Heat exchangers play a pivotal role in various industrial applications, offering vital functions in processes that require thermal energy transfer. Their classification is key to selecting the appropriate type for specific operational needs, ensuring efficiency, cost-effectiveness, and reliability.
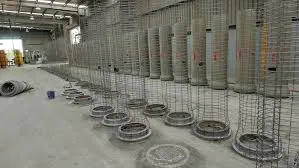
Heat exchangers can be categorized primarily by their design and operational principles. The most common classifications include shell and tube, plate, air-cooled,
and regenerative heat exchangers. Each type exhibits unique characteristics that make them well-suited for different applications across industries such as chemical processing, HVAC, power generation, and more.
Shell and tube heat exchangers are among the oldest and most prevalent types, known for their robustness and versatility. They consist of numerous tubes enclosed within a cylindrical shell, allowing one fluid to flow through the tubes while another fluid flows over them within the shell. This design is ideal for handling high-pressure applications and accommodating significant temperature differentials. Industries favor shell and tube heat exchangers due to their durability and the ease of maintenance they offer, making them a trusted choice for petrochemical and refinery processes.
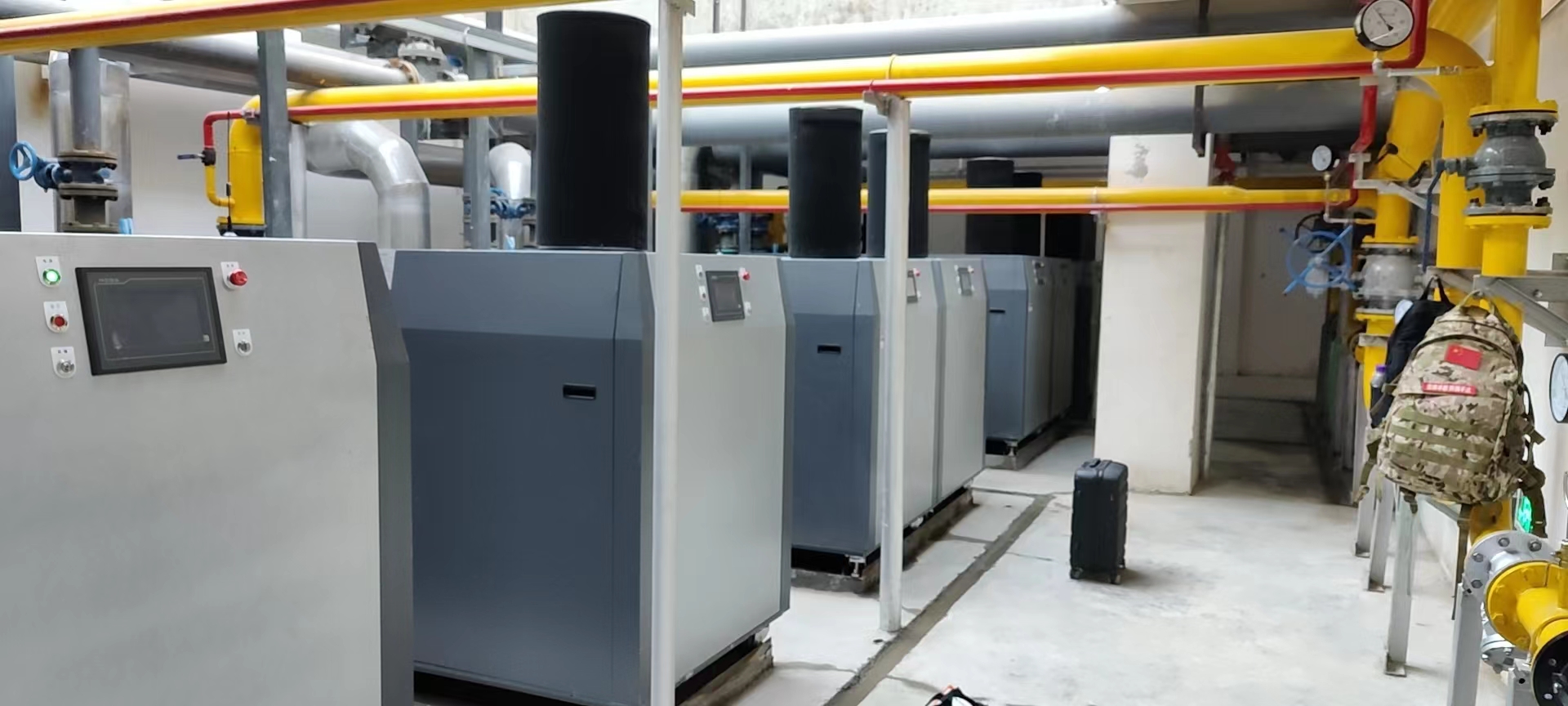
Plate heat exchangers, on the other hand, are synonymous with efficiency. Comprising a series of thin, slightly separated plates that facilitate heat transfer through a large surface area, these exchangers provide excellent thermal performance. They are particularly favored in applications where space is at a premium because of their compact size. Commonly used in food processing and beverage industries, plate heat exchangers excel in transferring heat between fluids with varying viscosities all while ensuring minimal cross-contamination–a critical feature in these sectors.
Air-cooled heat exchangers offer a distinct advantage by eliminating the need for water as a cooling medium, which can be beneficial in areas where water supply poses a concern. These exchangers function by passing air over a set of coils or tubes that carry the hot process fluid. Their eco-friendly nature positions air-cooled heat exchangers as ideal for environments striving towards sustainable practices, such as in refinery cooling processes or power plants.
classification of heat exchanger
Regenerative heat exchangers capitalize on heat recovery, thus enhancing overall system efficiency. These exchangers temporarily store heat from exhaust gases or fluids, transferring it back to the system, often reducing energy consumption significantly. Implemented extensively in gas turbine applications, regenerative heat exchangers play an essential role in industries looking to optimize energy use and reduce operational costs.
Selecting the right heat exchanger type necessitates a keen understanding of the specific application requirements, including factors such as temperature ranges, pressure limits, and fluid compatibility. Expert consultation with manufacturers and engineers can provide valuable insights into the most suitable choices, emphasizing that real experience coupled with technical proficiency is indispensable.
Furthermore, advances in materials and technology continue to redefine heat exchanger capabilities. Innovations such as the utilization of corrosion-resistant alloys and enhanced surface treatments contribute to longer life spans and improved efficiency. These developments, driven by a deeper understanding of thermodynamics and materials science, bolster the authority of experts in recommending and implementing heat exchangers tailored to advanced industrial needs.
Incorporating trustworthiness within the industry relies heavily on adherence to established standards and certifications. Ensuring that heat exchangers comply with international safety and efficiency standards not only safeguards operations but also elevates the stature of manufacturers and suppliers as reliable entities in the field.
In conclusion, the classification of heat exchangers forms the foundation of optimizing processes across various sectors. By aligning the choice of heat exchanger with specific operational dynamics and leveraging cutting-edge developments, industries can achieve significant enhancements in efficiency, sustainability, and performance. This interplay between experience, expertise, authority, and trust underscores the critical role that informed decision-making plays in the selection and application of heat exchangers.