Tube and tube heat exchangers, a crucial piece of thermal management equipment, are renowned for their efficiency in transferring heat between two fluids. Having worked in the thermal management industry for over a decade, I've witnessed firsthand how these devices have evolved to meet various industrial demands. With a design engineered for maximum efficiency and durability, tube and tube heat exchangers have become indispensable in fields as varied as chemical processing, power generation, and HVAC systems.
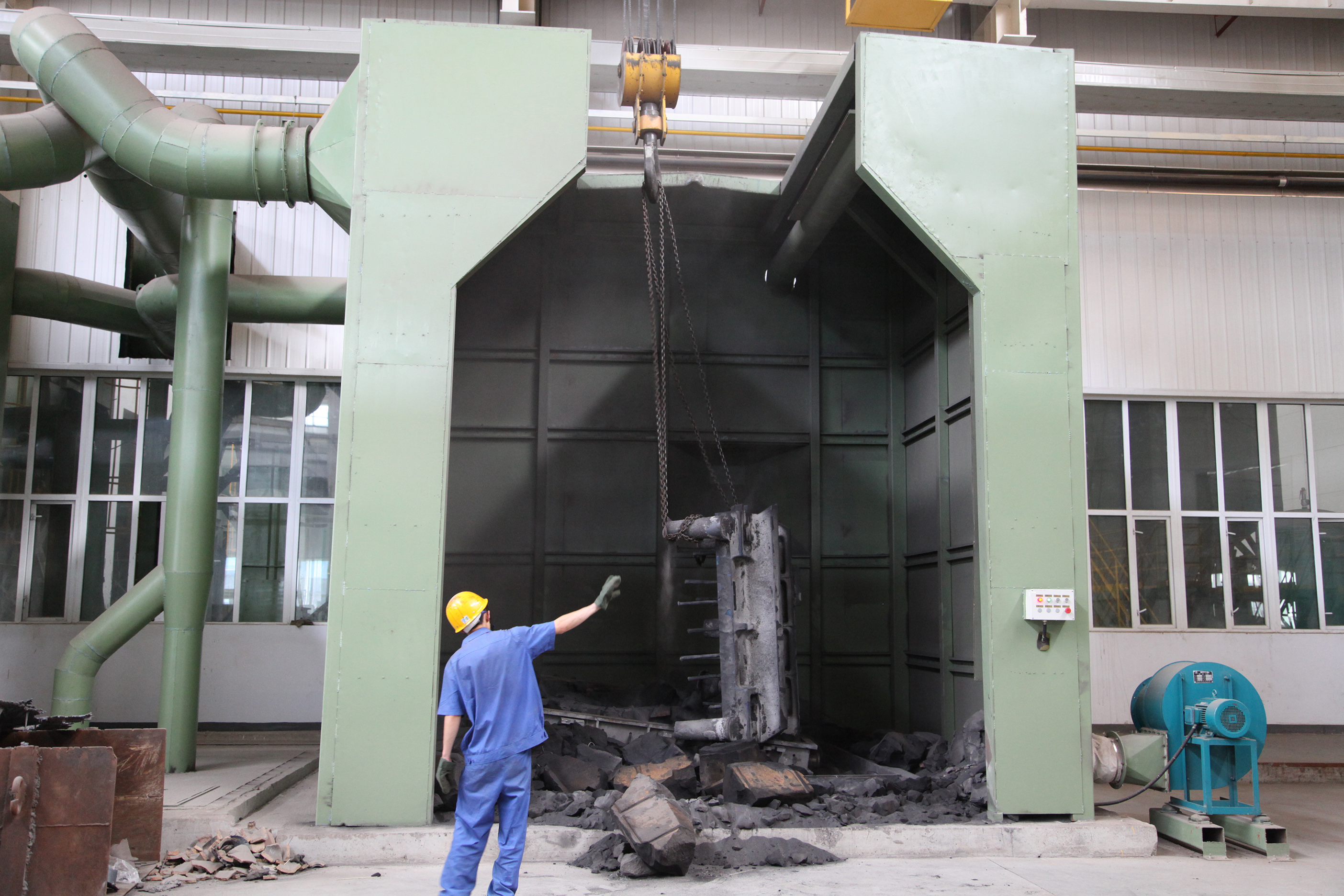
A standout feature of these heat exchangers is their versatility. They are designed to accommodate various fluid types and temperatures, making them suitable for an extensive range of applications. Their construction typically involves a series of tubes—one set carrying the hot fluid and another the cold—allowing for heat exchange where fluids can either be in a parallel or counterflow configuration. This design not only enhances the thermal transfer process but also provides the flexibility needed for different operational needs.
From an expertise perspective, understanding the materials used in tube and tube heat exchangers is paramount. Metals like copper, stainless steel, and titanium are commonly employed due to their exceptional heat conduction properties. Each of these materials has its unique advantages for example, copper offers excellent thermal conductivity and corrosion resistance, whereas titanium is most suitable in saltwater applications due to its outstanding corrosion resistance. Selecting the appropriate material can significantly influence the efficiency and longevity of the heat exchanger.
