Direct contact heat exchangers play a crucial role in numerous industries due to their efficiency and unique design. These systems facilitate the direct transfer of heat between two fluid streams without a separating wall. Unlike indirect heat exchangers, direct contact variants enable more efficient transfer of thermal energy, significantly improving system performance while reducing costs. Below, we explore examples of direct contact heat exchangers, emphasizing their application, functionality, and benefits, particularly in industrial processes.
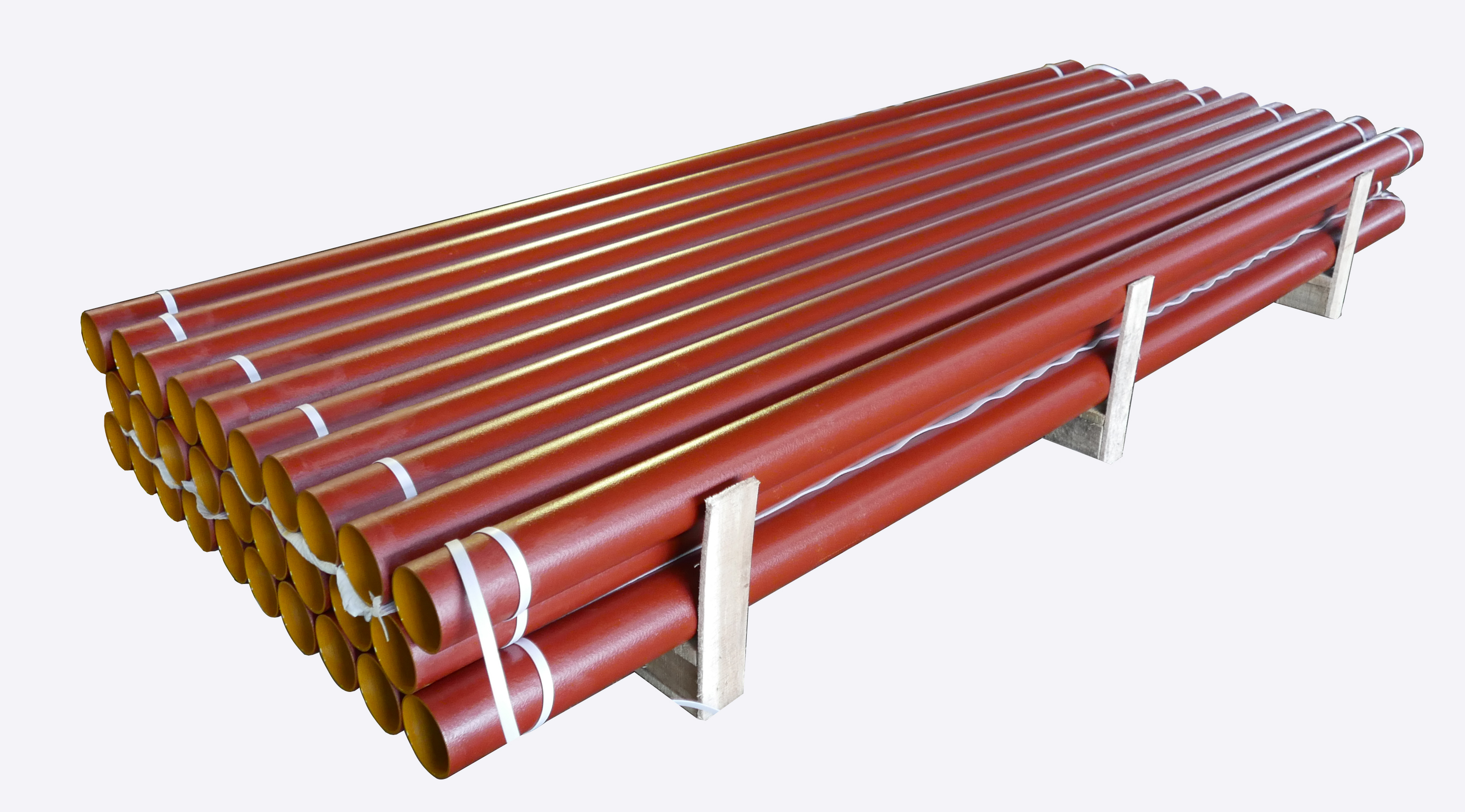
A quintessential example of a direct contact heat exchanger is the cooling tower, commonly used in power plants, refineries, and chemical manufacturing facilities. In a cooling tower, warm water from industrial processes is sprayed over a fill material, increasing the surface area for evaporation. At the same time, air is drawn or forced through the tower, allowing the water to cool as the heat is directly transferred to the air, which then vented to the atmosphere. This efficient cooling process helps maintain optimal operating temperatures for machinery, reducing the likelihood of equipment overheating and extending operational lifespan.
Another notable example is the gas scrubber system employed in industries for air pollution control. Gas scrubbers work by bringing a hot gas stream into direct contact with a liquid, typically an alkaline solution. As they mix, the heat and particulates in the gas are absorbed by the liquid. This process not only cools the gas but also removes harmful contaminants, demonstrating the dual functionality of direct heat exchangers in both temperature control and environmental management. Their successful application in industrial emission control supports compliance with environmental regulations and reinforces corporate responsibility.
