The Versatile World of Aluminum-Magnesium Alloy Casting
Aluminum-magnesium alloy casting is a sophisticated metallurgical process that combines the lightweight properties of aluminum with the strength and durability of magnesium. This fusion results in an advanced material, offering superior performance characteristics for numerous applications ranging from automotive to aerospace industries.
The science behind aluminum-magnesium alloy casting is intricate and demands precision. The process begins with meticulously selecting raw materials based on the desired properties of the end product. Aluminum and magnesium are carefully proportioned, often with additional elements such as zinc, copper, or silicon added to fine-tune the alloy's strength, hardness, and corrosion resistance.
Once the ingredients are mixed according to specific ratios, the alloy is prepared for casting. There are several casting methods, including sand casting, die casting, and permanent mold casting, each with its own advantages and suited for different requirements. Die casting, for instance, is favored for high-volume production due to its precision and repeatability.
During the casting process, temperatures and cooling rates must be closely monitored to prevent defects such as porosity or hot tearing. The molten alloy is poured into pre-made molds where it solidifies and takes the desired shape The molten alloy is poured into pre-made molds where it solidifies and takes the desired shape
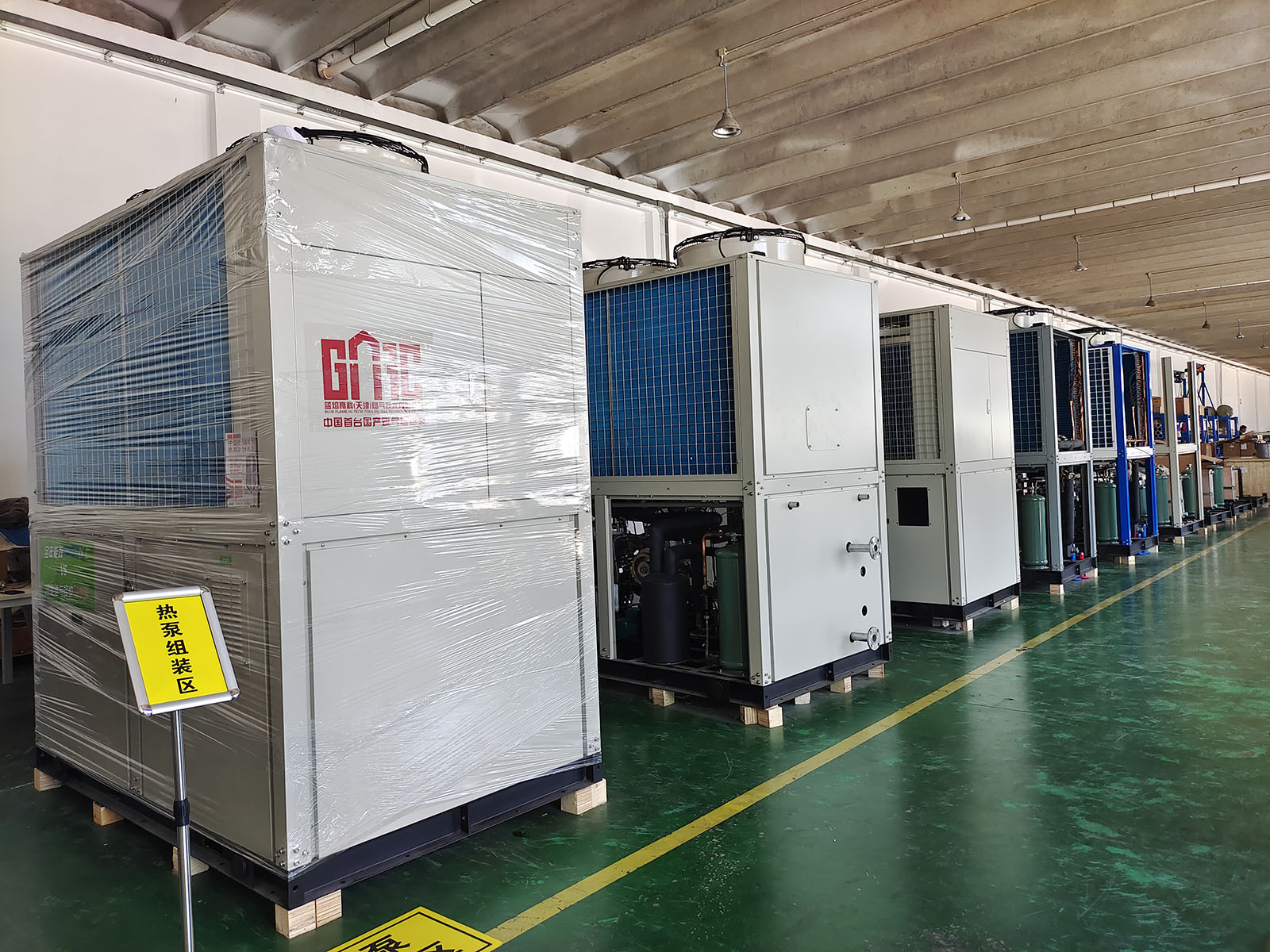
The molten alloy is poured into pre-made molds where it solidifies and takes the desired shape The molten alloy is poured into pre-made molds where it solidifies and takes the desired shape
aluminum-magnesium alloy casting. The cooling phase is critical; rapid cooling can lead to stress within the material, while slower cooling might result in a coarser grain structure affecting the alloy’s strength.
One of the significant benefits of aluminum-magnesium alloys is their excellent strength-to-weight ratio. These alloys are much lighter than traditional metals yet maintain comparable strength, making them ideal for weight-sensitive applications like aircraft components and automobile parts. Furthermore, they exhibit good corrosion resistance and can withstand harsh environmental conditions, expanding their utility in marine applications and outdoor architectural elements.
In conclusion, aluminum-magnesium alloy casting stands at the forefront of modern materials science, pushing boundaries with its unique blend of lightness, toughness, and adaptability. As technology continues to evolve, so too will the refinement of these alloys, promising even more innovative uses across various sectors. The future of design and engineering is being shaped, one cast at a time, by the remarkable properties of aluminum-magnesium alloys.