Cement casting, a fundamental technique in the construction and artistic industries, has evolved significantly over the years. Its versatility and strength have made it an indispensable part of many projects, ranging from large-scale architectural designs to intricate decorative art pieces. Drawing from decades of industry experience, expertise, and a commitment to trustworthiness, this article explores the intricacies of cement casting and provides valuable insights into its modern applications.
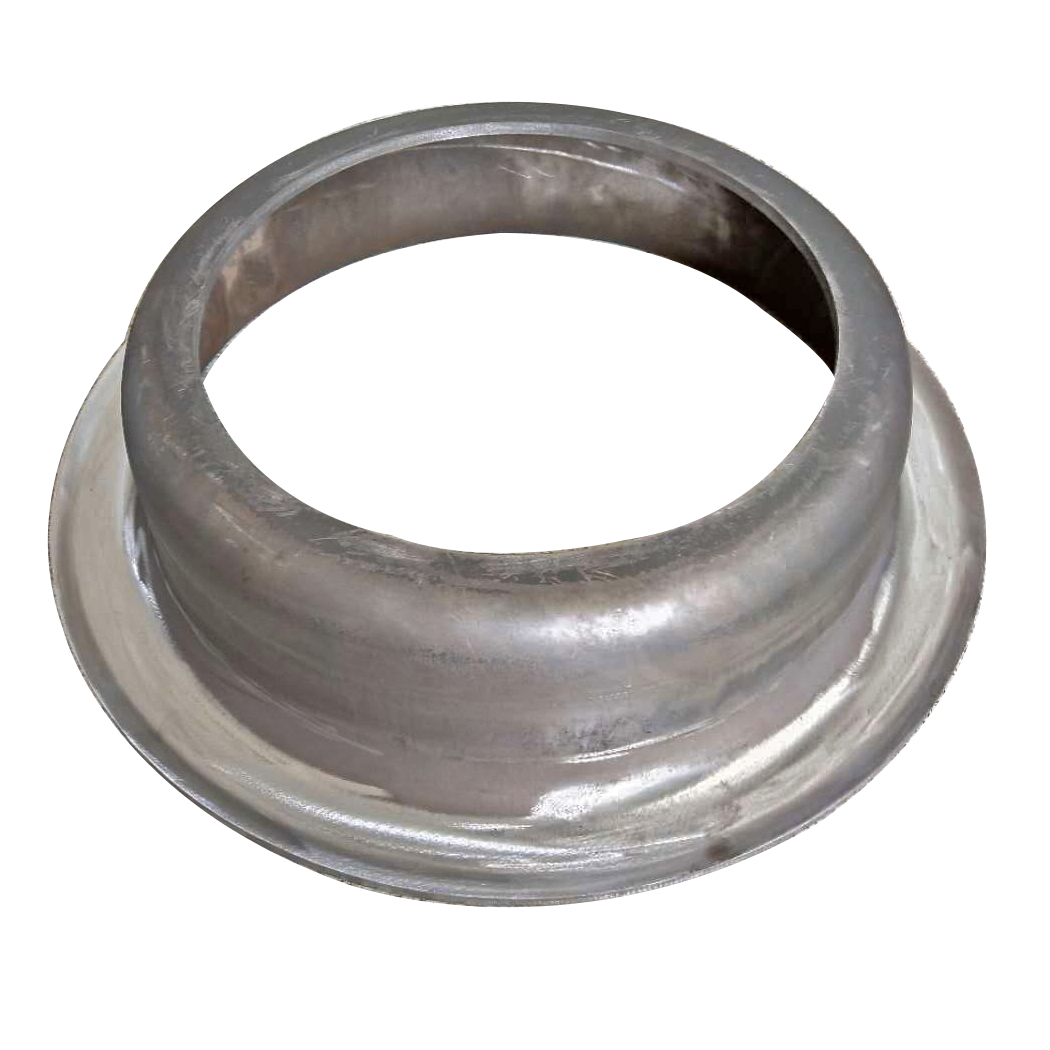
The process of cement casting begins with choosing the right kind of cement for the project at hand. There are two primary types used for casting Portland cement and specialized epoxy cement mixtures. Portland cement is renowned for its durability and is often the choice for structural applications such as beams, slabs, and panels. On the other hand, epoxy cement mixtures are prized for their adhesive properties and are increasingly popular in artistic and decorative projects that demand finer details and a smoother finish.
Preparation of the casting mold is the next crucial step. This involves creating a mold that precisely matches the desired final product. Experienced artisans and construction professionals understand that the quality of the mold directly affects the outcome of the cast. Materials for molds range from metal and plastic to silicone rubbers, each chosen based on the complexity of the design and the preferred surface texture. Meticulous mold preparation includes ensuring all joining parts fit tightly to prevent any leakage, a common issue that can lead to a compromised cast.
