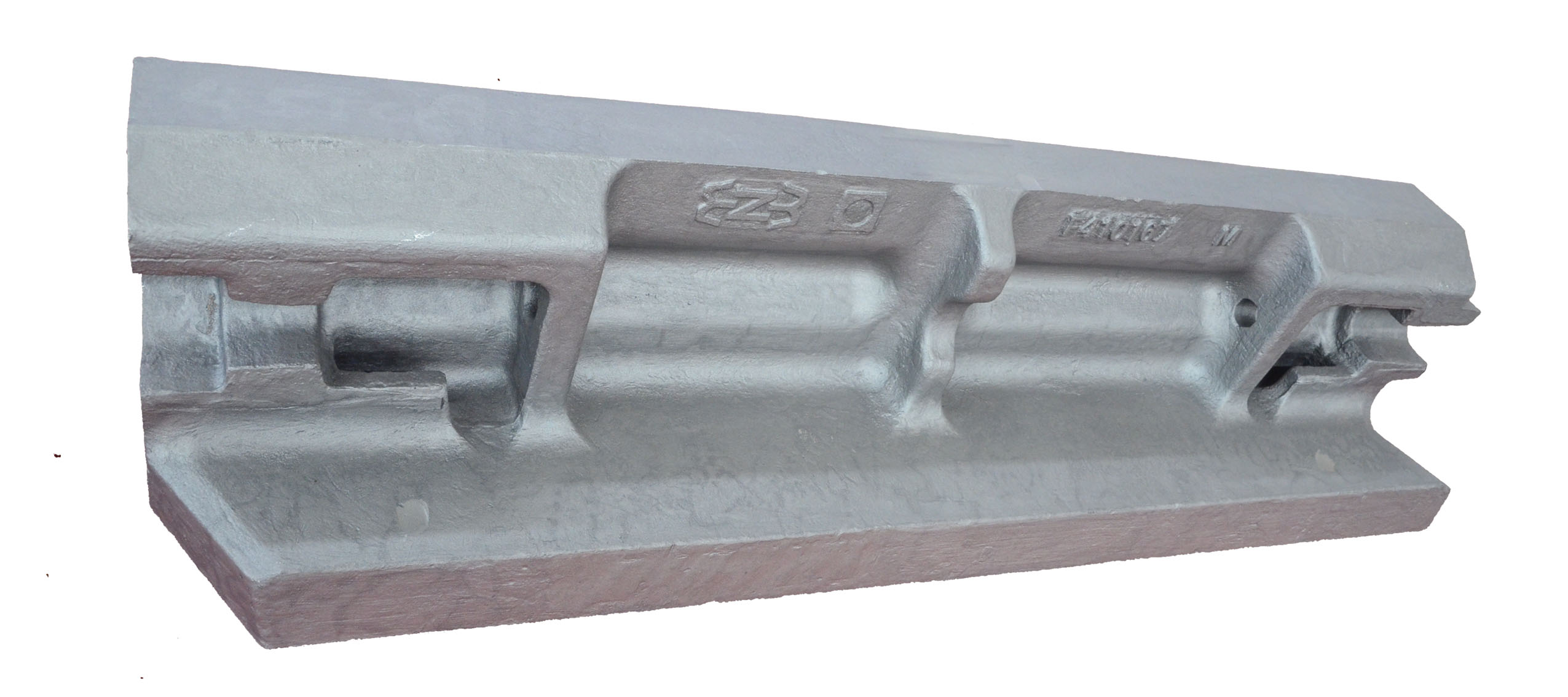
Investment casting parts are pivotal in industries ranging from aerospace and automotive to medical devices and industrial machinery. The process begins with the creation of a wax model of the desired part, which is then coated in a ceramic shell. Once hardened, the shell is heated to remove the wax, leaving a cavity into which molten metal is poured. Upon cooling, the ceramic mold is broken away, unveiling a metal casting that mirrors the initial wax design.
The true testament to the uniqueness and benefits of investment casting lies in its delivery of complex geometries. Unlike machining processes, investment casting can achieve intricate shapes and internal cavities without the need for additional operations. This capability translates into reduced production costs and time, a critical aspect in the fast-paced production environments.
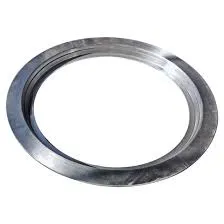
Expertise in choosing materials for investment casting is necessary to ensure optimal performance and longevity of parts. From stainless steel and carbon steel to more exotic alloys like Inconel and titanium, the selection depends on the intended application of the part. For instance, the aerospace industry, which demands parts capable of withstanding extreme temperatures and pressures, often opts for superalloys that provide durability and resilience.
Beyond material selection, the expertise in controlling casting parameters further underscores the professionalism of investment casting facilities. Variables such as pouring temperature, cooling rate, and mold material can significantly affect the mechanical properties of the finished part. Precision in controlling these parameters helps in producing parts with superior surface finishes and tight tolerances.
investment casting parts
Having an authoritative reputation in the investment casting industry is not only about producing quality parts but also about achieving certifications that validate the processes and materials used. Compliance with international standards such as ISO 9001 and AS9100 not only enhances trustworthiness but also opens doors to global markets. These certifications reflect a company's commitment to quality assurance and continuous improvement, essential for industries where failure is not an option.
Trustworthiness in investment casting production is further emphasized by transparent communication with clients. Providing detailed reports that trace the casting process steps from design to final inspection instills confidence in clients about the integrity of their parts. Advanced inspection techniques, including X-ray and 3D scanning, ensure parts meet stringent industry specifications and customer expectations.
Experience-rich investment casting facilities often engage in partnerships with clients during the design phase, offering insight into manufacturability and potential cost savings. This collaborative approach not only enhances the overall product design but also aligns production capabilities with customer needs, ensuring that the final product performs as intended.
Investment casting continues to hold its ground as a cornerstone in modern manufacturing by offering unmatched precision, quality, and efficiency. Its application across diverse industries is a testament to its versatility and reliability. As technologies evolve, investment casting facilities that embrace innovation and maintain stringent quality controls will continue to lead the market, fostering trust and delivering excellence in casting.