The Aluminum Melt Temperature A Crucial Factor in the Metal Casting Industry
The aluminum melt temperature is a critical parameter that significantly influences various aspects of the metal casting process. This temperature, which typically ranges from 650°C to 950°C, depending on the alloying elements present in the aluminum alloy, must be carefully controlled to ensure the quality and integrity of the final cast product.
At lower temperatures, the viscosity of the molten aluminum increases, making it more difficult to pour into molds and leading to defects such as cold shuts and misruns. On the other hand, higher temperatures can cause the aluminum to oxidize more rapidly, leading to the formation of dross and reducing the yield of pure aluminum. Additionally, excessive heat can also lead to the decomposition of the alloy, releasing gases that can form voids or pores in the castings.
Therefore, it is essential to maintain the aluminum melt temperature within a narrow range to optimize the casting process. This can be achieved through the use of sophisticated temperature control systems that monitor and adjust the temperature in real-time based on feedback from thermocouples or other temperature sensors. These systems can also be programmed to automatically compensate for variations in the input power or furnace design that may affect the melt temperature These systems can also be programmed to automatically compensate for variations in the input power or furnace design that may affect the melt temperature
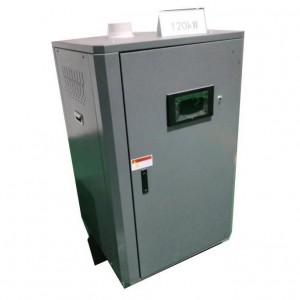
These systems can also be programmed to automatically compensate for variations in the input power or furnace design that may affect the melt temperature These systems can also be programmed to automatically compensate for variations in the input power or furnace design that may affect the melt temperature
aluminum melt temperature.
In addition to its impact on the casting process, the aluminum melt temperature also plays a crucial role in determining the properties of the final cast product. For example, increasing the melt temperature can increase the fluidity of the aluminum, allowing it to fill molds more completely and resulting in castings with better surface finish and dimensional accuracy. However, too high a temperature can also lead to the loss of some of the alloy's strength and hardness, as well as an increase in its susceptibility to corrosion.
In conclusion, the aluminum melt temperature is a critical factor that must be carefully controlled in the metal casting industry to ensure the quality and integrity of the final cast product. By using sophisticated temperature control systems and optimizing the casting process, manufacturers can produce castings with superior properties and reduce waste and rework.