In industrial applications, the effectiveness of a shell and tube heat exchanger plays a pivotal role in optimizing energy efficiency and process performance. Drawing upon extensive expertise in thermal systems, this article delves into the nuanced benefits and considerations that establish shell and tube heat exchangers as a cornerstone in heat transfer technology.
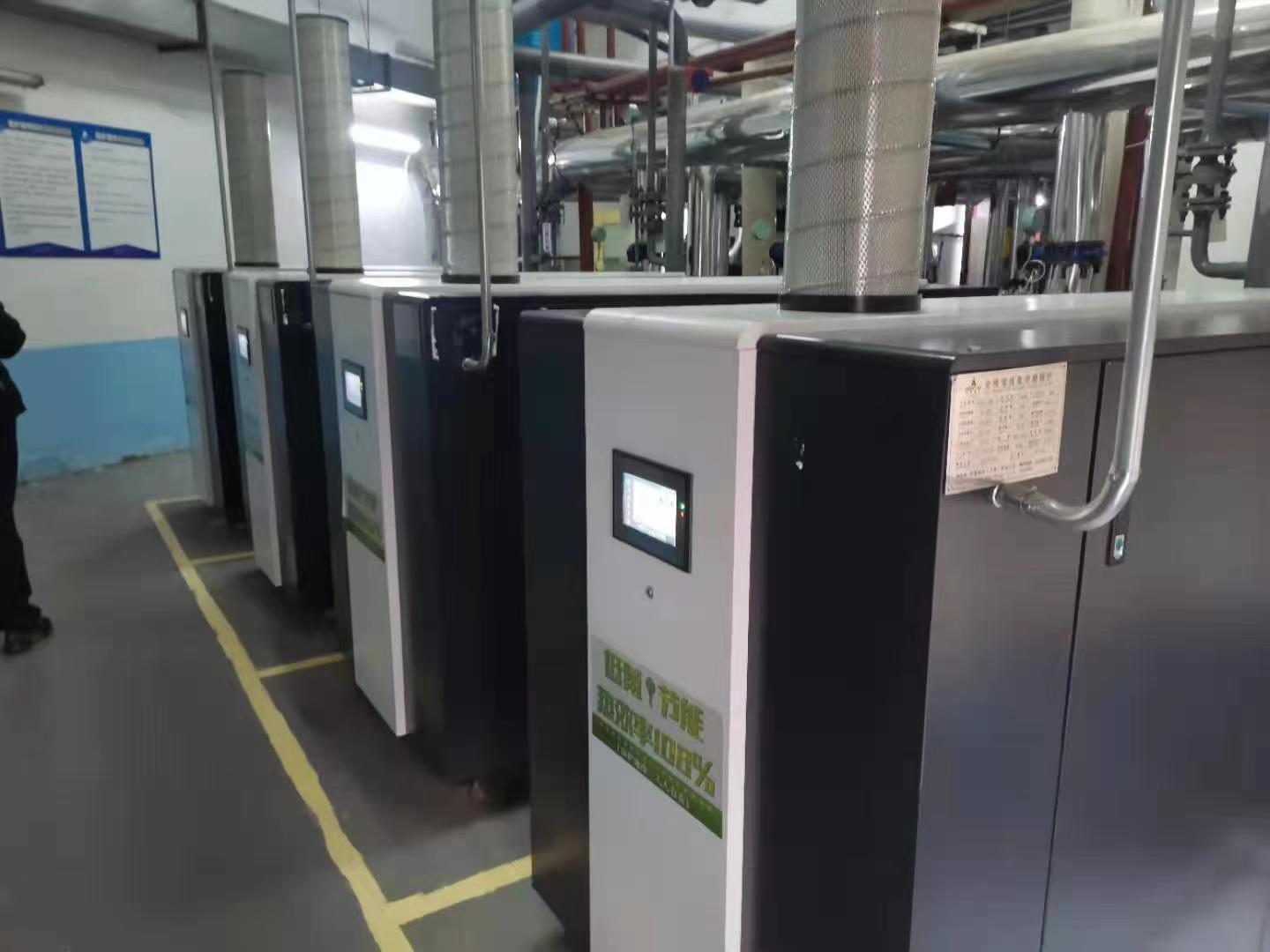
Shell and tube heat exchangers are celebrated for their robustness and versatility across a broad spectrum of industries, including chemical processing, refineries, and HVAC systems. The design of these exchangers facilitates efficient heat transfer between two fluids, one flowing through the tubes and another around them within the shell, a configuration that can be tailored to meet specific thermal and pressure requirements.
A key advantage of shell and tube heat exchangers is their adaptability to high-pressure applications. This is essential in industrial sectors where the integrity of materials under high pressure is non-negotiable. Their construction allows for significant thermal expansion, accommodating varying temperatures with minimal risk of mechanical stress or failure. Compared to plate heat exchangers, shell and tube systems offer a higher pressure resistance, making them suitable for applications involving hazardous or volatile fluids.

From a maintenance perspective, these heat exchangers offer a high degree of reliability. Their design allows for straightforward cleaning and inspection, which is crucial for maintaining high operational efficiency. Periodic maintenance ensures longevity and reduces downtime, particularly in industries where uninterrupted processing is critical. Innovative cleaning techniques, such as in-place cleaning and advanced inspection methods, have further enhanced the lifespan and serviceability of these units.
The effectiveness of a shell and tube heat exchanger is heavily influenced by its design parameters, such as the selection of tube materials and the configuration of baffles within the shell. Materials like stainless steel and titanium are commonly employed to resist corrosion and withstand high-temperature operations. The incorporation of baffles plays a vital role in creating turbulence, thereby enhancing the heat transfer coefficient by promoting greater fluid dynamics within the shell. Tailoring these design components can significantly impact the exchanger's performance in specific industrial applications.
effectiveness of shell and tube heat exchanger
Another pivotal aspect influencing the effectiveness of shell and tube heat exchangers is their design flexibility. They can be engineered to accommodate a variety of tube diameters, lengths, and shell configurations, ensuring compatibility with spatial constraints and process demands. This versatility makes them instrumental in retrofitting existing systems where process optimization is necessary without overhauling existing infrastructure.
Furthermore, advances in computational fluid dynamics (CFD) have revolutionized the design and optimization of shell and tube heat exchangers. CFD modeling allows engineers to simulate complex fluid flow patterns and thermal characteristics with high accuracy, enhancing the exchanger's performance before physical prototypes are constructed. This capability not only reduces development costs but also minimizes the environmental impact by optimizing resource use from the initial stages of design.
Trustworthiness and authoritativeness in the use of shell and tube heat exchangers are reinforced through adherence to international standards and certifications, such as those from the American Society of Mechanical Engineers (ASME) and the Heat Exchange Institute (HEI). Compliance with these standards ensures that design, manufacturing, and testing phases meet stringent criteria for safety and performance, critical to building confidence among industrial stakeholders.
In summary, the effectiveness of shell and tube heat exchangers in industrial settings is derived from their robust design, adaptability to high-pressure and high-temperature environments, and ease of maintenance. Their global trustworthiness is underscored by compliance with engineering standards and the utilization of advanced modeling techniques for optimal performance. These features collectively make shell and tube heat exchangers an indispensable asset in modern industrial operations, continually evolving to meet the dynamic needs of energy and thermal management across varied applications.