Ductile iron pipes have long been an essential component in various infrastructure projects, thanks to their remarkable properties of strength, durability, and cost-effectiveness. Central to the manufacturing process of these pipes is the mold bottom ring, a critical part that significantly influences the overall quality and performance of the final product. Here, we delve into the intricacies and the indispensable role that ductile iron pipe mold bottom rings play in the production process, drawing from real-world experience, professional expertise, authoritative insights, and a foundation of trustworthiness.
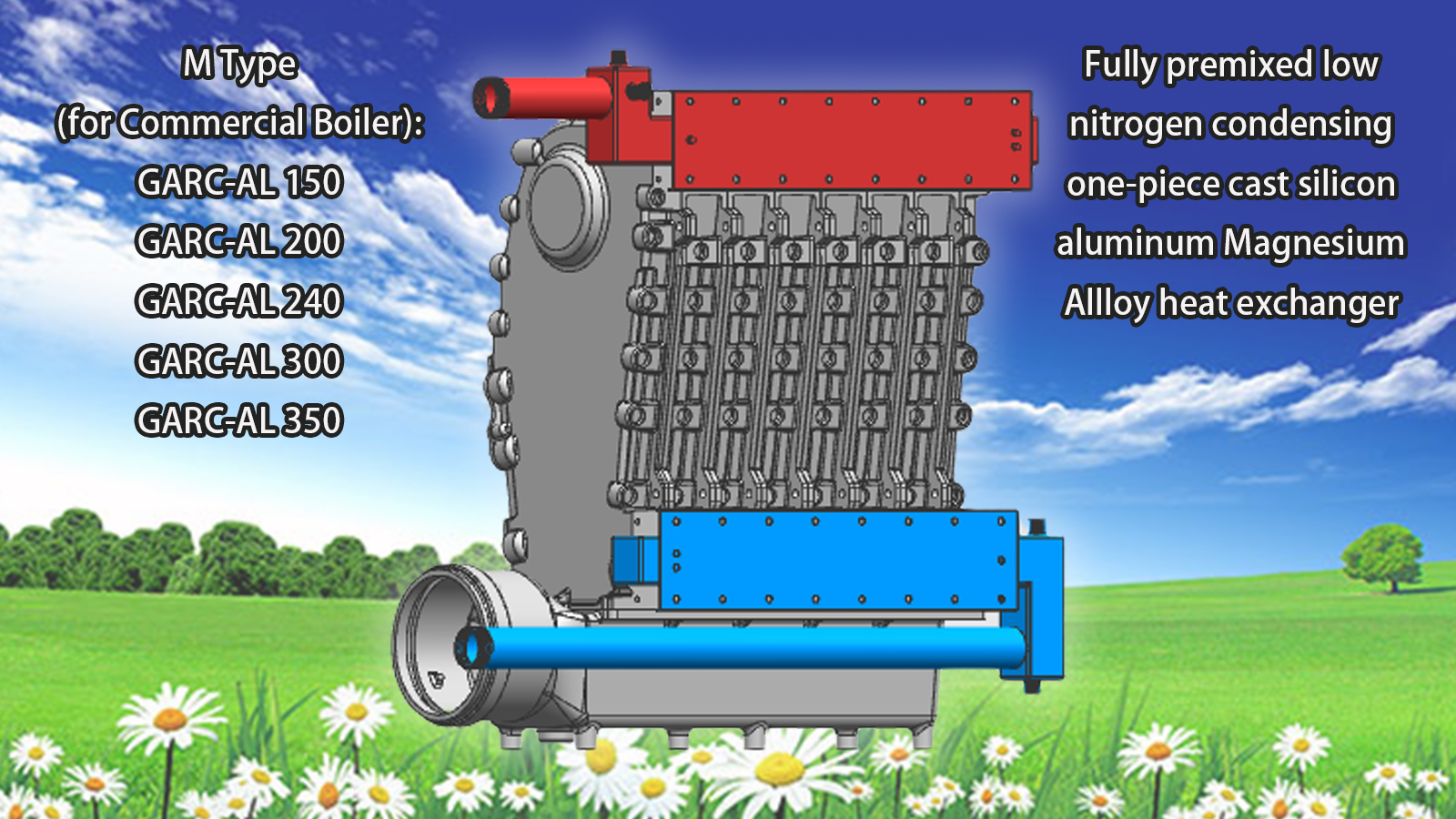
The mold bottom ring in ductile iron pipe production serves as the foundational support and initial shaping component of the pipe's mold assembly. It is where the molten iron initially comes into contact, consequently dictating the uniformity, wall thickness, and surface finish of the pipe. This element must withstand high temperatures and pressures while maintaining structural integrity to produce consistent and high-quality results.
From an experiential standpoint, operators and manufacturers consistently report that selecting the right material composition and design for the mold bottom ring is crucial. The preferred materials often include nickel or chromium-enhanced alloys, which offer superior resistance to thermal fatigue and wear. A well-crafted mold bottom ring minimizes defects such as blowholes, inclusions, and uneven wall thickness, which are critical concerns that can severely compromise the pipe's performance and longevity.
