Dry Cast Reinforced Concrete Pipe Mould Pallets Innovations in Infrastructure Manufacturing
In the realm of infrastructure development and water management systems, the use of dry cast reinforced concrete pipe (DCRCP) has gained significant traction due to its durability, cost-effectiveness, and versatility. A pivotal component in the production process of these pipes is the dry cast reinforced concrete pipe mould pallet. This innovative technology not only streamlines manufacturing but also ensures the structural integrity of the pipes, contributing to robust and resilient infrastructure worldwide.
**Understanding Dry Cast Reinforced Concrete Pipes**
DCRCPs are widely utilized for various applications, including stormwater drainage, sewage systems, and culverts. Their strength lies in the combination of high-quality concrete with carefully placed reinforcement, typically steel bars or spirals, which enhance load-bearing capabilities and resistance to corrosion. Unlike wet casting, the dry cast method involves compacting concrete into a mould under low moisture conditions, resulting in faster curing times and increased efficiency.
**The Role of Mould Pallets**
At the heart of DCRCP production lies the mould pallet system. These specially designed pallets serve as the foundation upon which the pipe sections are formed. They are typically made from sturdy materials like steel or high-density polyethylene (HDPE), ensuring they can withstand the pressures of the casting process and repeated use without deformation.
Mould pallets are engineered with precision to create the desired pipe dimensions, complete with internal cavities for reinforcement placement. They often feature modular designs, allowing for the manufacture of pipes in various diameters and lengths, thus enhancing versatility in production. Quick-release mechanisms are incorporated to facilitate efficient demolding once the concrete has cured, minimizing downtime and increasing production output.
**Innovative Features and Benefits**
1. **Efficiency and Speed** Dry cast methods, coupled with the use of well-designed mould pallets, significantly reduce production time compared to traditional wet casting techniques. This acceleration in manufacturing allows for a higher volume of pipes to be produced daily, meeting the growing demands of infrastructure projects This acceleration in manufacturing allows for a higher volume of pipes to be produced daily, meeting the growing demands of infrastructure projects
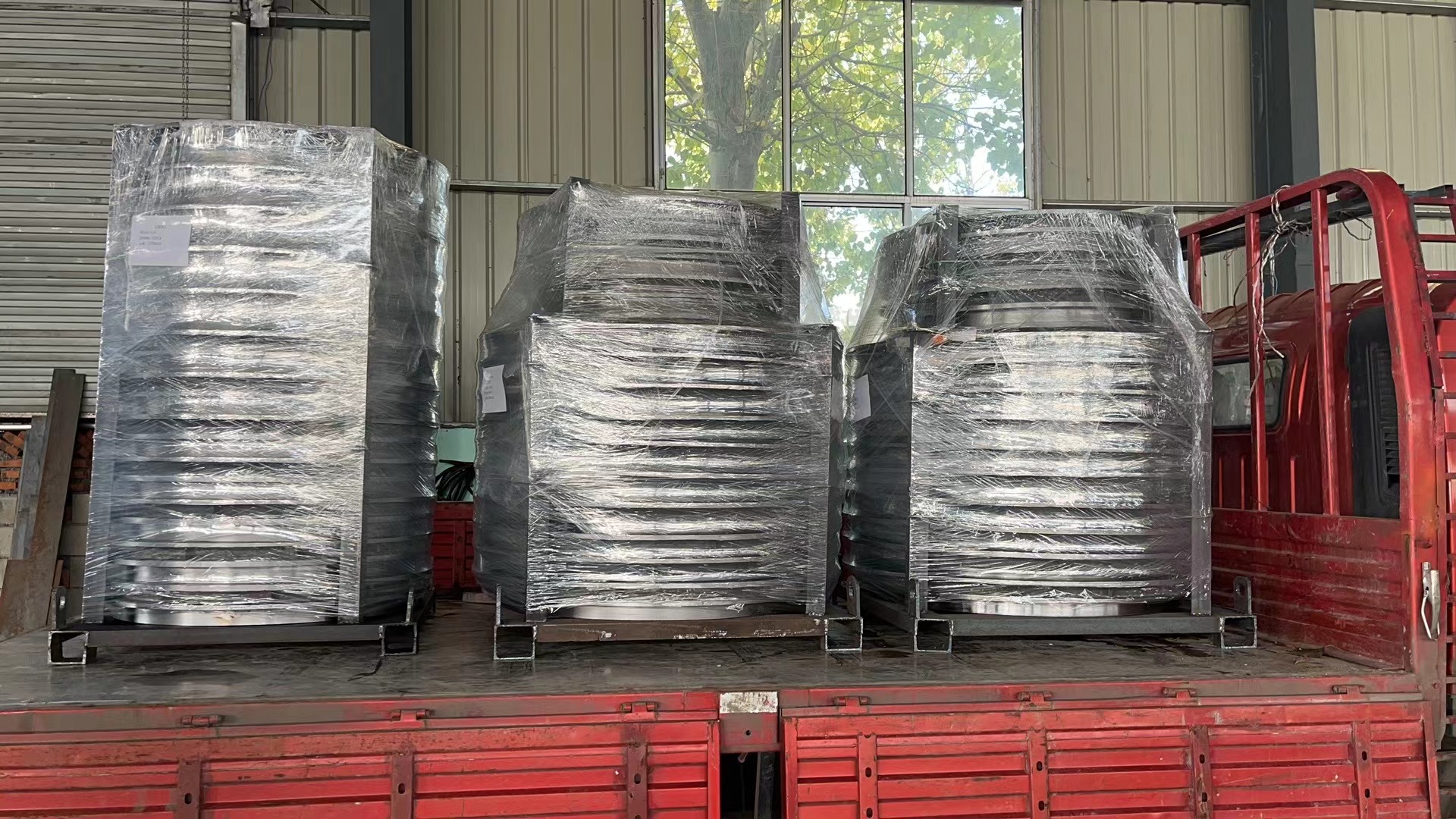
This acceleration in manufacturing allows for a higher volume of pipes to be produced daily, meeting the growing demands of infrastructure projects This acceleration in manufacturing allows for a higher volume of pipes to be produced daily, meeting the growing demands of infrastructure projects
dry cast reinfored concrete pipe mould pallet.
2. **Consistency and Quality** Automated or semi-automated mould systems ensure each pipe is manufactured to exact specifications, guaranteeing uniformity in diameter, wall thickness, and reinforcement positioning. This consistency translates into pipes that meet or exceed industry standards for performance and longevity.
3. **Cost-Effectiveness** Although the initial investment in a dry cast system and high-quality mould pallets may be substantial, the long-term savings derived from reduced labor costs, faster production cycles, and minimal material waste make it a cost-effective solution over time.
4. **Environmental Sustainability** The dry cast process consumes less water than wet casting, reducing environmental impact. Additionally, the durable nature of DCRCPs means they require less frequent replacement, contributing to sustainable infrastructure practices.
5. **Customization and Adaptability** Mould pallets can be tailored to incorporate specific design features such as joints, bells, or linings, enabling the production of specialized pipes suited for unique project requirements.
**Conclusion**
The adoption of dry cast reinforced concrete pipe mould pallet technology underscores a progressive shift in the infrastructure manufacturing sector towards enhanced productivity, quality assurance, and sustainability. By leveraging these advanced systems, manufacturers can efficiently produce pipes that stand the test of time, playing a vital role in building resilient cities and communities. As urbanization continues to escalate and the need for robust water management systems grows, the strategic implementation of DCRCP mould pallet technologies becomes increasingly crucial in shaping the future of infrastructure development.