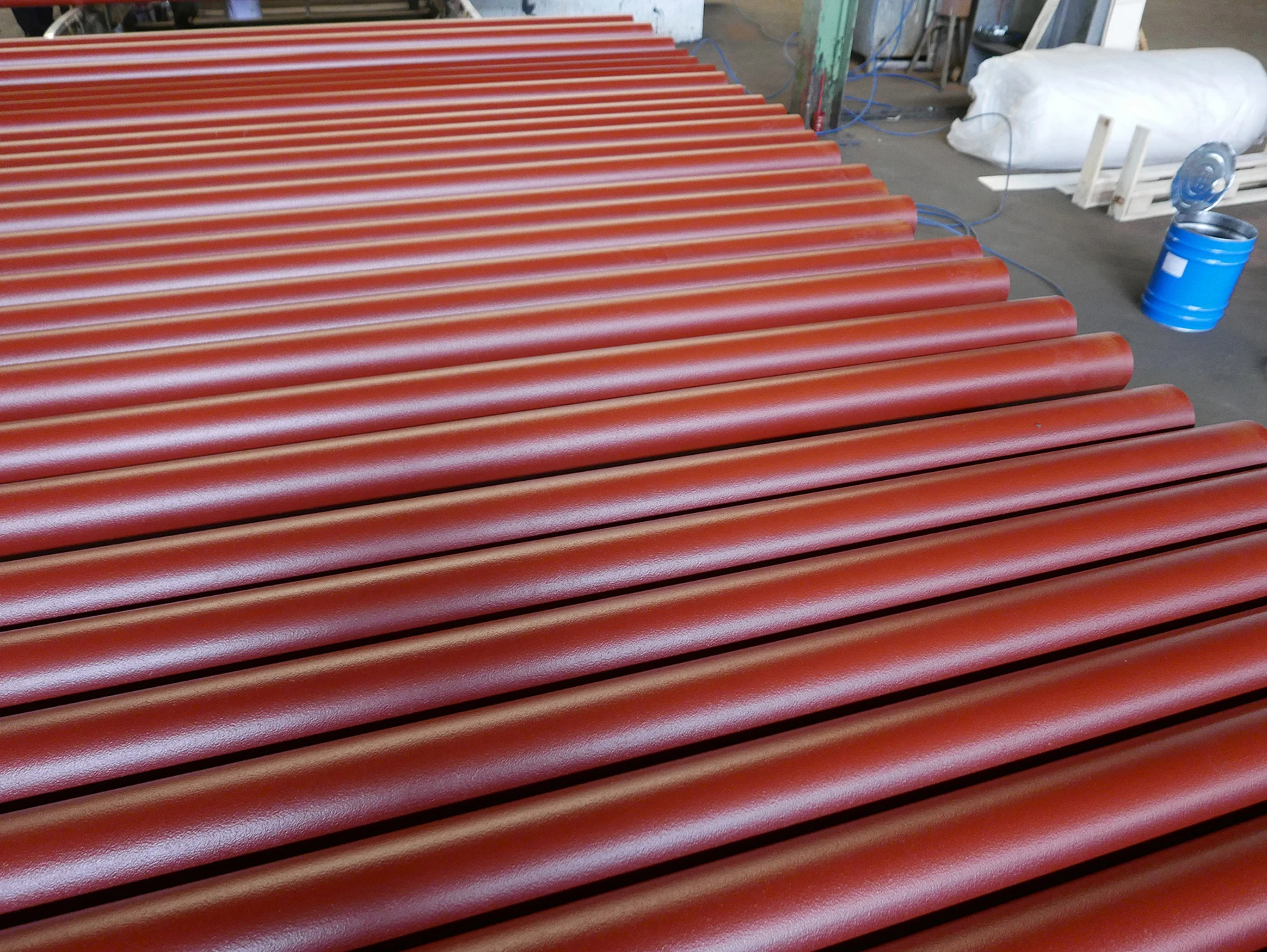
In my career, ensuring that the tube and tube heat exchangers are correctly maintained has always been critical. Routine inspections for leaks, scaling, and corrosion ensures that the exchangers operate at peak efficiency. A common issue that I have encountered is fouling—a buildup of unwanted material on the heat transfer surfaces. Regular cleaning and the use of anti-fouling coatings can mitigate such issues, ensuring the reliability and longevity of the equipment.
tube and tube heat exchanger
The authority of tube and tube heat exchangers also lies in their design innovation. Recent advancements have led to the development of exchanger models with enhanced tube geometries and increased surface areas to maximize heat transfer rates. Computational fluid dynamics (CFD) modeling is often used in the design phase to simulate fluid flow and heat exchange, thereby optimizing the exchanger's performance before it is even built. This proactive approach minimizes energy consumption and operational costs, aligning with the global push towards sustainable industrial practices.
Trust in tube and tube heat exchangers is further bolstered by a robust track record in various industry applications. In power plants, these exchangers are integral for turbine condensers where they efficiently handle immense temperature differences. In the food processing industry, they maintain critical temperature control for pasteurization and sterilization processes. Users can rely on these exchangers not only for efficiency but also for meeting stringent safety and hygiene standards.
In conclusion, my experience in the field attests to the invaluable role of tube and tube heat exchangers. Their blend of versatility, material excellence, innovative design, and proven reliability makes them a cornerstone of modern thermal management systems. For any industrial application requiring precise and efficient heat transfer, tube and tube heat exchangers continue to offer unparalleled performance, backed by a solid foundation of expertise and trustworthiness. As industries grow and challenge existing boundaries, these heat exchangers are poised to evolve and meet the next generation of energy management demands.