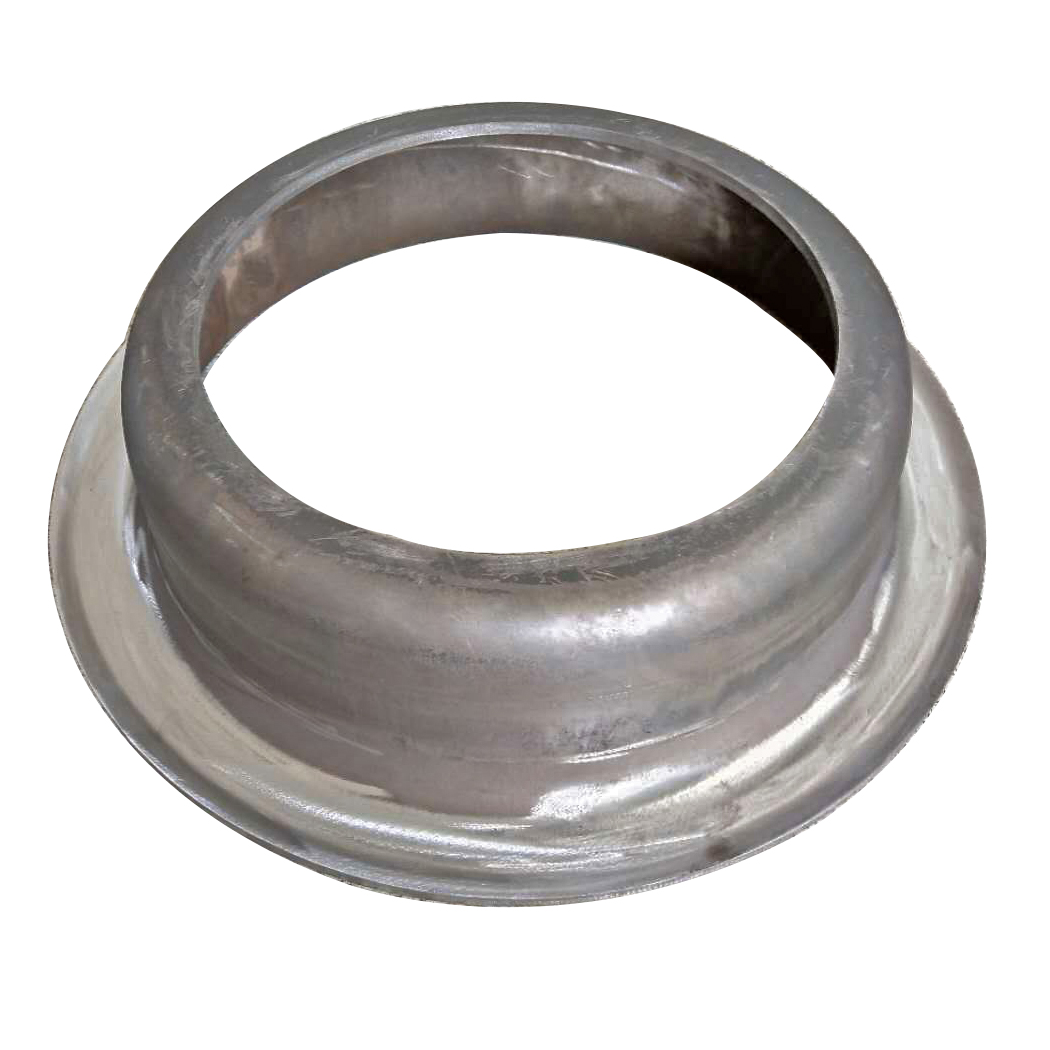
From an expertise-driven perspective, it is essential to understand the precise engineering that goes into designing the bottom ring for mold use. This includes considerations such as thermal expansion properties, wear resistance, and the ability to quickly and evenly cool down to prevent thermal cracking. Engineers often utilize advanced simulation techniques to model how different designs might perform under typical operational conditions, optimizing the bottom ring's design before it even enters the production line.
ductile iron pipe mold bottom ring
To maintain authority in manufacturing high-quality ductile iron pipes, companies must emphasize rigorous testing and quality control procedures for their mold bottom rings. Inspection protocols often involve nondestructive testing methods such as ultrasonic, magnetic particle, and dye penetrant testing to ensure the integrity and durability of the ring. By establishing such robust procedures, manufacturers can uphold their reputation and deliver pipes that meet the stringent standards required for infrastructure projects worldwide.
Finally,
the reliability and trustworthiness in deploying well-engineered mold bottom rings cannot be overstated. A trusted supplier not only provides these components but also offers technical support and advisory services. This partnership ensures that the evolving needs of production are met with cutting-edge technology and solutions, fostering a collaborative environment where innovations lead to enhanced efficiency and product quality.
Choosing the right ductile iron pipe mold bottom ring is a critical factor in the success of pipe manufacturing processes. Manufacturers who invest in high-quality bottom ring designs and materials can improve their production efficiency, reduce waste, and deliver superior products. By staying informed through continuous research and development, and partnering with experienced suppliers and engineers, companies can confidently tackle the challenges of modern infrastructure demands, solidifying their position as industry leaders in ductile iron pipe production.