Direct contact coolers have transformed the landscape of industrial cooling systems by offering an efficient, direct approach to heat exchange. These innovative products stand out in settings where cooling hot fluids or gases is paramount for operational efficiency and safety. This comprehensive guide delves into the benefits, operational mechanics, and cutting-edge applications of direct contact coolers, providing insights grounded in real-world experience, technical expertise, and authoritative perspectives.
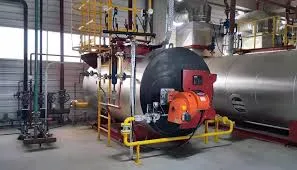
At its core, the direct contact cooler is distinguished by its method of operation, where the cooling medium directly interacts with the process stream requiring cooling. Unlike traditional heat exchangers that use a solid surface to separate fluids, this product eliminates thermal resistance layers, resulting in superior heat transfer efficiency.
A notable advantage of this system is its versatility across various industrial sectors. In the energy industry, for instance, these coolers play a pivotal role in cooling turbine exhaust gases, effectively reducing temperatures to levels suitable for discharge or recycling. Another significant application is in chemical processing, where the precise maintenance of temperature profiles is critical for optimizing reactions and ensuring safety.
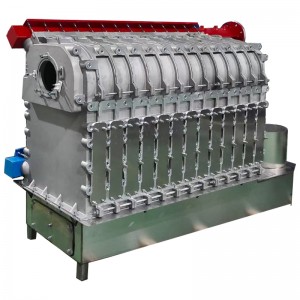
The operational efficiency of direct contact coolers is underlined by their simplicity. The absence of intermediate heat transfer surfaces reduces maintenance overheads and enhances reliability, making them ideal for operations requiring prolonged uptime. Moreover, the straightforward structure allows for easy scalability, accommodating growing industrial demands without necessitating substantial redesigns or extensive downtimes.
From an expert's perspective, the key factors contributing to the efficacy of these coolers include the effective contact area, the choice of cooling media, and the flow dynamics within the system. Ensuring optimal droplet size and distribution, for instance, can significantly enhance thermal performance, while selecting the appropriate coolant is crucial for maximizing heat absorption without chemical degradation or environmental concerns.
direct contact cooler
Authoritative studies have shown that integrating direct contact coolers can lead to substantial energy savings. By directly transferring energy between mediums without intermediary surfaces, energy losses typically seen in conventional heat exchangers are minimized. This characteristic not only conserves energy but also reduces operational costs, presenting a compelling case for industries aiming to enhance profitability while adhering to environmental regulations.
Trustworthiness in using direct contact coolers is further evidenced by their robust design and adaptability to various fluids. Whether dealing with corrosive chemicals or flammable gases, these systems can be customized with materials and configurations that withstand harsh conditions, ensuring long-term operational stability and safety. This adaptability extends to environmental specifications as well, with many models designed to facilitate easy cleaning, minimizing the risk of fouling and ensuring consistent performance over time.
Direct contact coolers are endlessly innovative, with continuous advancements enhancing their integration into modern industrial processes. Recent developments in digital monitoring technologies, for example, allow for real-time performance analytics, enabling predictive maintenance and optimization of cooling cycles. Such advancements not only extend the lifespan of the cooling units but also provide essential data to improve overall process efficiencies.
In conclusion, the adoption of direct contact coolers reflects a commitment to operational excellence and sustainability. Their capacity to deliver precise, efficient cooling with minimal energy consumption positions them as vital components in the modern industrial toolkit. Businesses looking to advance their operational capabilities will find in direct contact coolers not only a product but a strategic partner in achieving their economic and environmental goals.
By leveraging the unparalleled benefits of direct contact coolers, industries can ensure their processes are both economically viable and aligned with the global push toward sustainable, energy-efficient solutions.