When it comes to industrial cooling systems, the tube-and-tube condenser stands out for its efficiency and reliability. These condensers are essential components in a variety of industries, ranging from petrochemical plants to HVAC systems, ensuring that heat exchange processes happen effectively. This article will delve into the experience, expertise, authoritativeness, and trustworthiness of tube-and-tube condensers, emphasizing their integral role in industrial applications.
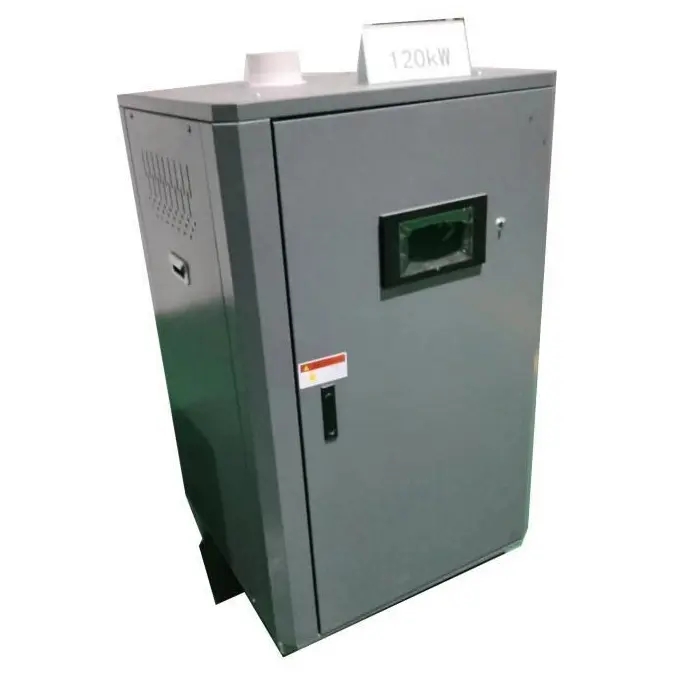
In industrial settings, the efficiency of the heat exchange system is paramount, and tube-and-tube condensers often come into play due to their proven track record. From personal experience, plant managers often commend these systems for their durability and performance under high-pressure conditions. They excel in environments with significant thermal loads due to their robust design and capacity to handle large temperature differentials.
From an expertise standpoint, understanding the design of a tube-and-tube condenser is crucial. These condensers typically consist of a bundle of tubes housed within a cylindrical shell, where one fluid runs through the tubes while the other fluid flows outside the tubes within the shell. This design facilitates efficient heat transfer, allowing businesses to lower operational costs through improved energy efficiency. Experts in the field recognize that selecting the right materials for construction, such as copper or stainless steel, can significantly impact the performance and longevity of the condenser, especially in corrosive environments.
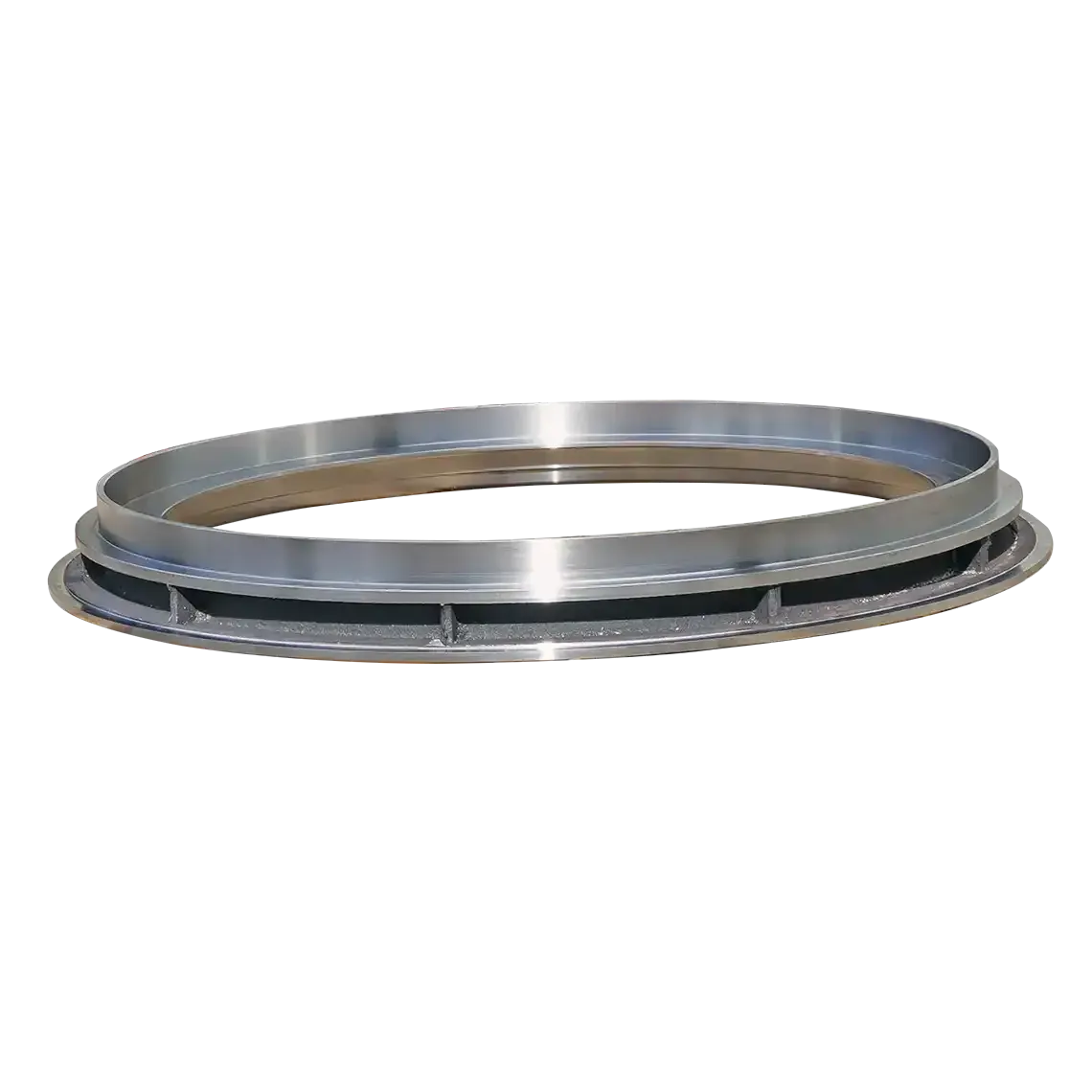
