The Importance of Heat Exchangers in Low Nitrogen Condensing Boiler Factories
In the realm of modern industrial processes, efficiency and environmental sustainability are paramount. One key technology that has emerged to address these concerns is the heat exchanger, particularly in the context of low nitrogen condensing boiler factories. These facilities have revolutionized the way we generate heat, significantly reducing nitrogen oxide emissions while maximizing energy efficiency.
A heat exchanger is a vital component in a low nitrogen condensing boiler system. It functions by transferring thermal energy from one medium to another without allowing the fluids to mix. In the case of these boilers, it facilitates the transfer of heat from the combustion gases to the water or steam, thereby extracting the maximum possible energy before the gases are vented.
Low nitrogen condensing boilers are designed with advanced heat exchanger technology to achieve higher thermal efficiency and lower NOx emissions. The unique design of these exchangers allows for the cooling of flue gases to very low temperatures, causing the water vapor within them to condense. This process not only recovers latent heat that would otherwise be lost but also reduces the formation of nitrogen oxides (NOx), a major contributor to air pollution.
The use of high-efficiency heat exchangers in these factories offers numerous benefits. Firstly, they increase the overall efficiency of the boiler, as more heat is extracted from the fuel, leading to reduced fuel consumption Firstly, they increase the overall efficiency of the boiler, as more heat is extracted from the fuel, leading to reduced fuel consumption
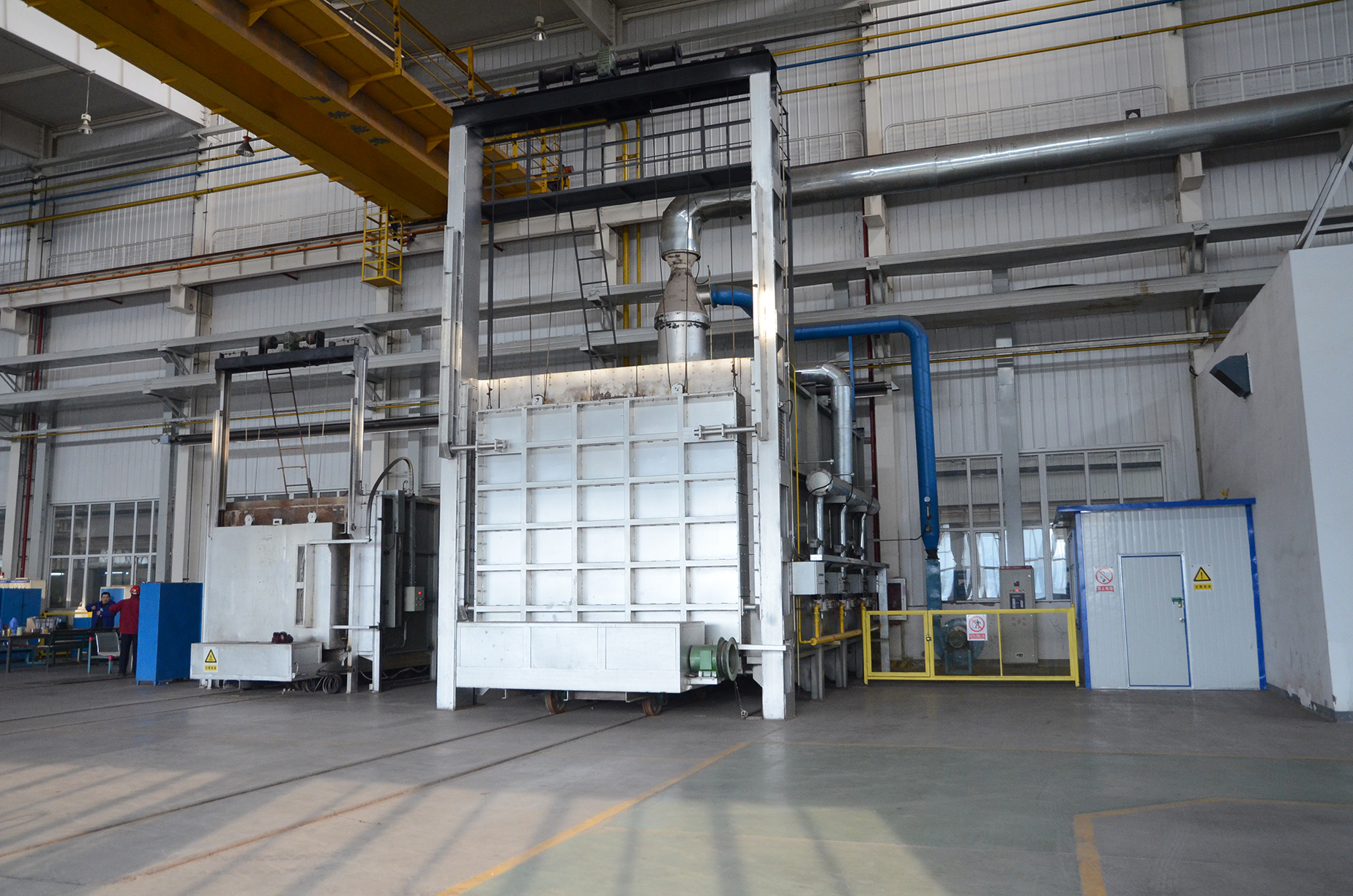
Firstly, they increase the overall efficiency of the boiler, as more heat is extracted from the fuel, leading to reduced fuel consumption Firstly, they increase the overall efficiency of the boiler, as more heat is extracted from the fuel, leading to reduced fuel consumption
heat exchanger for low nitrogen condensing boiler factories. Secondly, the condensation of flue gases helps to lower the flue gas temperature, which in turn reduces NOx emissions. This aligns with global efforts to mitigate climate change and adhere to stringent environmental regulations.
Moreover, the design of these heat exchangers often incorporates materials resistant to corrosion caused by acidic condensate, ensuring longevity and reliability. Regular maintenance and cleaning of the exchanger surfaces are crucial to maintaining optimal performance and preventing blockages.
In conclusion, the heat exchanger plays an instrumental role in the operation of low nitrogen condensing boiler factories. Its ability to enhance efficiency, minimize environmental impact, and contribute to sustainable energy practices underscores its significance in today's industrial landscape. As technology continues to evolve, we can expect even more innovative heat exchanger designs that will further optimize boiler performance and reduce our carbon footprint. The future of heating lies in the intelligent integration of such technologies, and low nitrogen condensing boiler factories, with their advanced heat exchangers, are at the forefront of this revolution.