Ductile Iron Casting Manufacturer A Comprehensive Guide
Ductile iron casting is a specialized manufacturing process that produces strong and durable metal components with excellent mechanical properties. These castings are widely used in various industries due to their high strength-to-weight ratio, good corrosion resistance, and excellent machinability. In this article, we will provide a comprehensive guide to ductile iron casting manufacturers, including their processes, materials, applications, and benefits.
Process of Ductile Iron Casting
The process of ductile iron casting involves the following steps
1. Melting Iron ore, coke, and limestone are melted in a blast furnace to produce molten iron.
2. Nodularization The molten iron is treated with magnesium or other nodulizing agents to form graphite nodules, which improve the ductility and toughness of the cast iron.
3. Molding The molten iron is poured into molds made of sand, ceramic, or other materials. The mold is designed to produce the desired shape and size of the casting.
4. Solidification The molten iron cools and solidifies in the mold, forming a solid casting.
5. Cleaning and Finishing The casting is then cleaned and finished to remove any excess material and achieve the desired surface finish.
Materials Used in Ductile Iron Casting
Ductile iron casting is typically made from cast iron with a high carbon content (around 3.5%) and silicon content (around 2%). The addition of magnesium or other nodulizing agents during the casting process helps to form graphite nodules, which improve the mechanical properties of the cast iron. Other elements such as manganese, chromium, and molybdenum may also be added to enhance specific properties of the casting.
Applications of Ductile Iron Casting
Ductile iron castings are widely used in various industries due to their excellent properties. Some common applications include
1. Automotive industry Engine blocks, transmission cases, cylinder heads, and other engine components Automotive industry Engine blocks, transmission cases, cylinder heads, and other engine components
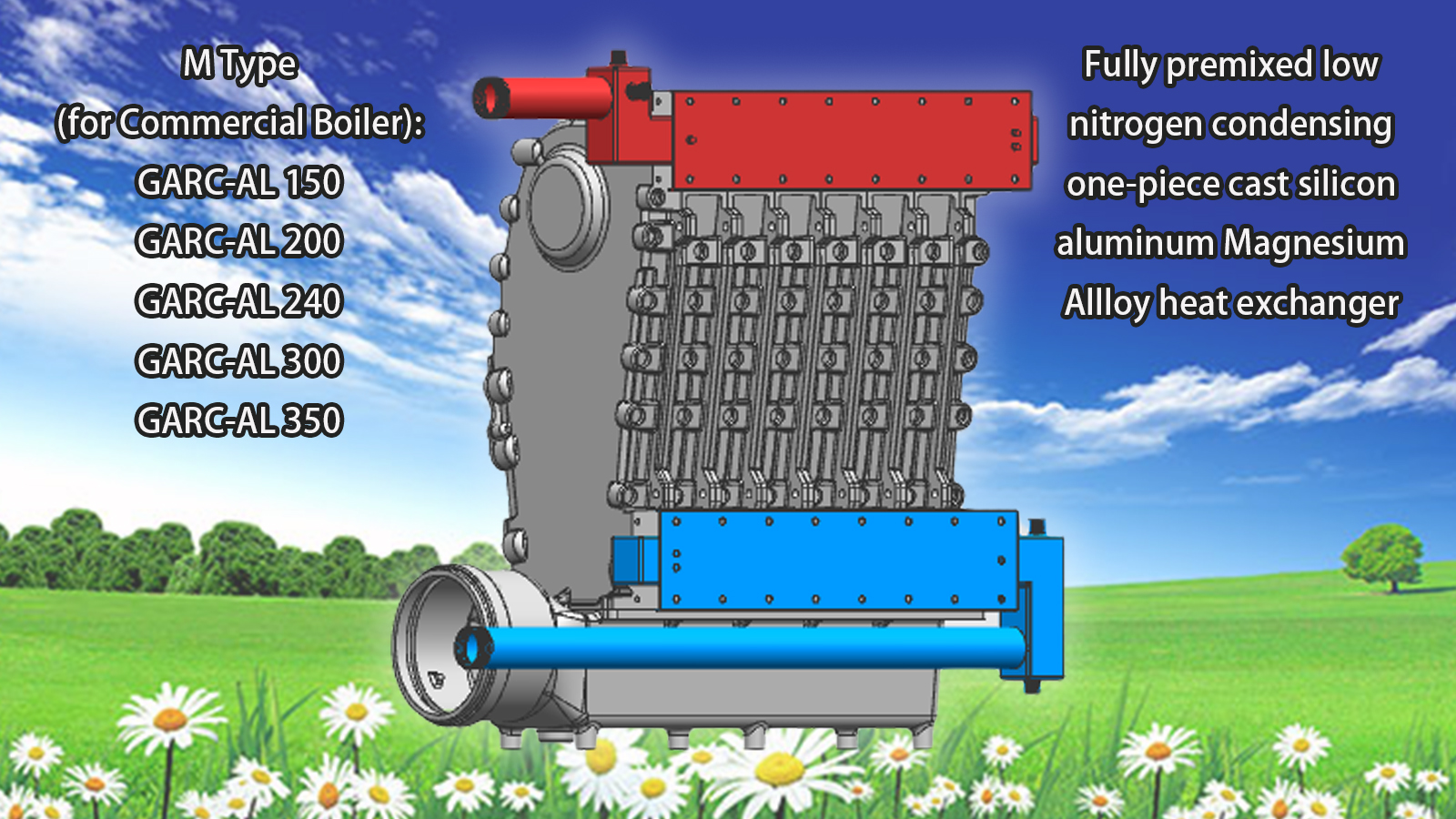
Automotive industry Engine blocks, transmission cases, cylinder heads, and other engine components Automotive industry Engine blocks, transmission cases, cylinder heads, and other engine components
ductile iron casting manufacturer.
2. Construction industry Manhole covers, pipe fittings, and other structural components.
3. Machinery industry Gearboxes, bearings, pumps, and other machine components.
4. Oil and gas industry Valves, pipes, and other equipment used in oil and gas production and transportation.
5. Aerospace industry Structural components, landing gear, and other aircraft parts.
Benefits of Ductile Iron Casting
Ductile iron casting offers several benefits over other casting processes, including
1. High strength and toughness The presence of graphite nodules in ductile iron castings provides excellent strength and toughness, making them suitable for demanding applications.
2. Good corrosion resistance The high carbon content in ductile iron provides good corrosion resistance, making it suitable for outdoor and harsh environments.
3. Excellent machinability Ductile iron castings can be easily machined, making them suitable for complex shapes and tight tolerances.
4. Cost-effective Compared to other materials such as steel and aluminum, ductile iron casting is relatively inexpensive and offers good value for money.
In conclusion, ductile iron casting is a versatile and cost-effective manufacturing process that produces strong and durable metal components with excellent mechanical properties. With its wide range of applications and benefits, ductile iron casting continues to play a crucial role in various industries.