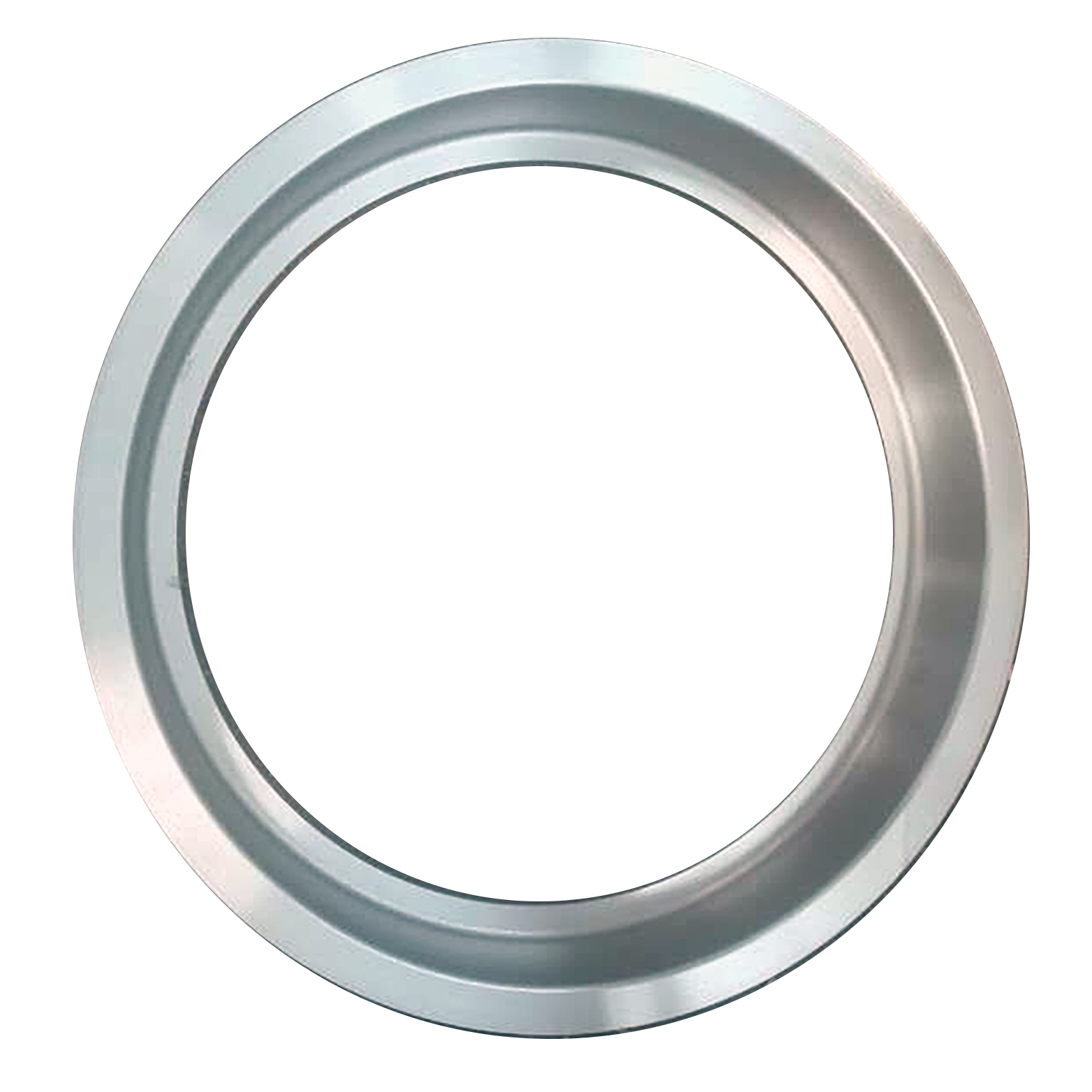
Mixing is an art and science combined, requiring precise measurements and thorough blending to achieve optimal strength and workability. Expert practitioners know that environmental factors such as temperature and humidity can significantly influence the mixture. Hence, they adjust water-to-cement ratios and incorporate admixtures to enhance setting times and strength attributes. An accurate mix ensures not only the longevity of the cast product but also its aesthetic appeal.
cement casting
Pouring the cement mixture into the mold must be conducted with care to avoid introducing air bubbles, which can deteriorate the structural integrity of the cast. Professional techniques involve strategic vibration or tamping to release trapped air and ensure the cement fills all recesses of the mold. This expertise guarantees a homogeneous product, free of weak points, and with a smooth, even surface.
Curing is a critical yet often underestimated aspect of cement casting. Experts in the field emphasize the importance of allowing sufficient curing time, typically several days to weeks, depending on the mixture and environmental conditions. Proper curing not only enhances the strength and durability of the final product but also affects its color and texture. Neglecting this step can lead to cracks, warping, and other structural issues that compromise the product's integrity.
Finally, finishing touches are applied, which can include polishing, painting, or sealing the cast to protect it from environmental contaminants and enhance its aesthetic appeal. Professional finishers bring their experience to bear, selecting compatible products that meet both protective and decorative needs.
In conclusion, cement casting is not just a process but a meticulous journey from conception to completion, requiring expertise and attention to detail. Professionals in the industry, grounded in experience and driven by a commitment to quality, bring authority and trust to their work, ensuring that each cast product not only meets but exceeds expectations. As innovations in materials and techniques continue to evolve, the potential for creativity and efficiency in cement casting expands, promising new possibilities for both commercial and artistic applications.