Sand casting is a cornerstone technique in the world of metalworking, offering both versatility and historical depth. It is widely employed in various industries, from automotive manufacturing to artistic sculpture. This intricate process boasts a unique combination of experience, expertise, authoritativeness, and trustworthiness, making it an invaluable methodology for creating a vast array of metal components.
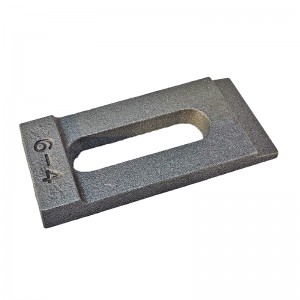
The sand casting process begins with the creation of a mold.
This involves compacting sand around a pattern, which is the exact replica of the item to be produced. Sand is favored as a mold material due to its affordability, availability, and heat resistance. Throughout the centuries, artisans and craftsmen have honed their techniques to perfect the consistency and composition of the sand mixture, ensuring an optimal mold.
Throughout history, sand casting has developed a rich repository of expertise. Mastery over this technique requires knowledge of various sand compositions, binding agents, and the nuances of mold creation. An experienced cast maker understands how to mitigate common defects such as porosity, shrinkage, and surface imperfections, which can compromise the structural integrity of the final product. The precision with which these professionals operate is a testament to the craft’s sophistication and the level of expertise required to produce high-quality results.
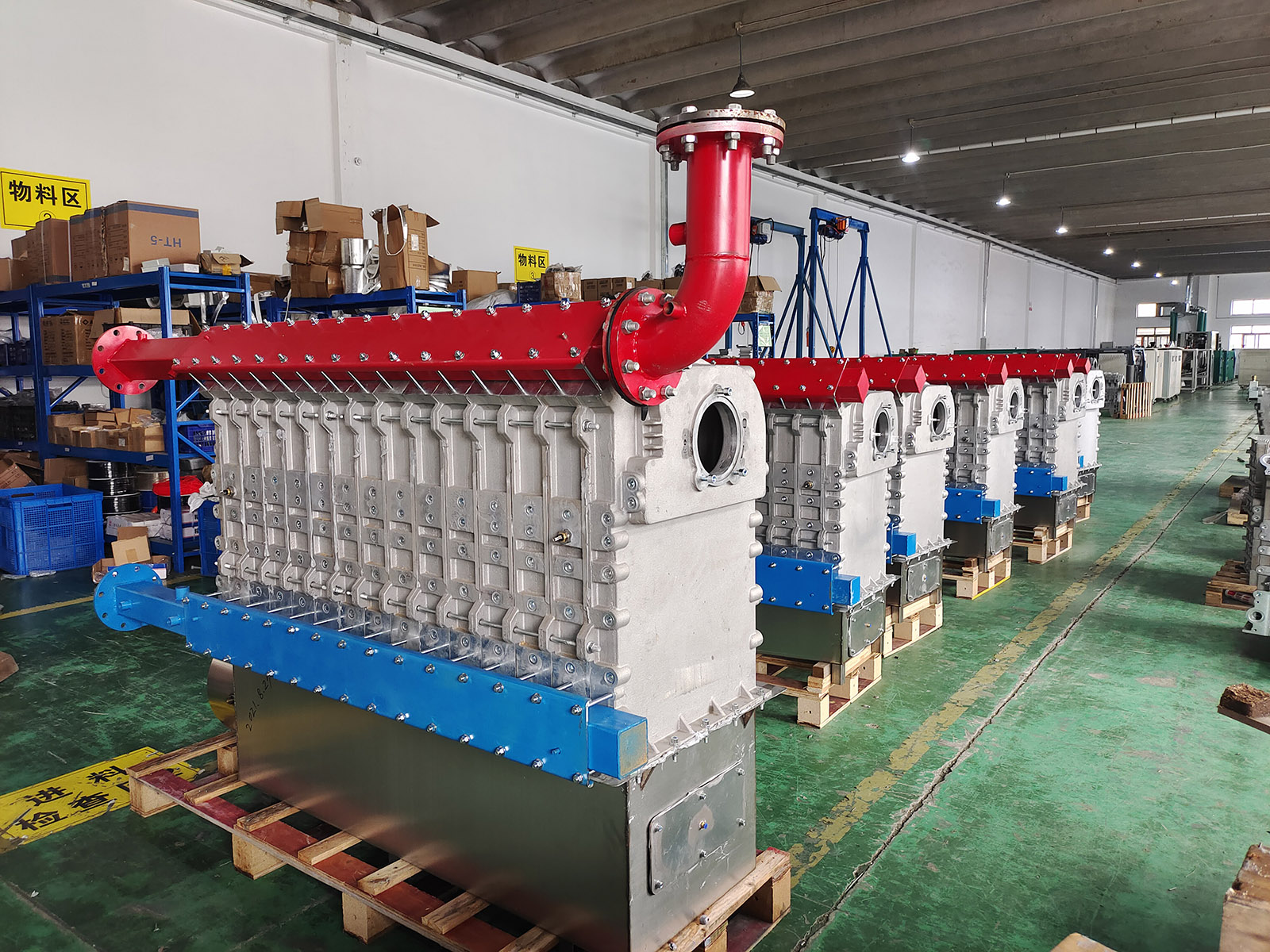
The process of pouring molten metal into the meticulously prepared sand mold is a delicate and authoritative act. Temperature control is paramount; too hot, and the metal may compromise the mold, too cold, and it may solidify prematurely, resulting in incomplete casting. This step is guided by an authoritative understanding of metallurgy and material science, where metallurgists meticulously select the appropriate alloy suited to the product’s functional requirements and operational environment.
sand cast
Furthermore, the efficiency and cost-effectiveness of sand casting make it an authoritative choice among manufacturing methods. With the capability to produce complex shapes and sizes with minimal machinery, it remains a preferred technique for prototyping and small to medium-sized production runs, where investment in expensive die-casting molds is impractical.
Trustworthiness in sand cast products is cemented through rigorous quality control measures. Each casting undergoes thorough inspection, often utilizing modern non-destructive testing (NDT) methods such as X-ray and ultrasonic testing, to ensure compliance with strict industry standards. The reliability of sand casting is particularly evident in critical applications within the aerospace, automotive, and construction sectors, where even the slightest material defect could lead to catastrophic failures.
The alignment of sand casting with cutting-edge technologies demonstrates a blend of tradition and innovation. The integration of computer-aided design (CAD) and computer-aided manufacturing (CAM) into the casting process enhances accuracy and repeatability. Simulation software allows for the prediction and optimization of mold filling and solidification, reducing trial and error and boosting first-time success rates.
In summation, sand casting stands as a testament to the enduring marriage of art and science. It captures the essence of time-honored practices refined by modern advancements. This method upholds a reputation built on decades of trust, driven by expert knowledge and authoritative execution, embodying the true spirit of craftsmanship in the world of metalworking. The power and potential of sand cast products continue to inspire confidence and foster innovation in manufacturing, proving that even the time-honored techniques still reign supreme in an increasingly modernized world.