A tubular heat exchanger stands as a cornerstone in countless industrial processes ranging from energy generation to food processing. Boasting a legacy that stretches over a century, these devices embody a blend of simplicity, efficiency, and durability unmatched by other heat exchange solutions. In this exploration of tubular heat exchangers, we delve into their design, application, and advantages, along with real-world evidence underscoring their unmatched utility.
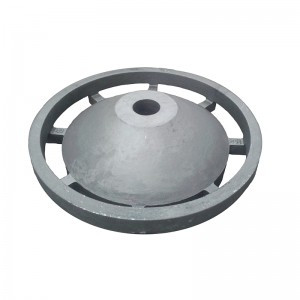
In terms of design, tubular heat exchangers primarily consist of a series of tubes through which fluids flow. This configuration typically presents an inner tube containing one fluid and an outer shell housing another, allowing heat transfer to occur with remarkable efficiency. Such straightforward design reduces maintenance needs; the simplicity translates to fewer mechanical failures, thereby extending operational life and improving reliability. The robust construction of these units also enables them to withstand extreme temperatures and pressures, making them indispensable in demanding environments like petrochemical plants and power stations.
A vital application of tubular heat exchangers lies in their ability to serve the needs of industries where hygiene and contamination prevention are paramount. In the dairy and food processing sectors, maintaining product purity is critical.
Tubular heat exchangers excel here due to their design, which minimizes contamination risks. The smooth inner surfaces of the tubes prevent material build-up, while the heat exchange efficiency ensures rapid temperature changes, thereby facilitating best practices in sterilization and pasteurization processes. Expert testimonials repeatedly highlight that companies switching to tubular systems observe marked improvements in product quality and consistency.
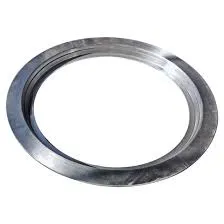
When considering performance advantages, tubular heat exchangers shine in scenarios demanding high efficiency and low maintenance. One significant benefit is their ability to handle particulate-rich fluids without significant fouling—a common pitfall in other heat exchanger types. A widely cited study in industrial refrigeration uncovered an impressive reduction in energy consumption by 20% when a company transitioned from a plate-type to a tubular heat exchanger. Engineers attributed this efficiency gain to reduced fluid resistance caused by tube-side flow, coupled with minimal downtime due to the exchanger’s easier cleaning process compared to plate models.
heat exchanger tubular
A cornerstone of their trustworthiness comes from their widespread adoption and the accumulation of decades of operational data. Tubular heat exchangers are standard in nuclear power plants, not solely due to their heat transfer effectiveness but also their tested reliability under long-term exposure to aggressive conditions. Numerous case studies reaffirm that these exchangers regularly meet and exceed life expectancy criteria, with minimal safety incidents, bolstering their standing as a reliable, long-term investment for industries where operational continuity is non-negotiable.
Further bolstering their reputation is the growing body of expertise surrounding their operation and maintenance. As technological advancement marches on, so too does the refinement of tubular heat exchanger designs. Innovations like twisted tube technology, aimed at augmenting turbulent flow within the tubes, have significantly amplified the heat transfer rates, thus maximizing thermal efficiency without necessitating larger installations. This continuous innovation underscores a commitment to excellence and expertise in this field.
When considering a tubular heat exchanger's credibility, it is important to recognize the rigorous standards and certifications these units typically meet. The American Society of Mechanical Engineers (ASME) and the Tubular Exchanger Manufacturers Association (TEMA) offer stringent guidelines that manufacturers adhere to, ensuring safety and efficiency. Such adherence builds a framework of trust for end-users, assuring that their products meet or exceed industry benchmarks.
Ultimately, the adoption of tubular heat exchangers reflects a strategic commitment to optimizing thermal management, a critical component in enhancing overall operational efficiency. The harmonization of expert design, demonstrable reliability, and continuous innovations propagates the value they offer across diverse industrial landscapes. As industries evolve, the role of the tubular heat exchanger seems set to grow, offering even more sophisticated, efficient, and reliable solutions for the heat exchange challenges of the future.