The art of lost wax casting, a process dating back thousands of years, has become indispensable in modern manufacturing. This enduring technique shapes everything from intricate jewelry pieces to robust industrial parts. By melding traditional craftsmanship with cutting-edge technology, lost wax casting offers a unique solution for manufacturers seeking precision and versatility.
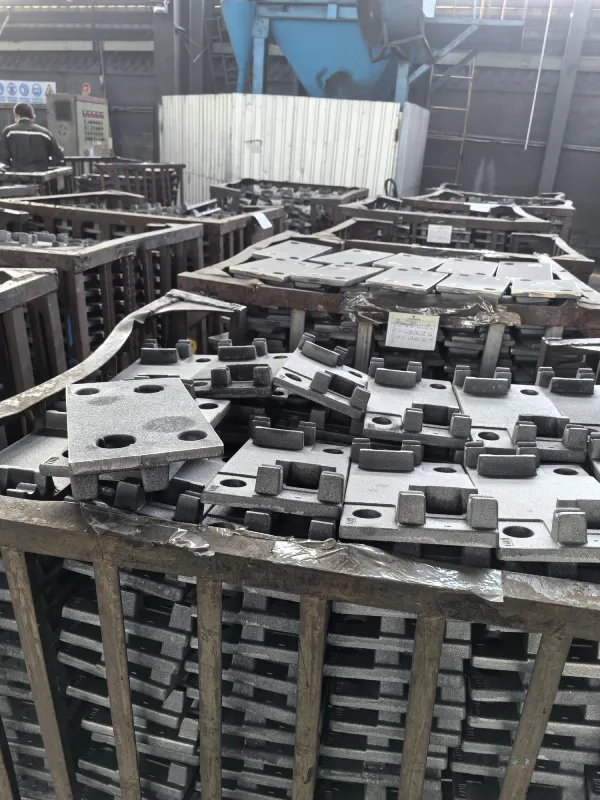
A thorough understanding of lost wax casting begins with recognizing its core components a wax model, ceramic mold, and molten metal. The process initiates by creating a detailed wax replica of the final piece. This wax model is then encased in a ceramic material, forming a mold. After the wax is melted away—leaving behind a hollow design—the mold is filled with molten metal. The outcome is a meticulously crafted metal part that mirrors the original wax configuration.
Precision remains a hallmark benefit of lost wax casting. Manufacturers often select this process when producing components that demand high accuracy and tight tolerances. The ability to craft complex geometries with minimal material waste makes it an appealing option for various industries, including aerospace, automotive, and medical devices.
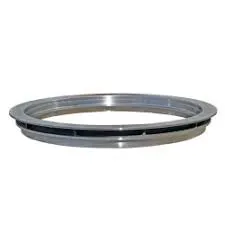
Expertise in lost wax casting is crucial for ensuring the best outcomes. High-quality production hinges on several factors, such as the selection of suitable wax, the finesse of the mold-making technique, and precise temperature control during metal pouring. Professionals in the field leverage their extensive experience to optimize these variables, thereby ensuring superior quality and dimensional accuracy.
In the context of authority and trustworthiness, established foundries boast a legacy of excellence and reliability. Reputed firms often provide comprehensive support throughout the casting process, guiding clients from initial design to finished product. These experienced manufacturers not only meet industry standards but also often exceed expectations by investing in cutting-edge technology and continuous process improvement.
lost wax casting parts
Lost wax casting is experiencing a resurgence as industries demand more customized, reliable, and durable parts. This technique is particularly advantageous for limited production runs or one-of-a-kind items, offering economically viable solutions without compromising on quality.
Furthermore, the process is environmentally friendly, as it involves recyclable materials and reduces waste. Many firms have adopted sustainable practices, such as reclaiming wax and recycling metal scraps, thus aligning with contemporary eco-friendly and sustainable manufacturing trends.
To fully appreciate the advantages of lost wax casting, consider testimonials from industry leaders who have successfully integrated this method into their operations. These real-world applications not only underscore the method's versatility but also highlight the transformative impact of precision casting on enhancing product performance and lifespan.
For businesses looking to incorporate lost wax casting into their manufacturing repertoire, partnering with a seasoned expert is essential. Such collaboration ensures not only technical execution but also strategic insights that can lead to significant cost savings and process efficiencies.
In summary, lost wax casting is more than a practical method—it's a convergence of art and engineering that meets the demanding needs of modern manufacturing. Expertise in the process fosters innovation and reliability, offering businesses an authoritative and trustworthy path to quality production.