Unlocking the Potential of Carbon Steel Lost Wax Casting in Manufacturing
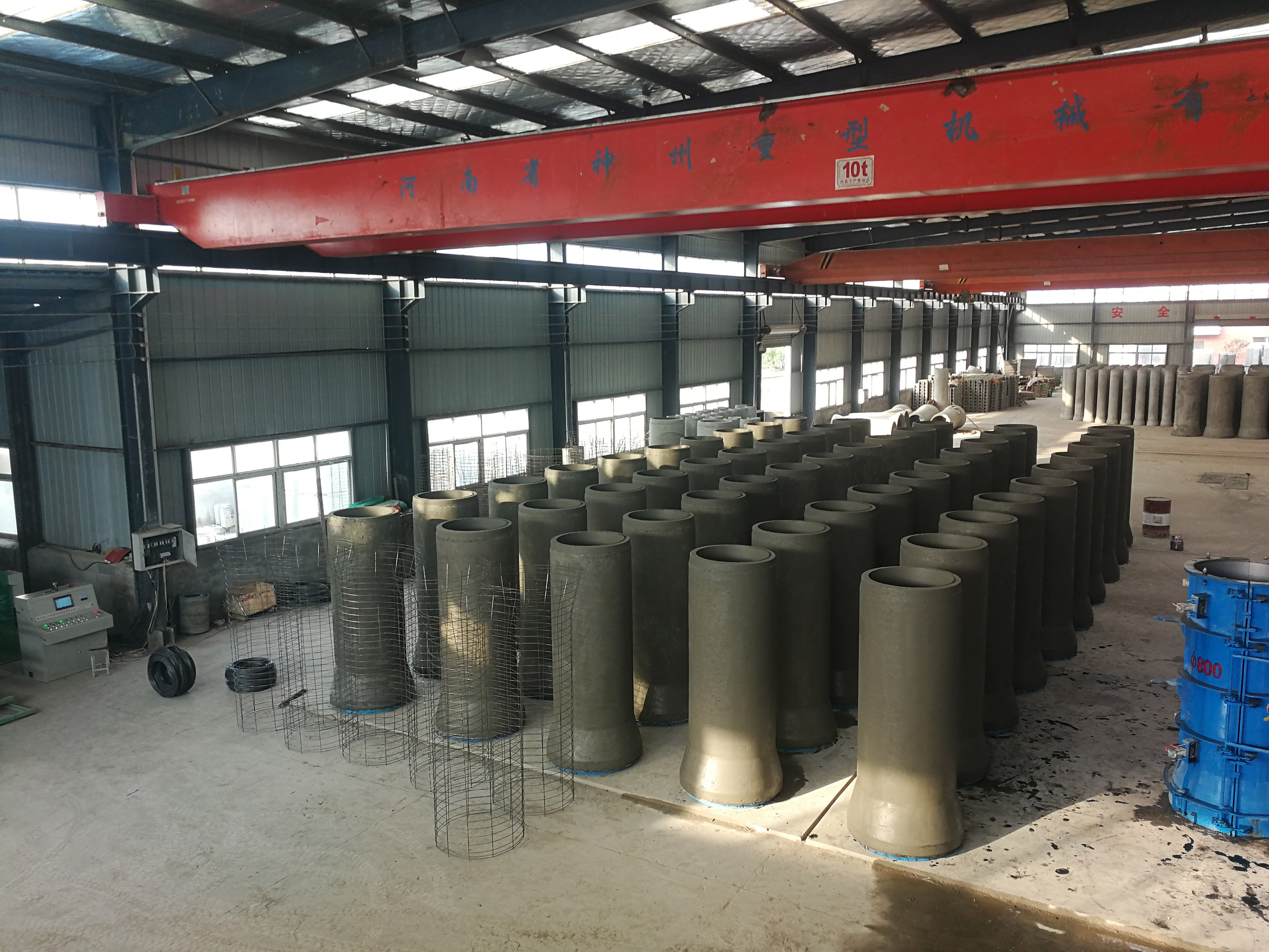
In the intricate world of manufacturing, precision and quality form the backbone of successful production processes. One technique that stands out for its remarkable ability to deliver both is carbon steel lost wax casting. Those familiar with this process understand the unique combination of historical craftsmanship and modern technology that makes it one of the most reliable methods for producing complex metal components.
Lost wax casting, often referred to as investment casting, is a venerable technique that traces its roots back thousands of years. Despite its traditional origins, the process has evolved significantly, leveraging advancements in metallurgical science and engineering to meet contemporary demands. When carbon steel, a material known for its strength and versatility, is introduced into this process, the results can be nothing short of extraordinary.
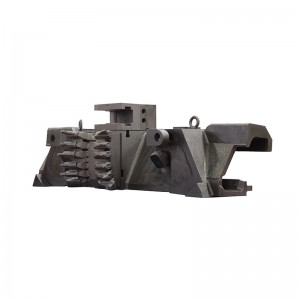
The process begins with the creation of a wax model of the desired component, which may be designed using advanced computer-aided design (CAD) software. This model serves as a precise replica, capturing every intricate detail that the final carbon steel product will exhibit. The wax model is then encased in a ceramic shell, which, once hardened, serves as a mold.
A critical phase of lost wax casting is the removal of the wax, typically achieved through a high-temperature process known as burnout.
This leaves a hollow ceramic shell ready for casting. It is at this point that the superior qualities of carbon steel become evident. Known for its exceptional hardness, durability, and resistance to wear and tear, carbon steel is melted and carefully poured into the mold. The precise handling of carbon steel in this stage ensures that the final product retains all of the intricate details of the original design, offering unparalleled accuracy and quality.
One of the primary reasons manufacturers opt for carbon steel lost wax casting is its ability to produce components with complex geometries that would be challenging or impossible to achieve through traditional machining. This makes it an ideal choice for industries such as aerospace, automotive, and machinery manufacturing, where precision and reliability are non-negotiable.
carbon steel lost wax casting
Moreover, the process is highly efficient in terms of material usage. By limiting wastage and optimizing the use of carbon steel, manufacturers can ensure both environmental sustainability and economic viability. The cost-effectiveness of this method is further amplified by the fact that it minimizes the need for further machining or finishing processes, which can be resource-intensive.
From a professional standpoint, the strategic use of carbon steel lost wax casting can significantly enhance the performance of the products. Engineers and designers have increasingly leaned towards this method to exploit its full potential, generating components that withstand high stress and adverse environmental conditions without compromising on weight or aesthetics.
A vital aspect of this technique is the skill and expertise required, underscoring the need for a profound understanding of materials science and casting principles. Working with carbon steel in the context of lost wax casting necessitates a distinctive set of capabilities—balancing the thermal dynamics involved with maintaining the structural integrity of the steel and the mold.
Finally, the trust that industries place in this casting process is a testament to its established reputation in the sector. By consistently delivering robust and reliable components, carbon steel lost wax casting has earned its place as a pillar of modern manufacturing processes, attesting to its trustworthiness and authority in delivering high-quality results.
In conclusion, the integration of carbon steel with lost wax casting illuminates the symbiotic relationship between tradition and innovation. This method not only stands as a beacon of manufacturing excellence but also as an embodiment of enduring expertise and trust in a world increasingly driven by the demand for high-performance materials and components.