Heat resistant castings are a breakthrough in materials engineering, designed to withstand extreme temperatures while retaining structural integrity and longevity. These castings find widespread applications across industries such as aerospace, automotive, chemical processing, and power generation, which demand materials that can perform under high-temperature conditions without degrading.
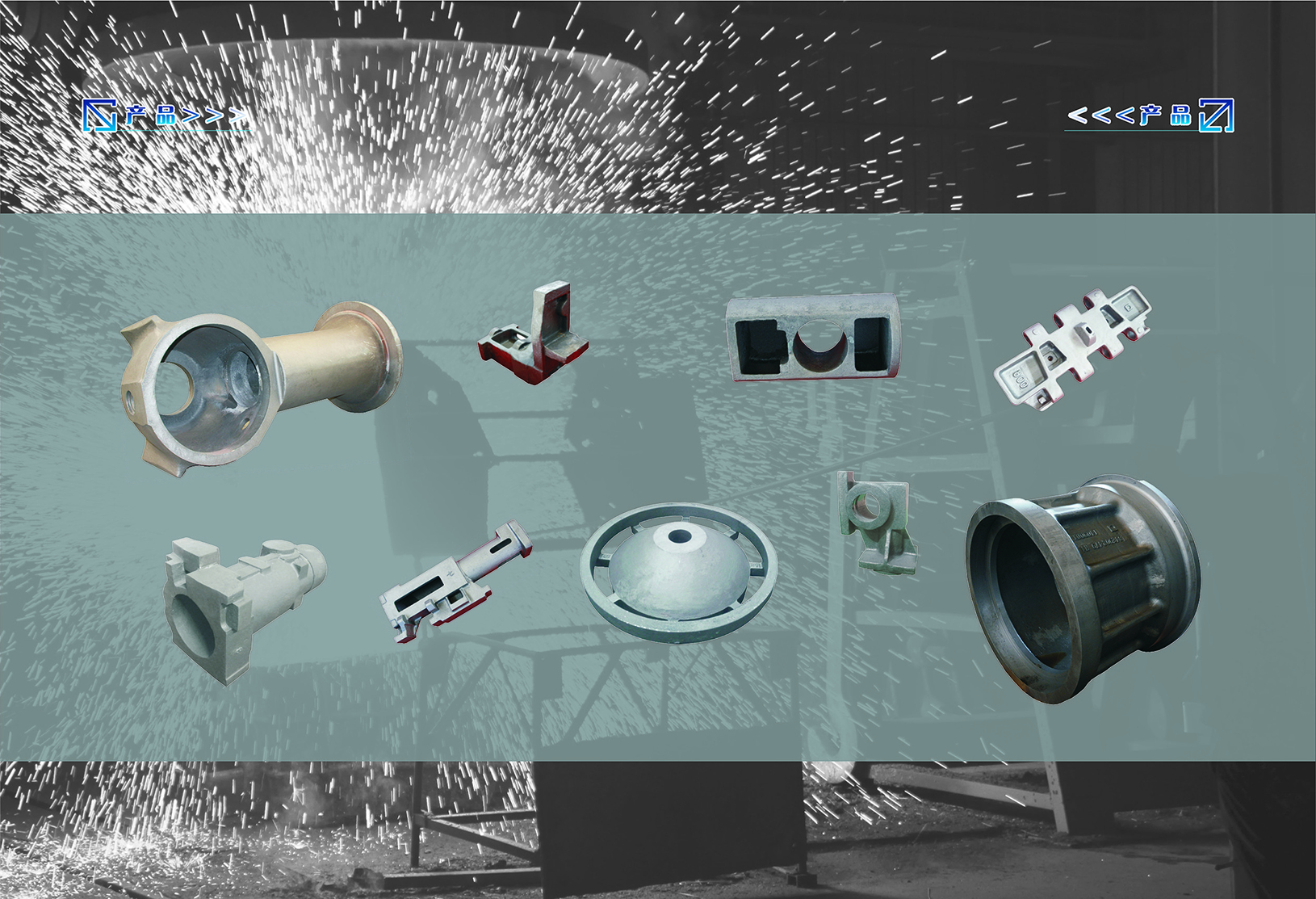
The science behind heat resistant castings lies in their composition. Typically made from specialty alloys, these castings often include elements such as nickel, chromium, and molybdenum, which enhance their ability to resist oxidation and thermal fatigue. This engineered composition makes them ideal for environments where standard metals would fail due to thermal expansion or chemical corrosion.
In the aerospace industry, for instance, heat resistant castings are crucial in the manufacture of jet engines. The internal components of these engines must endure not only the mechanical stress of high-speed rotation but also extreme heat generated during operation. By utilizing castings engineered for high thermal resistance, manufacturers ensure reliability and safety in aircraft performance.
Such expertise in material performance underscores the critical role these castings play in modern aviation.
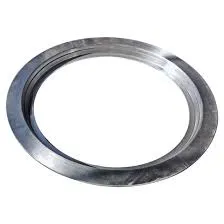
The expertise required to produce heat resistant castings extends beyond mere material selection. The casting process itself is complex, involving precise control over factors like mold materials, cooling rates, and casting temperatures. Foundries specializing in these products employ rigorous quality control measures, using advanced diagnostic tools and testing to verify the integrity and performance of each casting. This meticulous attention to detail assures clients of both the durability and trustworthiness of these components.
heat resistant castings
From a trustworthiness perspective, heat resistant castings are essential in power plants, especially those utilizing fossil fuels or concentrating solar power. Here, components such as turbine blades or heat exchangers must operate continuously in high-temperature environments. The failure of these parts could lead to costly downtimes or even catastrophic failures. Trust in the material's performance is non-negotiable, which is why these industries lean heavily on well-documented experiences, certifications, and the proven track records of manufacturers specializing in heat resistant technologies.
For petrochemical industries, expertise in handling corrosive materials at elevated temperatures is paramount. Heat resistant castings serve as critical components in reactors and piping systems, where they must resist not only heat but also chemical attack. The expertise involved in designing castings with such dual resistance is a testament to the advanced metallurgical skills that companies bring to bear, ensuring clients receive components that not only perform efficiently but also enhance operational safety.
In conclusion, the real-world experience and expertise involved in producing heat resistant castings make them indispensable to industries that operate under severe conditions. Their authoritativeness comes from a legacy of applications that have consistently demonstrated reliability under pressure. As technology advances, the continuous development and refinement of these castings will reinforce their status as a cornerstone of industrial resilience and innovation. By focusing on these key areas, businesses can better navigate the challenges posed by high-temperature applications, maintaining operational efficiency and safety through informed material choices.