Copper Sand Casting A Comprehensive Guide
Copper sand casting is a popular metal casting process that involves pouring molten copper into a mold made of sand. This method is widely used due to its versatility, cost-effectiveness, and ability to produce complex shapes. In this article, we will delve into the basics of copper sand casting, including its history, materials, processes, and applications.
History of Copper Sand Casting
The origins of copper sand casting can be traced back thousands of years ago. Early civilizations, such as the Egyptians and the Mesopotamians, used this technique to create intricate sculptures, jewelry, and tools. Over time, the process evolved, and it is now used in a variety of industries, including automotive, aerospace, and electronics.
Materials Used in Copper Sand Casting
Copper sand casting requires two main materials copper and sand. The choice of copper depends on the desired properties of the final product. For example, pure copper is used for its excellent electrical conductivity, while brass is used for its resistance to corrosion.
Sand, on the other hand, serves as the mold material. It must have the right combination of permeability, thermal conductivity, and strength to withstand the high temperatures involved in the casting process. Silica sand is the most commonly used type of sand due to its affordability and availability.
Processes Involved in Copper Sand Casting
The copper sand casting process consists of several steps, including
1. Mold Preparation A pattern is created using wax, plastic, or another material that can be melted or dissolved away after the casting is complete. This pattern is then coated with a layer of refractory material, such as silica sand, to create a mold.
2. Mold Assembly The various parts of the mold are assembled around the pattern. This can be done using metal pins, screws, or other fasteners This can be done using metal pins, screws, or other fasteners
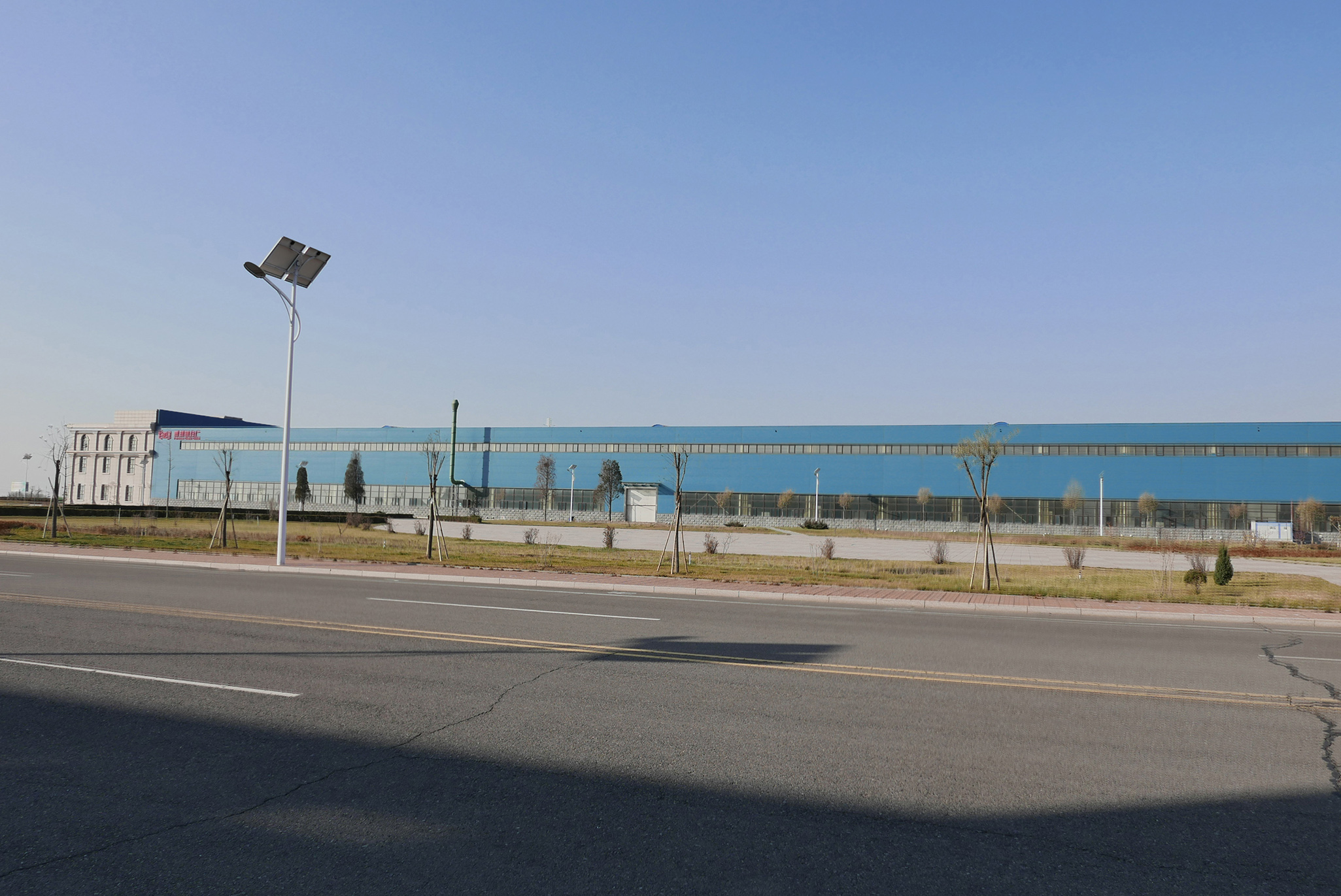
This can be done using metal pins, screws, or other fasteners This can be done using metal pins, screws, or other fasteners
copper sand casting manufacturers.
3. Pouring The molten copper is poured into the mold at a temperature of around 1083°C (2000°F). The mold is designed to allow the copper to flow evenly and fill all areas of the mold.
4. Solidification As the copper cools and solidifies, it takes the shape of the mold. The refractory material maintains its shape throughout the process.
5. Mold Removal Once the copper has cooled and solidified completely, the mold is broken apart, and the casting is removed. Any remaining wax or plastic patterns are also removed.
6. Finishing The casting is then cleaned, trimmed, and finished to meet specific requirements. This may involve grinding, polishing, or plating to improve its appearance and performance.
Applications of Copper Sand Casting
Copper sand casting is used in a wide range of applications due to its versatility and cost-effectiveness. Some of the most common uses include
* Electrical components, such as connectors, switches, and relays
* Heat exchangers and radiators
* Plumbing fixtures and fittings
* Decorative items, such as statues and sculptures
* Automotive parts, such as engine blocks and transmission casings
In conclusion, copper sand casting is a versatile and cost-effective metal casting process that has been used for thousands of years. By understanding the history, materials, processes, and applications of this technique, manufacturers can make informed decisions when selecting this method for their production needs.