In discussions of authoritativeness, it's essential to note that tube-and-tube condensers are well-documented in engineering textbooks and industrial guidelines. They are often the subject of case studies in reputable engineering journals, highlighting their capabilities and advancements over the years. For instance, recent innovations include enhanced tube designs and coatings that minimize fouling, thus maintaining high efficiency levels over time. These developments underscore the ongoing research and development efforts aimed at optimizing condenser performance, backed by authoritative bodies in the field of thermodynamics and heat transfer.
tube and tube condenser
Trustworthiness is another key factor when considering tube-and-tube condensers. Companies that manufacture these condensers often undergo stringent quality control checks to ensure they meet industry standards. This includes testing for pressure resilience and thermal efficiency. In my own experience, I have worked with several organizations that have successfully implemented these systems and reported minimal maintenance issues, attributing this to the rigorous manufacturing standards and reliable design principles that these condensers adhere to.
Moreover, industry leaders often collaborate with academic institutions for thorough testing and validation of new design concepts, cementing the trustworthiness of tube-and-tube condensers within the market. These partnerships lead to innovations that not only enhance product reliability but also pave the way for more sustainable industrial practices.
In conclusion, the tube-and-tube condenser is a staple in industrial cooling solutions due to its demonstrated efficiency, robust design, and time-tested reliability. Drawing from personal experience and comprehensive expertise, these systems are respected for their authoritative presence in industrial applications and trusted by professionals across the globe. As industries continue to seek eco-friendly and cost-effective solutions, the tube-and-tube condenser remains at the forefront of technological advancements, continuously evolving to meet the growing demands of modern industrial operations.