The Efficiency of Double Wall Shell and Tube Heat Exchangers
In the realm of industrial equipment, heat exchangers play a crucial role in managing thermal energy. Among various types, the double wall shell and tube heat exchanger stands out for its efficiency and versatility. This innovative design combines the robustness of a shell and tube configuration with an added layer of protection against leakage or contamination, making it suitable for applications requiring high standards of safety and cleanliness.
The operational principle of a double wall shell and tube heat exchanger is deceptively simple yet highly effective. It comprises two concentric walls around the tubes, creating an inner and outer layer separated by a sealed space. This construction not only strengthens the structural integrity of the unit but also provides an additional barrier to fluid cross-contamination. As fluids flow through the tubes and within the shell, heat is transferred between them without mixing, thanks to the double wall protection.
One significant advantage of this type of heat exchanger is its ability to handle pressure differentials effectively. The dual-walled tubes are designed to withstand substantial pressure variations, ensuring that the system can operate under demanding conditions without compromising its primary function—heat transfer. Furthermore, should there be a breach in the inner wall, the outer wall acts as a backup, preventing potential leakage from affecting the process fluids.
Maintenance is also streamlined in a double wall shell and tube heat exchanger. The design allows for straightforward inspection and cleaning procedures since the interior surfaces are accessible via the sealed space between the walls The design allows for straightforward inspection and cleaning procedures since the interior surfaces are accessible via the sealed space between the walls
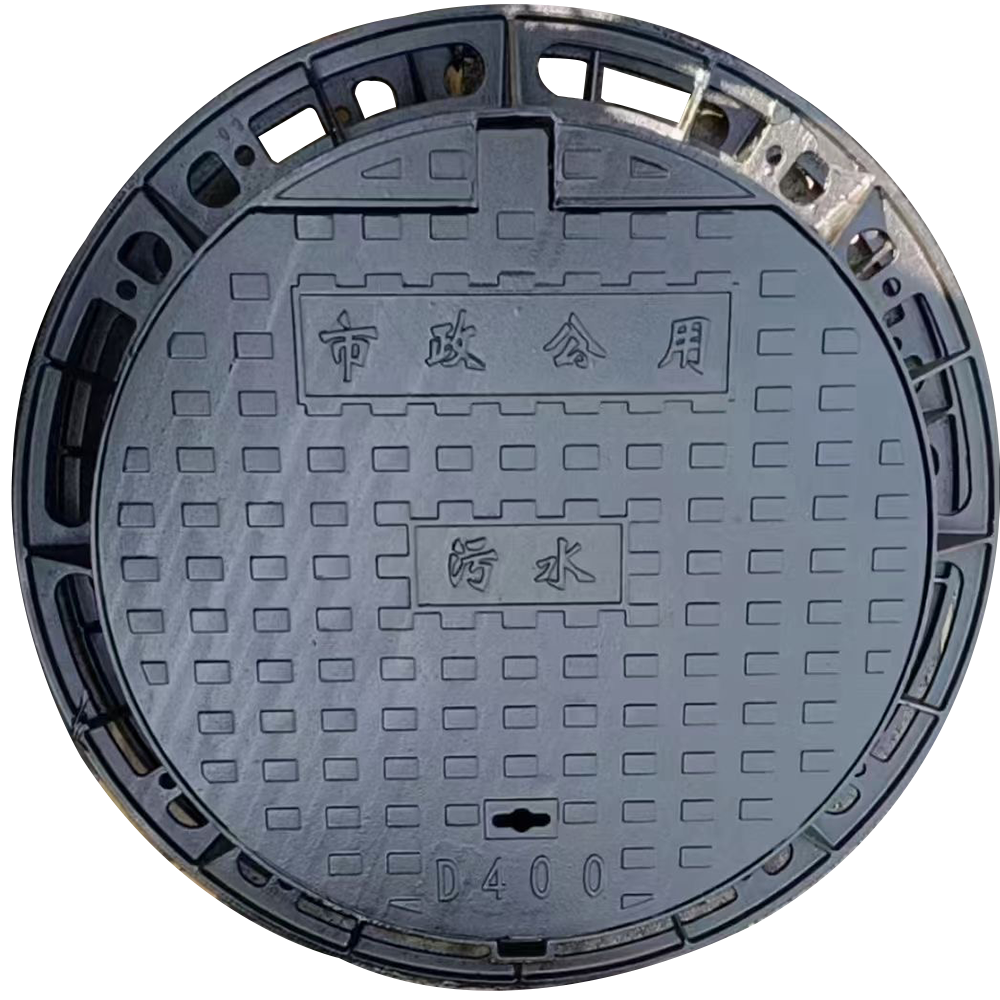
The design allows for straightforward inspection and cleaning procedures since the interior surfaces are accessible via the sealed space between the walls The design allows for straightforward inspection and cleaning procedures since the interior surfaces are accessible via the sealed space between the walls
double wall shell and tube heat exchanger. This feature is particularly valuable in environments where fouling or scaling is prevalent, as it enables regular upkeep to maintain optimal performance levels.
In terms of application, these heat exchangers are widely used in industries such as food processing, pharmaceuticals, and power generation. They are especially favored when dealing with sensitive materials or when strict hygiene standards must be adhered to. For instance, in milk pasteurization, the dual-walled system prevents contamination while efficiently heating and cooling the product.
Despite their complexity, double wall shell and tube heat exchangers offer a compelling blend of reliability, safety, and ease of maintenance. Their ability to provide an extra measure of protection without sacrificing heat transfer efficiency makes them an indispensable asset in processes where quality control and environmental protection are paramount. As technology evolves, we can expect further innovations that build upon this foundational design, enhancing both performance and operational safety in various sectors.
In conclusion, the double wall shell and tube heat exchanger is a testament to the continuous advancement in thermal management solutions. By integrating a secondary containment layer into the traditional shell and tube design, it has redefined the standards for safety, cleanliness, and efficiency in heat exchange processes. Its adoption across critical industries highlights its importance in maintaining operational integrity while ensuring environmental stewardship.