Casting is an age-old manufacturing process that has been refined over centuries to become an indispensable method in various industries, including automotive, aerospace, construction, and even art. The term CI Casting Products specifically refers to products made using Cast Iron (CI) casting, a subset of casting processes that offers unique advantages due to the properties of cast iron. This article delves into the nuances of CI casting, its applications, and the reasons behind its continued prevalence in modern manufacturing.
**Introduction to CI Casting**
Cast iron, known for its high carbon content, excellent machinability, and wear resistance, is a popular choice for casting applications that require strength without the need for extreme ductility. CI casting involves pouring molten iron into a mold, allowing it to cool and solidify, and then extracting the finished product. The process can be further categorized into green sand casting, shell molding, investment casting, and several other techniques, each tailored to specific product requirements and production volumes.
**Advantages of CI Casting Products**
1. **Strength and Durability** Cast iron products exhibit high compressive strength, making them ideal for applications that involve heavy loads or stress, such as engine blocks, machine tool parts, and building components like pipes and manhole covers.
2. **Economic Efficiency** The abundance of iron and relatively low cost of production make CI casting an economically viable option compared to other materials like steel or aluminum. It allows for the creation of complex shapes with minimal waste, reducing overall production costs.
3. **Excellent Machinability** Cast iron's structure facilitates easier machining, enabling the production of intricate designs and tight tolerances. This characteristic is particularly beneficial for parts requiring precision engineering.
4
4
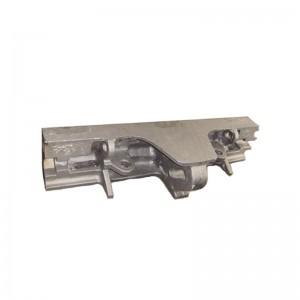
4
4
ci casting products. **Heat Resistance and Thermal Conductivity** Cast iron's ability to withstand high temperatures and efficiently conduct heat makes it suitable for cookware, engine parts, and heat exchangers.
**Applications of CI Casting Products**
CI casting finds extensive use across diverse sectors
- **Automotive Industry** Engine blocks, cylinder heads, brake discs, and various transmission parts are commonly made from cast iron due to its durability and thermal properties.
- **Construction Industry** Drainage systems, pipes, valves, and structural components benefit from cast iron's strength and corrosion resistance.
- **Agriculture** Farm machinery parts, like those used in plows and harvesters, often utilize cast iron for its resilience against abrasive soil conditions.
- **Railway Infrastructure** Rails, switches, and crossing components are frequently cast in iron to endure heavy loads and harsh environments.
- **Decorative and Artistic Applications** From ornate gates and fence posts to sculptures, cast iron's aesthetic appeal and versatility make it a favorite among artists and architects.
**Challenges and Innovations**
While CI casting offers numerous advantages, challenges such as shrinkage, porosity, and the risk of cracking during cooling must be meticulously managed. Advancements in casting technology, including computer-aided design (CAD), 3D printing for mold creation, and the use of advanced alloys, have significantly improved product quality and process efficiency.
Moreover, environmental concerns surrounding the high energy consumption and emissions associated with iron smelting and casting processes have driven research into more sustainable practices. Recycled iron usage and the implementation of cleaner production methods are becoming increasingly important in the industry.
In conclusion, CI casting products remain a cornerstone of modern manufacturing due to their inherent strengths, versatility, and cost-effectiveness. As technology progresses and sustainability becomes a central focus, the CI casting industry is poised for continuous evolution, ensuring its relevance and importance in the years to come. Through innovative techniques and a commitment to environmental responsibility, cast iron will continue to shape the world around us in countless functional and beautiful ways.