Heat exchangers play a crucial role in refinery operations, acting as the backbone of thermal management systems. In the intricate world of refineries, these devices ensure that temperatures remain optimal, thereby maximizing efficiency and safety. Unlike other sectors, refineries require highly specialized heat exchangers due to the complex and hazardous nature of petroleum products, which are processed through various stages including distillation, refining, and chemical synthesis.
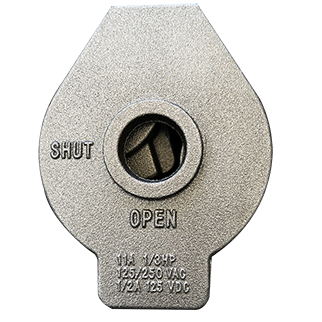
Over the years, technological advancements have led to the development of more sophisticated heat exchangers, tailored to handle extreme conditions and diverse fluids. In terms of design, heat exchangers in refineries range from shell and tube types to plate exchangers, each offering distinct advantages depending on the specific application.
1. Experience in Deployment and Maintenance
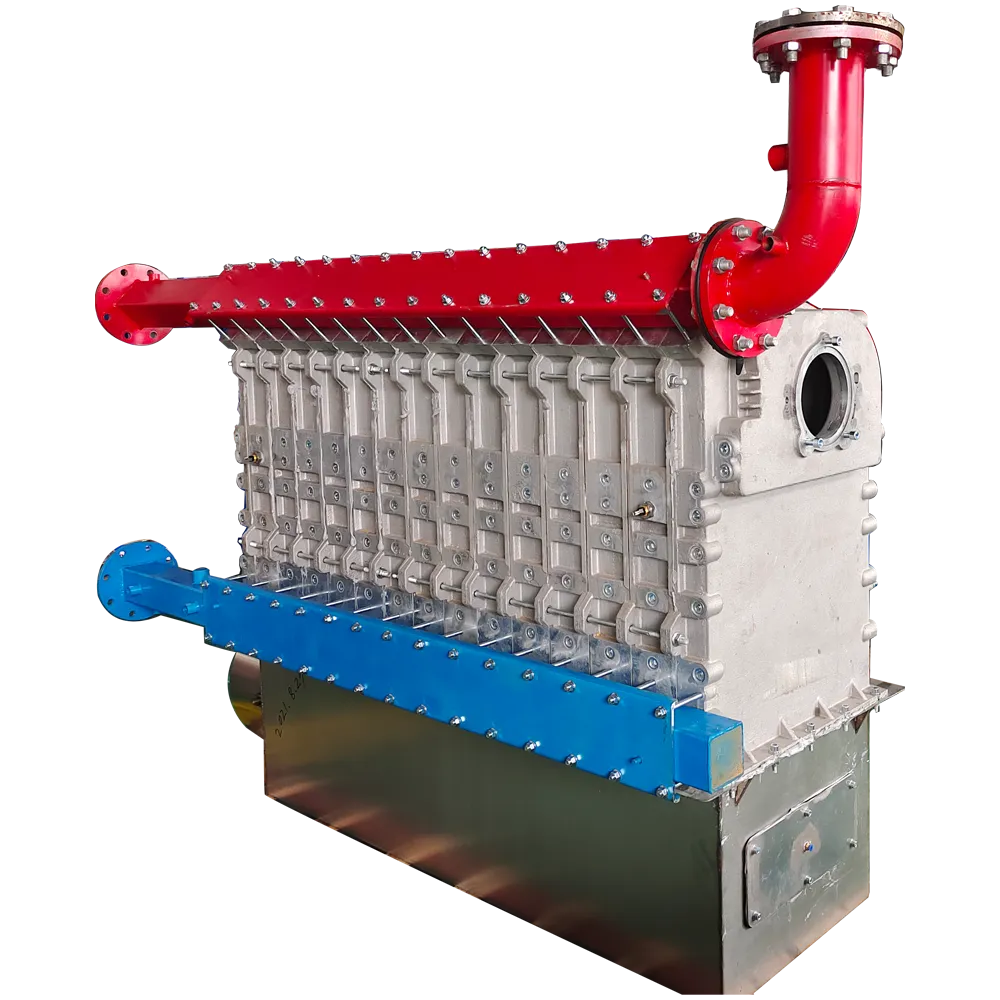
Refinery engineers often grapple with issues like corrosion, fouling, and scaling, which can impede the heat exchanger's performance. Drawing from field experience, operators emphasize the importance of regular maintenance schedules and the use of high-grade materials that resist wear and tear. Modern sensors and IoT integrations allow for real-time monitoring of system health, predicting maintenance needs before they become critical, thereby reducing downtime and extending the life of the equipment.
2. Expertise in Design and Application
The key to selecting an effective heat exchanger lies in understanding the intricacies of the refining process. Certain stages demand rapid heat transfer, while others require precise temperature control. For high-temperature processes, materials such as Inconel and Hastelloy, known for their excellent heat resistance and durability, are often utilized. Moreover, the selection of the heat exchanger should consider factors such as thermal efficiency, pressure drop, and compactness.
heat exchanger in refinery
3. Authoritativeness through Proven Performance
Leading manufacturers stress-test their designs in virtual and physical environments, demonstrating their reliability under simulated refinery conditions. By leveraging CFD (computational fluid dynamics) simulations, engineers can predict how exchangers will perform under extreme conditions, allowing refineries to make informed choices backed by empirical data. Peer-reviewed studies and certifications from reputable industry bodies further cement the authority of these products.
4. Trustworthiness through Compliance and Safety
Refineries adhere to stringent safety and environmental standards. Heat exchangers must be compliant with regulations such as ASME codes, API standards, and ISO certifications. This ensures they not only deliver optimal performance but also maintain the integrity of processes, preventing leaks that could lead to catastrophic incidents. Furthermore, exchangers designed with sustainability in mind help refineries reduce their carbon footprint, aligning operational goals with global environmental mandates.
In conclusion, heat exchangers are not mere auxiliary components in refineries but are critical to the core function and efficiency of the refining process. The combination of practical experience, cutting-edge expertise, authoritative validation, and robust trustworthiness makes them integral to modern refinery operations. As the oil and gas industry evolves, so does the technology around it, placing heat exchangers at the forefront of innovation and efficiency improvements. By investing in tailored, high-quality heat exchangers, refineries can ensure they meet current demands while preparing for future challenges.