Precision casting, also known as investment casting or lost-wax casting, is a sophisticated industrial process employed to fabricate intricate metal parts with exceptional accuracy and surface finish. This technique has been a cornerstone in industries where precision and reliability are paramount, such as aerospace, automotive, medical, and military sectors. The authenticity of precision casting is derived from its ability to meet the most stringent specifications and its adaptability to an extensive range of metals and alloys.
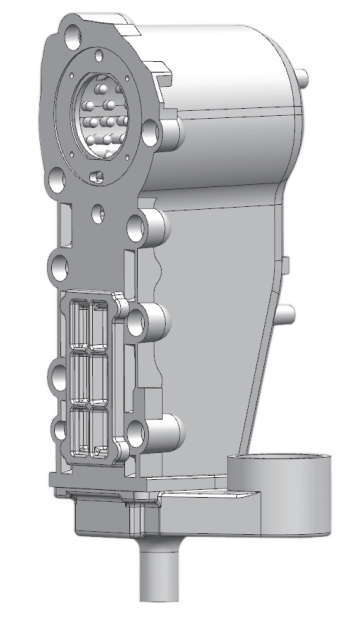
From an experiential perspective, the process begins with the creation of a wax model, which forms the centerpiece of the entire casting procedure. The wax model accurately replicates the final desired part, ensuring that even the most minute details are captured. Once the model is completed, it’s encased in a ceramic shell through a repeated dipping process. This shell is hardened, and the wax is then melted away, leaving a precise cavity for the metal casting.
The expertise involved in precision casting is unparalleled. Engineers and artisans work in tandem, employing their cumulative knowledge to meticulously manage each phase of the process. The ability to produce complex parts in a single piece, which would otherwise require multiple components and assembly, positions precision casting as a preferred method in manufacturing environments requiring high performance and durability. Moreover, the economic advantages derived from reducing waste material, as precise quantities of alloy are utilized, cannot be overstated.
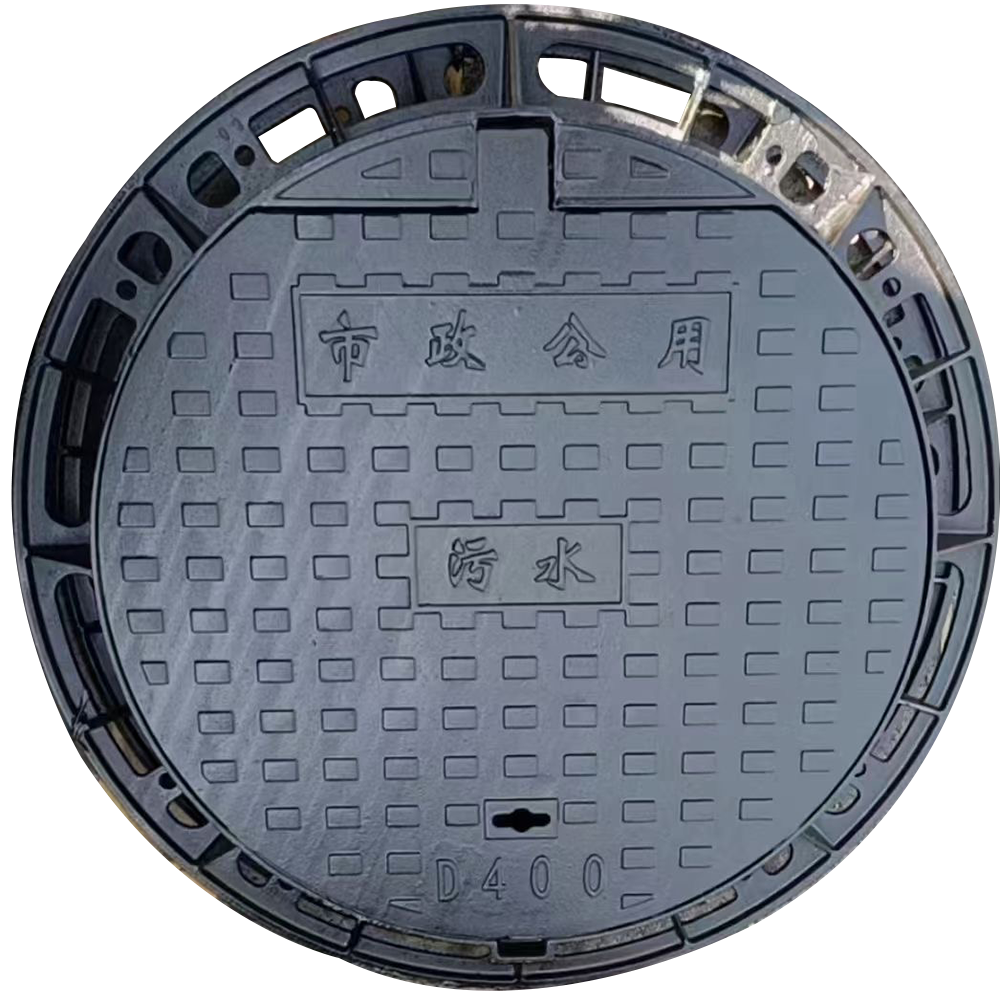
Precision casting boasts significant authoritative advantages in its domain. Given the industry's demand for parts that push the boundaries of material stress and environmental resilience, precision casting ensures components can endure such constraints with minimal wear and tear. In the aerospace sector, for instance, the reliability of these components is non-negotiable, prompting manufacturers to heavily invest in precision casting to produce turbine blades and other critical parts with outstanding repeatability and performance metrics.
precision casting
The credibility of precision casting is further fortified by rigorous quality control protocols. Each phase of the process is subject to careful inspection, often utilizing advanced techniques such as X-ray and 3D scanning to ensure structural integrity and adherence to design specifications. These inspections uphold the trustworthiness of precision casting parts, providing assurances that they meet or exceed industry standards.
What sets precision casting apart in today’s manufacturing landscape is its remarkable adaptability to new technologies and demands. The integration of CAD and CAM systems has revolutionized the design phase, enabling more complex and innovative shapes to be produced with unprecedented efficiency. Furthermore, innovations like rapid prototyping have shortened lead times and expanded the possibilities of design iterations.
As the world moves towards more sustainable manufacturing processes, precision casting stands out as an environmentally favorable option. The process’s inherent waste-reduction capabilities, coupled with its precision efficiency, underscore its role in the sustainable manufacturing landscape. With continued advancements and a commitment to high-quality outputs, precision casting remains at the forefront of modern manufacturing solutions.
To leverage the full potential of precision casting, it is essential to collaborate with manufacturers who embody experience, expertise, authoritativeness, and trustworthiness. By doing so, industries can harness the full suite of benefits that precision casting offers, ensuring that their components are not only of superior quality but also aligned with the technological and economic demands of the future.