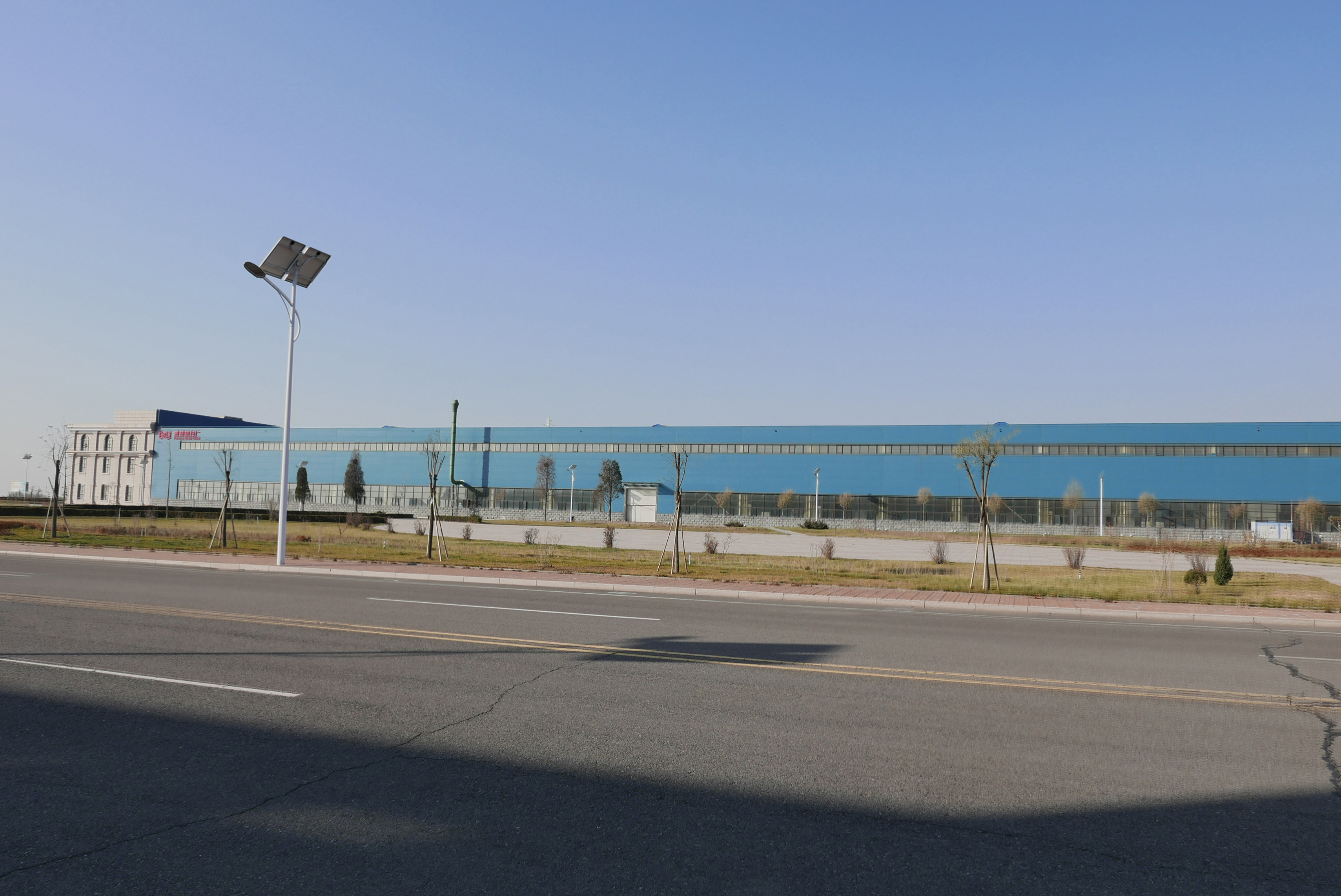
In addition to cooling towers and gas scrubbers, direct contact heat exchangers find application in geothermal power plants. In these settings, a direct contact condenser is used to condense steam from geothermal wells. Here, the steam is injected directly into a pool of cooling water, whereby the heat is transferred, leading to steam condensation. This method allows for efficient heat exchange and minimizes energy loss, essential for maximizing power generation and operational efficiency. The utilization of geothermal resources underscores the eco-friendly potential of direct contact systems in sustainable energy production.
direct contact heat exchanger example
Moreover, desalination plants often incorporate direct contact heat exchangers within multi-effect distillation (MED) processes. Direct contact between steam and seawater accelerates the evaporation rate, thus facilitating efficient desalination. This approach reduces energy consumption compared to indirect systems and contributes to addressing global water scarcity challenges.
The advantages of direct contact heat exchangers over traditional models are evident. These systems offer simplicity in design and operation, cost-effectiveness, and enhanced energy efficiency. They eliminate the need for complex heat transfer surfaces, reducing maintenance requirements and the risk of fouling. Furthermore, direct contact heat exchangers can handle large temperature differentials and large flow rates, making them suitable for diverse industrial applications.
In conclusion, the direct contact heat exchanger exemplifies an innovation in industrial thermal management with its broad applicability and operational advantages. From cooling towers and gas scrubbers to geothermal power plants and desalination units, these systems deliver efficient heat transfer and contribute to both economic and environmental goals across sectors. As industries strive for greater sustainability and cost-effectiveness, the role of direct contact heat exchangers will continue to grow, supported by ongoing research and development aimed at enhancing their performance and expanding their applications. These developments promise a future where energy efficiency and environmental stewardship go hand in hand, driven by the adoption of advanced thermal management technologies.