Optimizing heat exchanger capacity is a pivotal aspect of enhancing energy efficiency in industrial systems. With growing demands for performance and sustainability, choosing the right heat exchanger becomes a critical decision for engineers and facility managers. The following insights delve into essential considerations that can elevate the efficacy of these systems, drawing from real-world experience and industry expertise to underscore their authoritative and trustworthy nature.
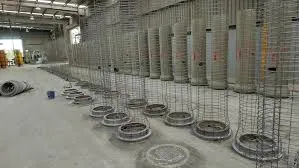
Heat exchanger capacity fundamentally influences the performance of industrial heating and cooling systems. It defines the system's ability to handle specified thermal loads, which is vital when designing or upgrading an HVAC system. Inefficient heat exchangers not only reduce system output but also escalate operational costs—a reality frequently encountered in industries processing large volumes of fluids or gases at varying temperatures.
Selecting the correct type of heat exchanger is the first step towards maximizing capacity. Shell-and-tube, plate, and air-cooled exchangers each offer unique benefits but selecting the wrong type can lead to suboptimal performance. For instance, shell-and-tube heat exchangers are renowned for their robustness and flexibility in handling high-pressure applications. However, plate heat exchangers might be more suitable for tasks requiring a compact design and higher thermal efficiency, such as in food processing industries. Real-life case studies have illustrated that a misalignment between exchanger type and application parameters often results in dramatic efficiency losses.
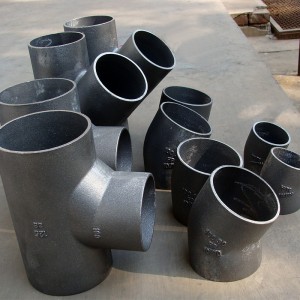
Moreover, the material composition of heat exchangers significantly affects capacity and longevity. Innovations in material science have introduced advanced alloys and composite materials that enhance thermal conductivity while resisting corrosion—a fundamental requirement in chemical industries where corrosive fluids are prevalent. As experts in the field note, cutting-edge materials not only enhance exchanger capacity but also ensure longer service life, reducing downtime and maintenance costs.
heat exchanger capacity
The exchanger's design intricacies, including surface area and flow arrangement, also dictate capacity. Maximizing the surface area in contact with fluids or optimizing flow patterns can vastly improve heat transfer rates. Counterflow and crossflow configurations, for example, offer varied capacities and efficiencies. Illustrative examples from telecommunications cooling systems reveal how strategic design adjustments in these parameters can achieve superior heat exchange capabilities without significant increases in system size.
The integration of cutting-edge technology, like computerized thermal modeling and real-time monitoring systems, further refines heat exchanger functionality. These technologies allow for predictive maintenance and dynamic adjustments to operational conditions, ensuring that the exchanger consistently operates at its intended capacity. Engineers recount instances where implementing these technologies has preemptively identified performance bottlenecks, safeguarding against unexpected system disruptions.
Industry regulations and environmental considerations, too, influence heat exchanger capacity choice and optimization. Compliance with industry standards ensures safety and reliability, reinforcing the authoritative credibility of the plant's operations. Regulatory adherence is often non-negotiable, as outlined by numerous expert assessments, in sectors such as pharmaceuticals and power generation, where the stakes are especially high.
In conclusion, optimizing heat exchanger capacity is a multidimensional endeavor requiring an amalgamation of precise selection, innovative design, material prowess, and technological integration. Professionals tasked with these choices must leverage their expertise, employ comprehensive strategies, and consistently adhere to industry standards, thereby ensuring efficiency, sustainability, and reliability in heat exchange applications. Through informed decision-making grounded in experience and expertise, significant advancements in industrial system performance are not only achievable but also sustainable, cementing the value of heat exchanger capacity optimization in modern industries.