Aluminium Die Casting A Comprehensive Guide
Introduction
Aluminium die casting is a manufacturing process that involves pouring molten aluminium into a steel die to create complex shapes and components with high dimensional accuracy and surface finish. This versatile process is widely used in various industries due to its ability to produce parts with excellent mechanical properties, good corrosion resistance, and lightweight design. In this article, we will provide a comprehensive guide to aluminium die casting, including its process, materials, applications, and benefits.
Process of Aluminium Die Casting
The aluminium die casting process consists of several key steps, including
1. Design and Preparation of Dies The first step in the process is to create a detailed design of the component using computer-aided design (CAD) software. The design must take into account the material flow, shrinkage, and cooling requirements to ensure the final part meets the required specifications. Once the design is complete, the dies are fabricated from high-quality tool steel and machined to precise dimensions.
2. Melting and Pouring The next step is to melt the aluminium ingots in a crucible furnace at high temperatures. The molten aluminium is then transferred to a holding furnace, where it is held at a constant temperature until it is ready for pouring. The molten aluminium is poured into the die cavity through a sprue and runner system, which distributes the metal evenly throughout the die.
3. Solidification and Cooling As the molten aluminium cools and solidifies within the die, it takes on the shape of the die cavity. The cooling process is critical to producing parts with the desired dimensional accuracy and surface finish. The dies are designed with cooling channels to control the cooling rate and ensure uniform shrinkage.
4. Part Removal and Finishing After the metal has solidified and cooled, the die is opened and the part is removed. The part may require additional finishing operations such as trimming, machining, or surface treatment to meet specific requirements.
Materials Used in Aluminium Die Casting
Aluminium die casting can be performed using a variety of aluminium alloys, each with its own unique properties and applications. Some of the most commonly used alloys include
1. A356 This alloy is a popular choice for general-purpose die casting due to its good castability, moderate strength, and excellent corrosion resistance.
2. A380 This alloy offers higher strength and hardness than A356, making it suitable for applications requiring higher mechanical properties.
3
3
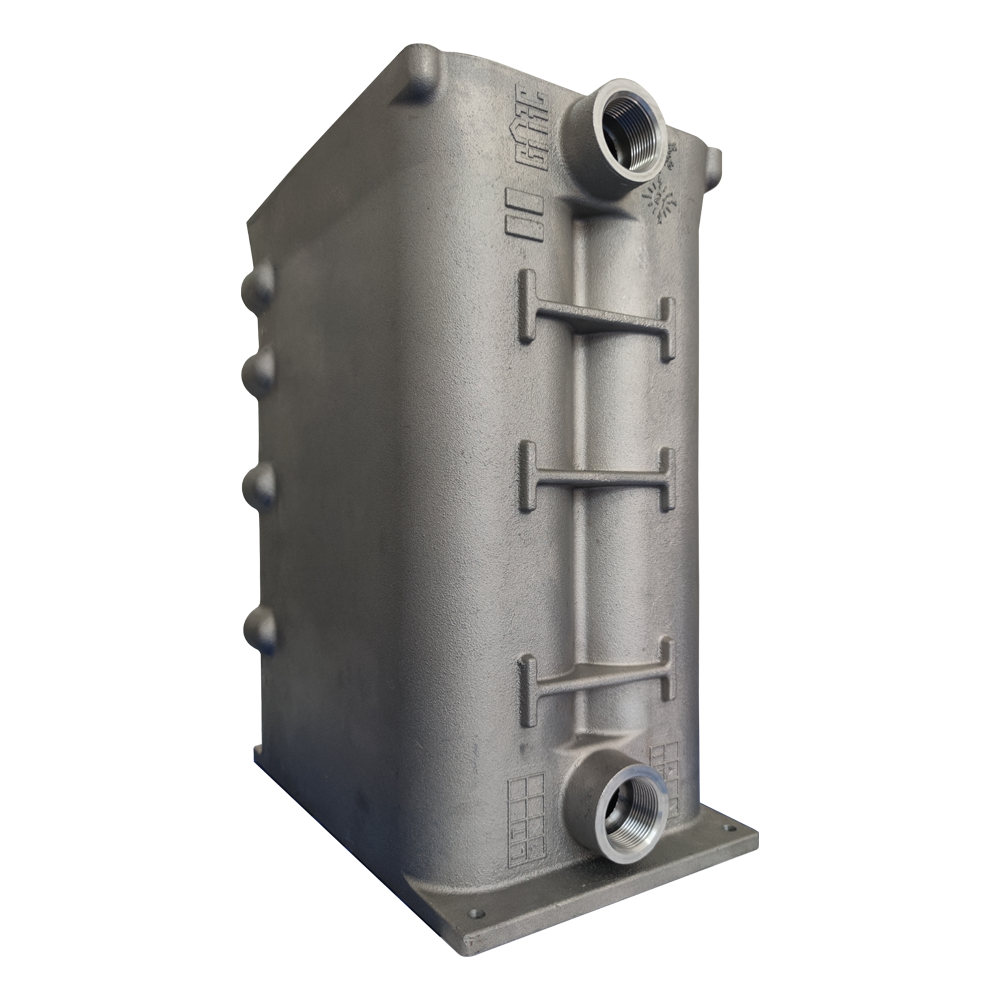
3
3
aluminium die. ZL101 This alloy is known for its excellent castability, high strength, and good wear resistance, making it ideal for automotive and aerospace components.
Applications of Aluminium Die Casting
Aluminium die casting is used in a wide range of industries due to its versatility and ability to produce complex shapes and components. Some of the most common applications include
1. Automotive Die-cast aluminium parts are commonly used in engines, transmission cases, and other automotive components due to their lightweight design and excellent mechanical properties.
2. Electronics Die-cast aluminium enclosures and components are used in consumer electronics, such as smartphones, laptops, and gaming consoles, due to their excellent heat dissipation and protection against electromagnetic interference.
3. Electrical Die-cast aluminium components are used in electrical equipment, such as transformers, circuit breakers, and motor housings, due to their good electrical conductivity and corrosion resistance.
4. Aerospace Die-cast aluminium parts are used in aircraft engines, landing gear, and other critical components due to their high strength and light weight.
Benefits of Aluminium Die Casting
There are several benefits to using aluminium die casting for manufacturing components, including
1. High Dimensional Accuracy Die casting produces parts with tight tolerances and excellent surface finish, making them suitable for precision applications.
2. Efficient Production The die casting process is highly automated and can produce large quantities of parts in a short time, making it an efficient manufacturing method.
3. Cost-Effective Die casting can be more cost-effective than other manufacturing processes, especially for complex shapes and components, due to its ability to produce parts with fewer secondary operations.
4. Lightweight Design Die-cast aluminium parts are much lighter than cast iron or steel parts, making them ideal for applications where weight is a critical factor.
5. Excellent Mechanical Properties Die-cast aluminium parts offer excellent mechanical properties, including high strength, hardness, and good wear resistance.
Conclusion
Aluminium die casting is a versatile and efficient manufacturing process that produces complex shapes and components with high dimensional accuracy and excellent mechanical properties. Its wide range of applications and benefits make it an attractive option for manufacturers in various industries.