Sand casting remains a pivotal technique in the manufacturing landscape, deeply rooted in both tradition and innovation. This versatile process is instrumental in producing intricate metal components, catering to various sectors from automotive to aerospace. The magic lies in its simplicity and the profound expertise required to perfect it, bridging the gap between ancient craftsmanship and modern technology.
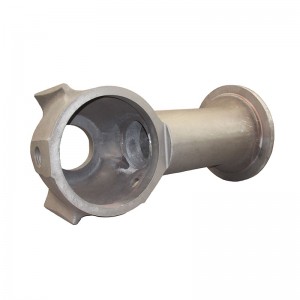
At its core, sand casting involves creating a mold from a sand mixture and pouring molten metal into it, which then solidifies into the desired shape. But while the principle is straightforward, mastering the nuances demands an in-depth understanding of materials, techniques, and meticulous quality control.
Experience in sand casting teaches us that the type and condition of sand used significantly affect the quality of the final product. Foundries often rely on silica sand due to its availability and favorable properties. Expert foundry engineers constantly experiment with various sand additives and binders to enhance mold strength and surface finish. They must carefully balance these factors to avoid common defects like burn-on, metal penetration, and sand inclusions. Thus, a deep expertise in choosing the right sand mixture cannot be overstated.
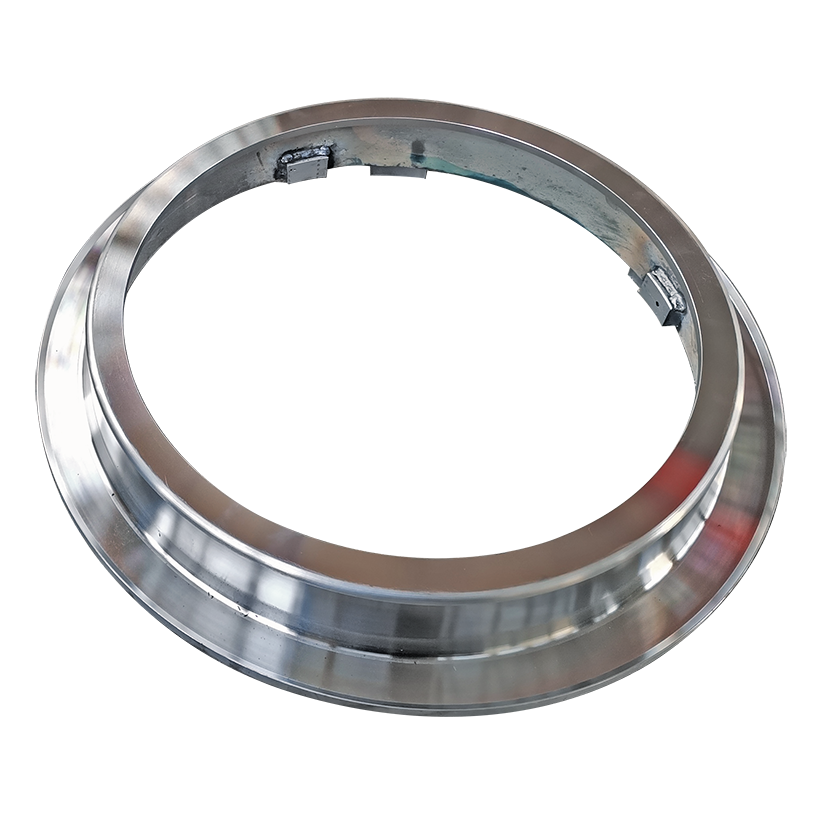
In terms of expertise, the design of gating systems in sand casting is critical. Gating refers to the pathways through which molten metal flows into the mold cavity, and improper design can lead to turbulence and defects like porosity. Experienced designers employ computer-aided simulations to predict the flow of metal and optimize these pathways. This reduces trial and error and ensures that the final castings meet stringent industry standards.
sand casting
The authoritativeness of a sand casting operation not only hinges on technical expertise but also on the quality assurance systems in place. Leading foundries integrate cutting-edge inspection tools such as X-ray radiography and ultrasonic testing to ensure the integrity and durability of cast components. Adhering to international quality standards such as ISO 9001 further cements their reputation, instilling trust among clients and partners.
Trustworthiness in sand casting is ultimately determined by the reliability and durability of the products manufactured. Long-term partnerships with industries that demand precision, such as aerospace, require a track record of delivering castings that withstand rigorous testing and demanding environments. Clients often seek references and case studies that illustrate not just past successes, but also a company's commitment to continuous improvement and innovation.
Sand casting also embraces sustainability, a vital aspect for today’s environmentally-conscious businesses. By nature,
sand is reusable in the casting process, significantly reducing waste. Moreover, the industry is advancing in reclaiming and recycling spent sand, which aligns with greener manufacturing practices and offers a competitive edge in markets increasingly making sustainability a buying criterion.
In conclusion, while sand casting may seem a relic of the past, its role in creating the future of industrial manufacturing is undeniable. This process embodies a blend of experience-driven craftsmanship and cutting-edge technology, offering unparalleled flexibility in design and production. For companies seeking reliable and expert metal component manufacturing, investing in experienced sand casting foundries is not merely a choice, but a strategic imperative.